From Virgin Atlantic outfitting a fleet of Boeing 787 aircrafts with internet of things (IoT) devices to resolve mechanical problems before they cause havoc, to IoT sensors in cows collars helping dairy farmers monitor their herd’s health, applications are virtually endless.
Innovative IoT solutions are on course to shake up product lifecycle management (PLM) for the better as it becomes increasingly important for companies to monitor products throughout their whole life cycle.
“IoT enables harmonisation of physical and digital life cycles spanning the entire digital thread from PLM design team, to manufacturing, to transportation and logistics, and to customer usage, powering the modern supply chain of the future,” says Atul Mahamuni, vice president of IoT at Oracle.
Most manufacturers currently only receive a limited amount of feedback on product use and performance from consumers, mainly through returns and complaints. However, this falls far short of the real-time responses IoT-enabled devices can provide. With the advent of IoT, Mr Mahamuni explains, manufacturers are now able to gain a level of insight into product design, ordering, fulfilment and transportation that was never before possible.
The benefits
There are clear business benefits for manufacturers who embrace IoT in PLM, namely predictive maintenance and more intelligent inventory management. “IoT performance data helps them use predictive insights to minimise maintenance costs, driving greater profitability and lower costs to the consumer for the capability. The consumer benefits as well by eliminating maintenance costs and headaches,” says Steve Shoaf, go-to-market manager, continuous engineering in IoT, at IBM Watson IoT.
Predictive models utilise advanced artificial intelligence technologies that allow manufacturers to respond rapidly to product problems, often before customers themselves know there is an issue. These consumers can be expected to benefit from the quick resolution of errors and will in turn be more satisfied with the product experience. The continuous stream of data from connected devices makes it easier for manufacturers to gather relevant consumer insights and then feed this information back into the production loop.
But perhaps more importantly, new revenue streams can be created by the effective implementation of IoT solutions in PLM. “IoT devices are becoming channels. Impactful and transformational business value can be achieved through end-to-end digitisation of value streams connecting the consumer or user of the IoT device to the manufacturer. Just as a mobile device or browser handles customer service, IoT devices can be used to promote products, services, cross-sell or upsell,” says Dr Setrag Khoshafian, chief evangelist and vice president of business process management technology at software company Pega.
Rather than just selling a traditional product, innovative manufacturers at the forefront of IoT adoption are exploring offering their customers a product-as-a-service. By utilising data insights, PLM managers can move away from the evaluation of internal data and processes, according to Mr Mahamuni. “Instead, continuous availability of current data and frequent changes to the products can be suggested, evaluated and executed, giving rise to rapid innovation cycles that can meet and exceed the expectations of external customers,” he says.
Modern business models are being developed to monetise the shift from a simple product to continuous service and are also creating closer relationships between manufacturers and customers in the process. While opportunities are created by this change, manufacturers will now be expected to ensure good product performance for the entire life cycle.
IoT-connected devices create vast quantities of highly valuable data every day with many manufacturers finding it difficult to sift through the mountains of data to uncover actionable insights. By applying analytics to this data, the loop can be closed in PLM and explicit information about how the product is operated by consumers will become available.
Customer usage is only one part of the PLM puzzle. IoT sensors can gather data on the environment the product is used in, including external temperature and the levels of humidity, to gain further detail on consumer behaviour.
Jan Höller, principal researcher at Ericsson Research, says the data can be used to analyse the actual design of the product in terms of performance. “This can be used to understand energy consumption patterns and to identify flaws in design or material choice by analysing wear and tear,” he says.
“These different types of online insights can then be used at different points in the product life-cycle process, from the design throughout the production process. Integration of data and applying analytics and machine-learning on data with products in the field to extract and use the insights requires a cloud-based IoT solution that is properly integrated into the PLM process itself. In addition, data and information interoperability across systems is another key feature to make this happen.”
