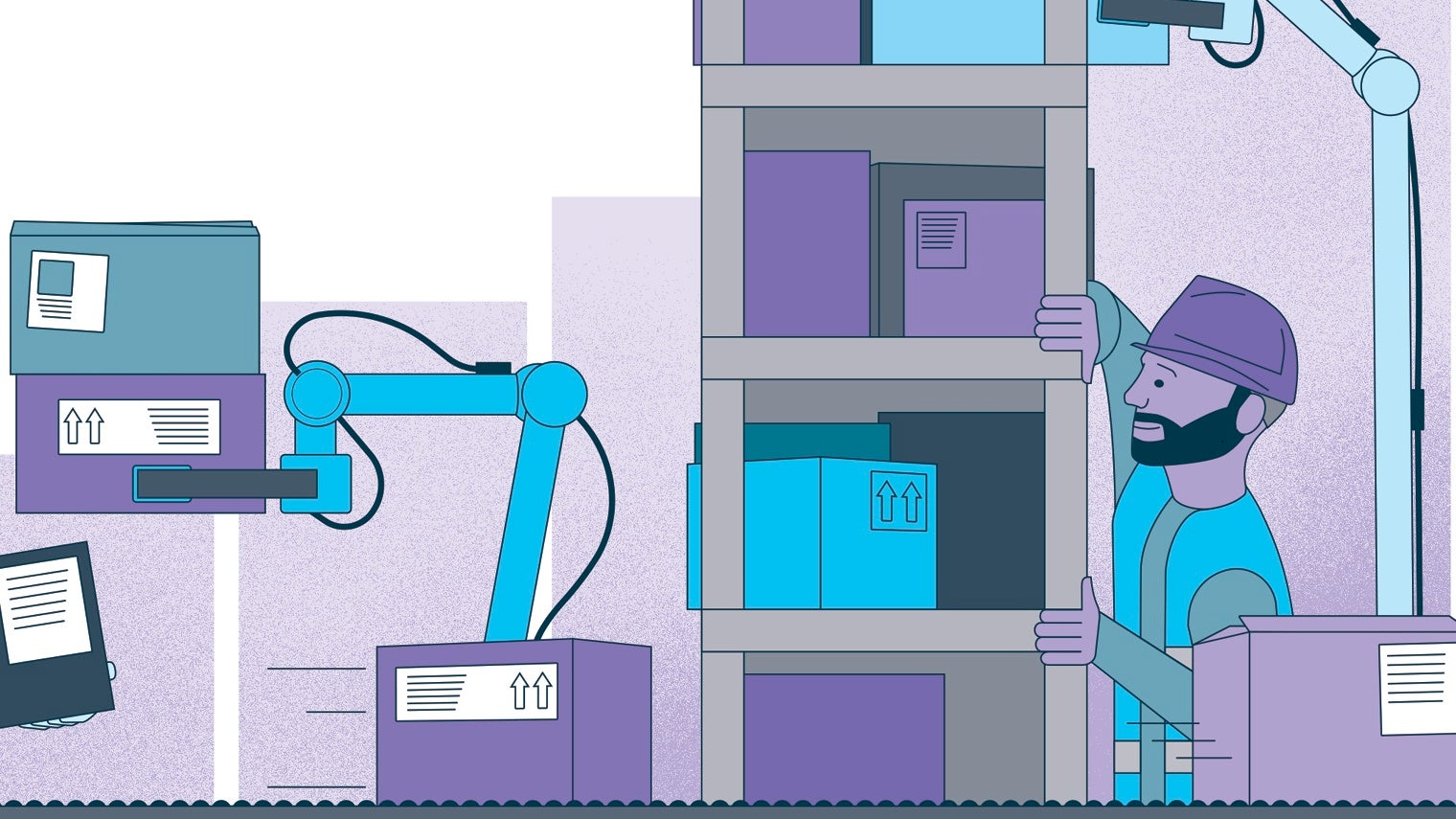
The nation’s shift towards online shopping at the start of the Covid crisis “accelerated five years of change into just five weeks. It has created demand for stock that is set to last long after the pandemic.”
That’s the prediction of Dave Ashwell, who, as managing director of AO Logistics, knows what he’s talking about. Online electricals retailer AO has acquired more than 45,000m2 of warehousing space across Cheshire and Staffordshire in recent months, in line with many other etailers that are investing in hi-tech facilities in their effort to keep the supply of goods up with demand.
