The marine industry faces considerable challenges as vessels spend most of their time at sea and, when in port, commercial pressures demand a fast turnaround with minimum downtime.
The problem is compounded by the existence of data silos and resistance to change, as Tim Schweikert, president and chief executive of GE’s Marine Solutions, explains.
He says: “Traditional methods of managing data have created data silos and islands of automation, making it difficult to optimise operations across a vessel or systemise across the fleet. Moreover, as marine operators are traditionally expertise dependent in their operations, they are often resistant to embracing the changes that come with digital transformation and servitisation.”
Digital adoption
The pressures of market oversupply, low oil revenues for the offshore marine industry, rising costs and increasing environmental regulations have conspired to force the industry to embrace digital technologies, such as cloud, artificial intelligence (AI) and internet of things (IoT), that create opportunities for transformation through disruptive innovation, servitisation and smarter use of data.
“In the marine industry, data is most commonly used for post-incident analysis, offering retrospective insights and solutions to problems once they have occurred, leading to significant dry dock costs and loss of revenues,” says Mr Schweikert. “Today, investors no longer have the patience to wait several years for their money to deliver dividends, but expect to see returns much faster.”
Through real-time analysis of data, potential problems can be predicted before they arise, enabling operators to shift from prescriptive to predictive maintenance, ultimately reducing the amount of maintenance required.
This will also create greater operational efficiencies for shipping operators. UK-based software company QiO has helped shipping operators to overcome the challenges created by the retrofitting of sensors that produce masses of data that are manually retrieved and only assessed when the journey is complete.
QiO’s mobile responsive web application deployed in a secure cloud environment creates a system that can not only detect anomalies, but also relate them to historic, current and predictive insights for a single ship or across the entire fleet, based on real-time sensor data. The outcome is improved fuel efficiency and hundreds of thousands of dollars in annual cost-savings per vessel.
Long-term asset management and maintenance are a priority for maritime manufacturers and operators, since downtime directly affects overall results, so the IoT can facilitate servitisation in this area.
Servitisation will present maritime operators new opportunities to sustain competitive advantage, with manufacturers able to offer evermore impressive service level agreements
Songa Offshore is an international mid-water drilling contractor with a strong presence in the North Atlantic basin, operating a fleet of seven semi-submersible rigs. To monitor asset performance, the company has connected IoT sensors to 600 assets on each of four of its rigs that will capture usage metrics.
To improve maintenance effectiveness and operationalise IoT data, the company has implemented the IFS IoT Business Connector, which enables it to capture asset condition readings that form the basis of planning and optimising maintenance work. This also forms a vital part of their strategy for documenting a rig’s condition.
Antony Bourne, global manufacturing industry director at IFS, says: “With the increased level of automation, Songa Offshore’s objective is to reduce the time needed for yard stays for the rigs, which means significant cost-savings, and at the same time dramatically shorten the unplanned downtime of each rig, due to better control of the equipment’s condition. The result is enhanced asset reliability, longer times between service intervals, longer asset lifespans and cost-savings.”
Through the use of digital technology, servitisation will present maritime operators new opportunities to sustain competitive advantage, with manufacturers able to offer uptime guarantees in the form of evermore impressive service level agreements. By utilising big data and the IoT, AI can analyse trends to develop the best service plan for maritime assets, says Marne Martin, chief executive of ServicePower.
She says: “For example, to manage engine maintenance, AI-backed software can recognise previous service events and suggest an appropriate plan, while locating the best resources for the job. It can then send a message to the appropriate engineer to co-ordinate the job’s next steps. This saves time on creating the service plan, contacts the most qualified available technician and provides instant insights to ensure project success.
“AI will also help manufacturers combine thousands of variables, like ship size, asset performance, cargo, even the weather, to over time continually improve performance. This means assets will sweat harder to considerably improve the reliability, timeliness and even green credentials of maritime organisations.”
The marine industry is at the start of its digital journey into servitisation, but as technology solutions continue to evolve, the future for maritime manufacturing looks bright.
Mr Schweikert concludes: “Building digital capability and eliminating silos can help ship owners and operators to derisk decisions, bringing practical, actionable insights into vessel and fleet performance. It also opens up opportunities for industry collaboration and brings a focus on changing processes, not just products.”