The conventional focus of PLM has been on the design life cycle, but IoT sensors embedded in goods are allowing manufactures to expand their attention to after the product is launched. Even existing products can be retrofitted with sensors after they hit the marketplace, leaving no device out of the IoT environment.
“With change and configuration support associated with the digital thread, IoT, supported by sensor data derived from operational performance, closes a loop between actual product performance and predicted performance associated with the design activity,” says Mr Shoaf. “Deriving insight from operational performance data, engineers can construct new requirements and basically loop back through the entire life cycle, resulting in continuous improvement.”
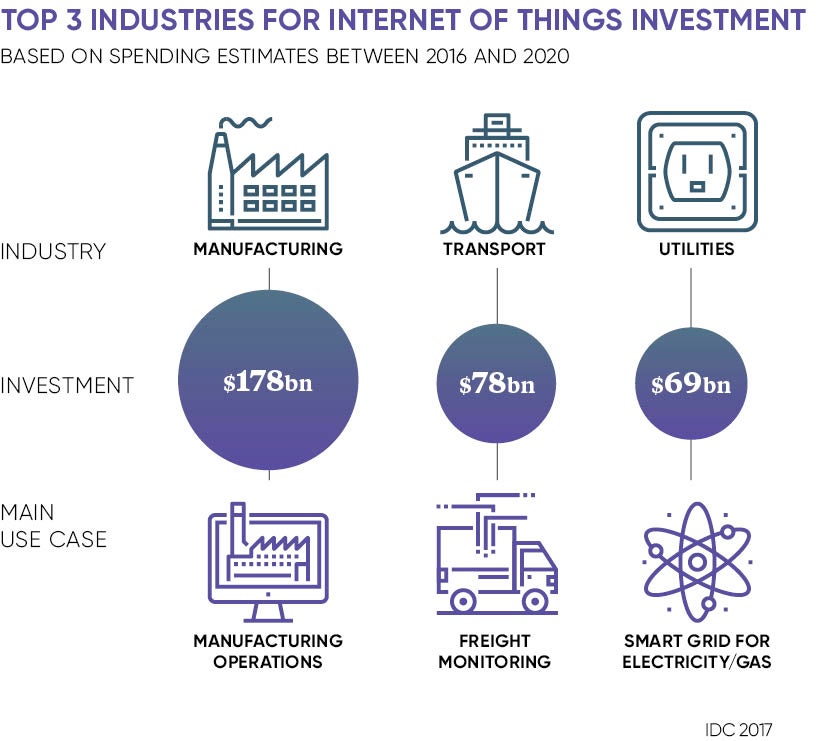
The benefits
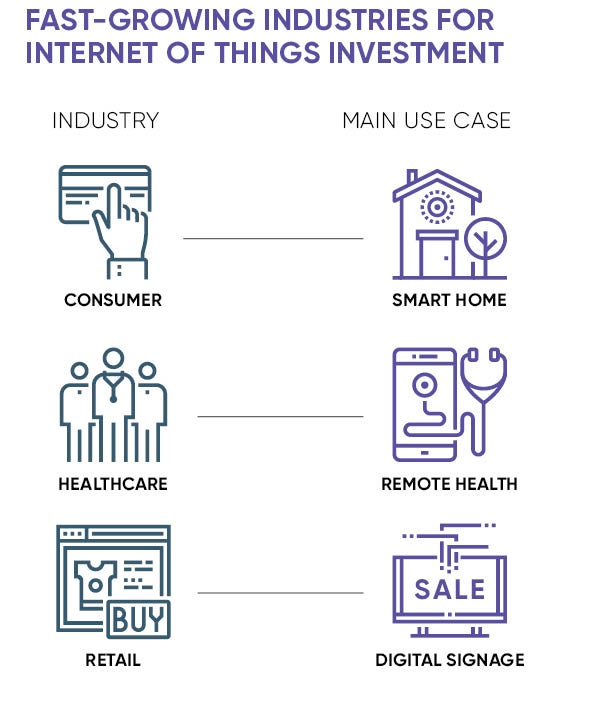