AO Logistics’ new warehouse in Stoke-on-Trent features voice-picking technology, which ensures that “the right goods are loaded in the correct sequence, improving speed and accuracy”, Ashwell says. “Our people wear headsets, meaning that they no longer need to carry around a pen and paper. This leaves them with both hands free to lift items safely. We hope that it will significantly reduce the amount of paper we use here too.”
The social distancing constraints of the pandemic have also accelerated the adoption of goods-to-person (G2P) systems. The use of this technology is set to quadruple before 2024, according to Gartner.
These systems feature robots, which retrieve items from storage and bring them to a human picker to decide where to put them.
For most of the year I have, say, 50 robots – and that’s good enough; it gets the work done. But for the Christmas rush I could scale that up to 500
“You let the robot do what the robot is good at: the things that really waste a person’s time,” says Dwight Klappich, research vice-president with Gartner’s supply-chain practice.
In the past, he says, the benefits of automation were limited, because of the high cost of the technology, the considerable time required to implement it and the fact that each machine could perform only one function. Today, though, the emergence of more flexible, intelligent robots is making it more viable.
“Robots are significantly less expensive and have a shorter payback period than conventional automation,” Klappich explains. “I can bring a robot in fairly quickly, set it up, test it out and evaluate several use cases. It can be in production within months, if not weeks.”
Using a mix of traditional automation and newer robotic systems requires complex management systems. Gartner predicts that, by 2024, half of all organisations in the supply management sector will invest in applications that support artificial intelligence and advanced analytics capabilities.
You let the robot do what the robot is good at: the things that really waste a person’s time
One company taking advantage of such systems is Nestlé. Together with transport and logistics firm XPO Logistics, it has recently opened a distribution centre in Leicestershire. The site uses advanced robotics alongside automated systems developed in collaboration with Swisslog.
An automated monorail brings pallets into the facility, where they are stacked by 31m-high cranes. The pallets are then broken down automatically into smaller case units for storage.
“One of the major benefits of this automation is its ability to make up bespoke orders,” says James Sharples, MD of Swisslog UK. “For example, a customer may not want to order a whole pallet of Kit Kats. It might instead want a mixed selection of products – known as a rainbow pallet.”
These are assembled to order using a combination of gantry robots and another robot-based system that Swisslog has developed. Meanwhile, state-of-the-art software synchronises both automated and human processes across the facility, collecting and analysing data to determine where refinements can be made.
“As we implement more technology, we get more data from it,” says Andrew Shaw, director of the supply chain for Nestlé in the UK and Ireland. “We’re looking at how that data can be used and also at how it can be combined with existing data to provide the real-time information that we need to improve safety, efficiency and customer service.”
Klappich believes that continuing labour shortages in the sector will prompt greater automation in warehouses and fulfilment centres, with most large companies building diverse fleets of robots in the longer term.
“You don’t want to use a robot that can move heavy loads for in-aisle picking, for instance,” he explains. “It’ll be more costly to operate because it has a bigger motor and bigger wheels – it’s going to be hefty. You want a smaller, less expensive robot for that task.”
Klappich notes that another trend in warehouse automation is emerging: robotics as a service. Given that many etailers have a cyclical business pattern, this model enables them to scale their use of robots up and down according to fluctuations in demand.
“For most of the year I have, say, 50 robots – and that’s good enough; it gets the work done,” he says. “But for the Christmas rush I could scale that up to 500. The ability to do this as a service, instead of incurring a huge capital expense, is affordable and gives a rapid payback. That’s pretty compelling.”
There’s broad agreement among industry experts that, even when the pandemic is a distant memory, labour shortages will continue to fuel the trend towards hi-tech automation in warehouses and fulfilment centres.
In fact, Klappich says, “the one challenge that retailers face is that they have too many options to choose from in this area, not too few”.