Digital adoption
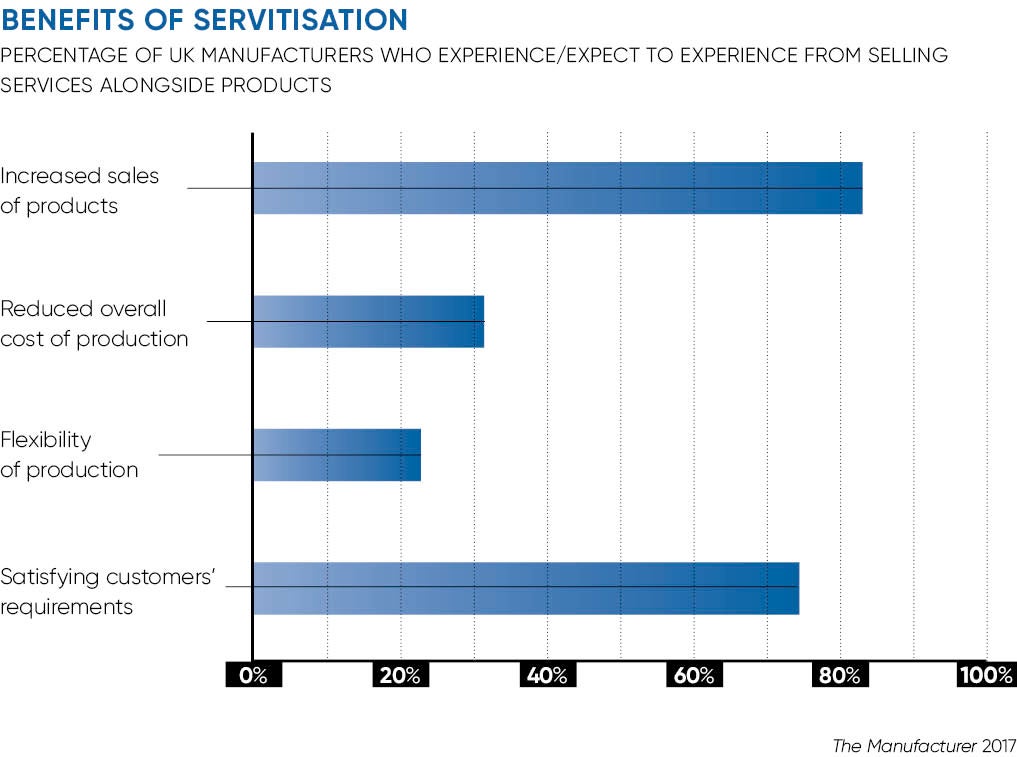
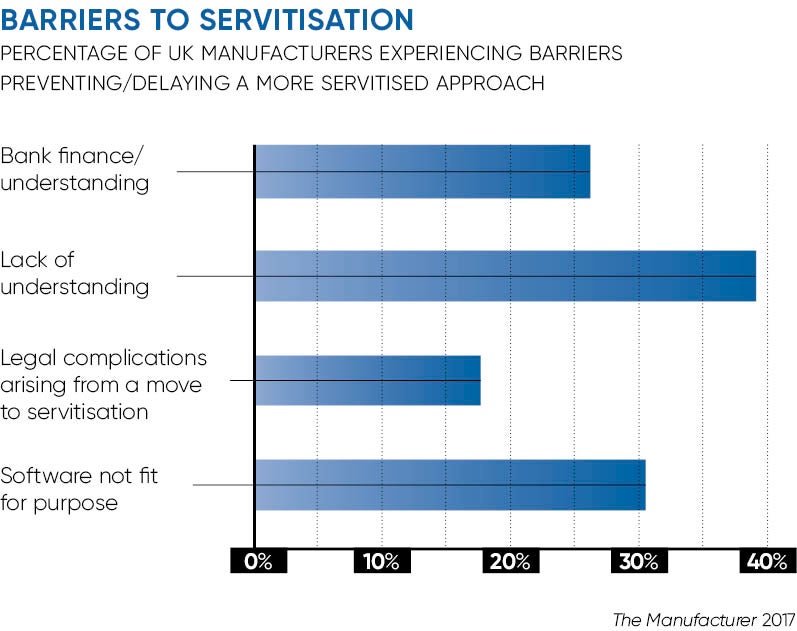