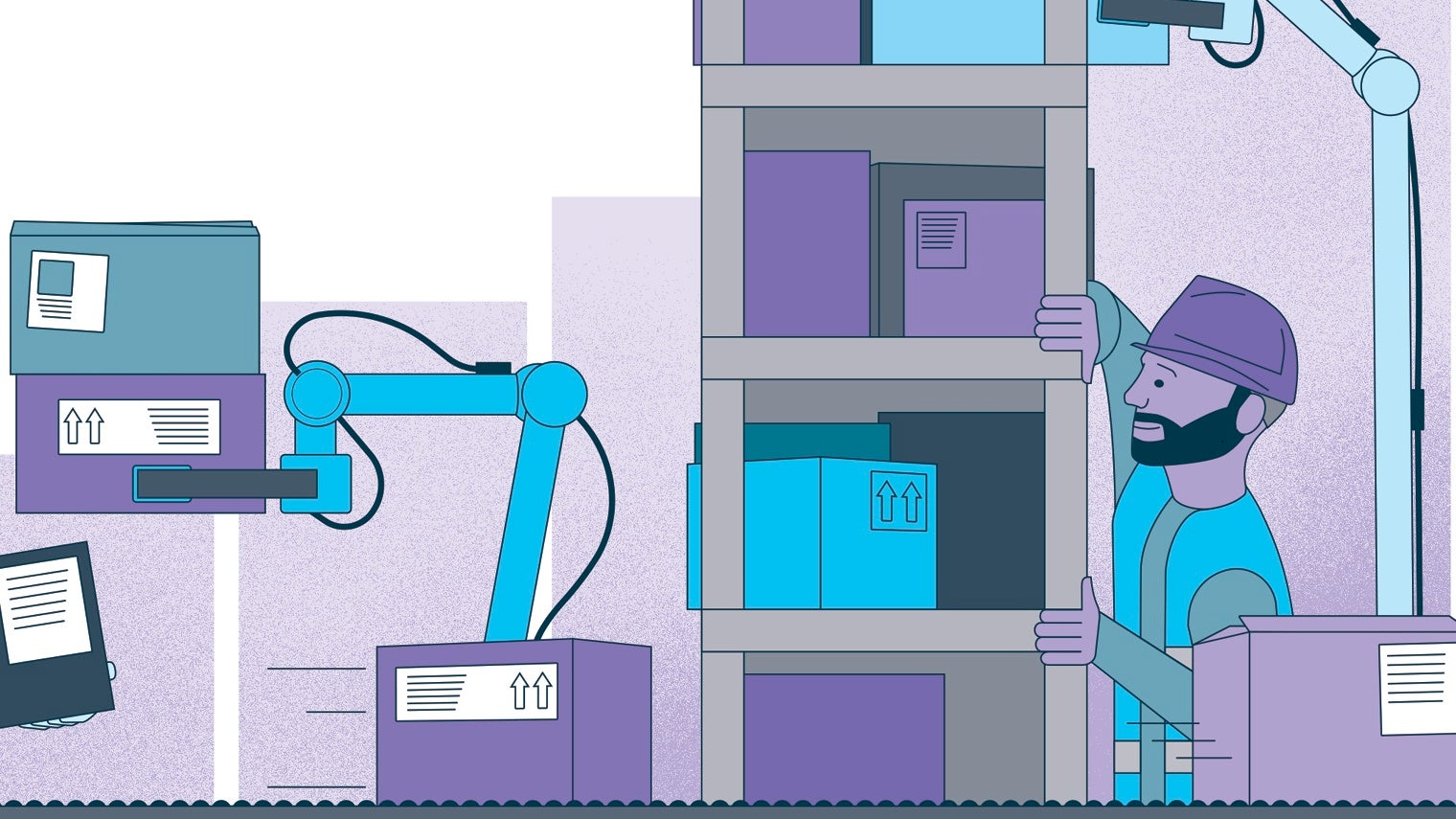
The nation’s shift towards online shopping at the start of the Covid crisis “accelerated five years of change into just five weeks. It has created demand for stock that is set to last long after the pandemic.”
That’s the prediction of Dave Ashwell, who, as managing director of AO Logistics, knows what he’s talking about. Online electricals retailer AO has acquired more than 45,000m2 of warehousing space across Cheshire and Staffordshire in recent months, in line with many other etailers that are investing in hi-tech facilities in their effort to keep the supply of goods up with demand.
AO Logistics’ new warehouse in Stoke-on-Trent features voice-picking technology, which ensures that “the right goods are loaded in the correct sequence, improving speed and accuracy”, Ashwell says. “Our people wear headsets, meaning that they no longer need to carry around a pen and paper. This leaves them with both hands free to lift items safely. We hope that it will significantly reduce the amount of paper we use here too.”