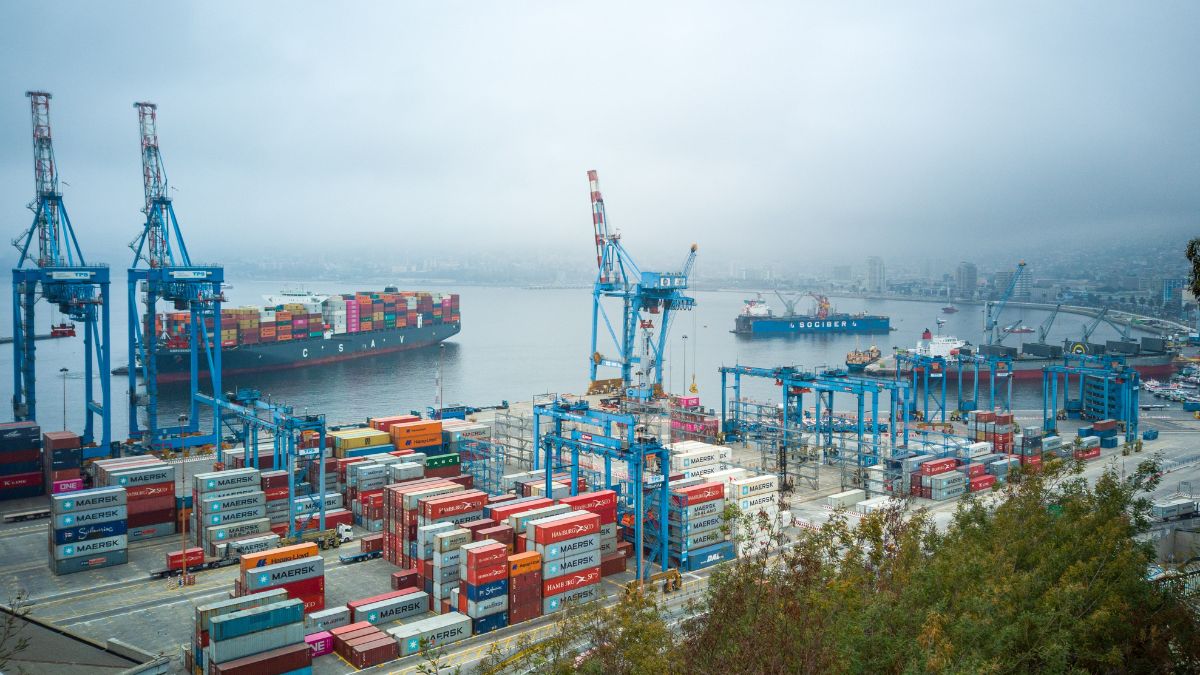
One of the first emails Rachel Watkyn opened in 2022 was from an overseas supplier, advising her that prices were being increased by 40% – with immediate effect.
Over the last 18 months, Watkyn’s packaging business, Tiny Box Company, has seen a massive increase in supply chain costs. The cost of a single shipment of boxes from East Asia has increased from £2,500 to £18,000, while the cost of sourcing raw materials in the UK has risen by more than a quarter.
“Supply chain costs used to account for 10% of our costs but that’s increased to 40%. It’s a huge challenge and it’s not possible for us to pass on all those costs to customers while remaining competitive,” says Watkyn.
Packaging is just one industry sector that’s facing huge supply chain issues in 2022, says Simon Geale, executive vice-president at supply chain consultancy Proxima. “Every company with a supply chain is grappling with supply chain cost management,” he says.
Here, we round up six industries facing supply chain challenges in 2022 and examine how they are building resilience to mitigate the impact of future disruption.
Automotive
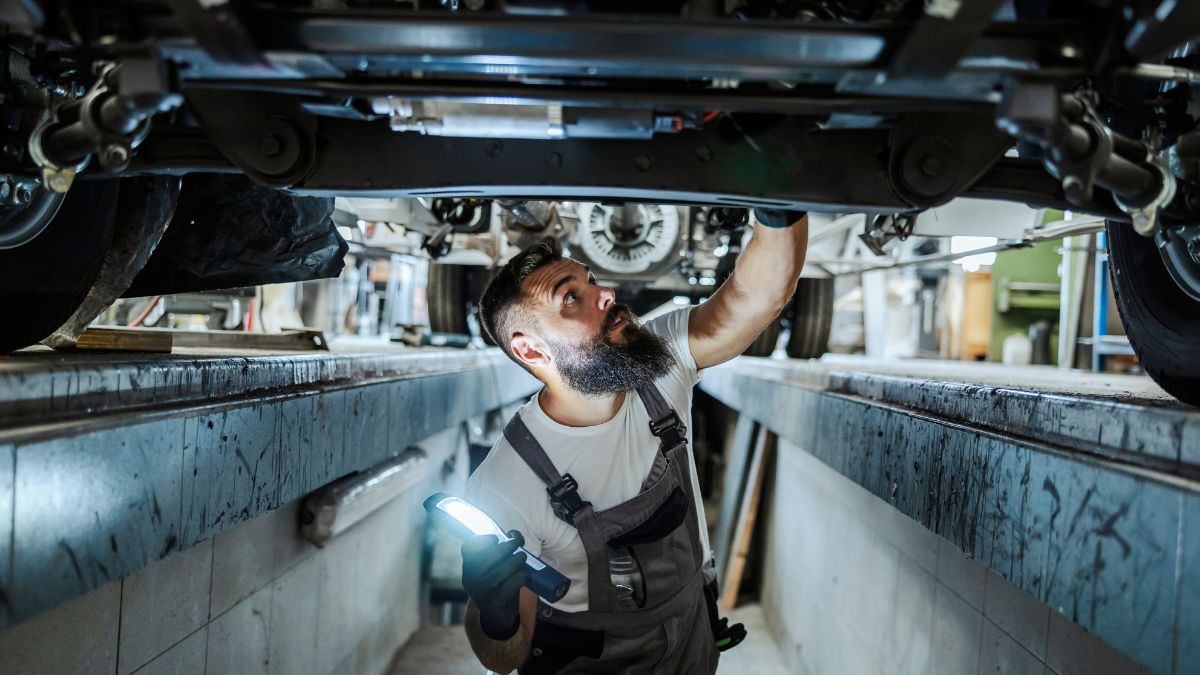
The automotive sector has experienced supply chain disruption due to a combination of the pandemic, the drought in Southwest China, the war in Ukraine and a shortage of chips. “The automotive sector illustrates how hard it is to manage risk in supply chains, because you’re dealing with so many different factors, from materials to weather to political events,” says Geale.
Companies like Volkswagen have invested heavily in new partnerships that reshaped its global supply chain, sourcing new suppliers for important components such as nickel and batteries, while adopting a nearshoring strategy for some manufacturing. “Even though the company sold 2 million cars less than expected, they still made a strong profit last year, which shows how important their supply chain strategy is to the company’s health,” Geale adds.
Fashion
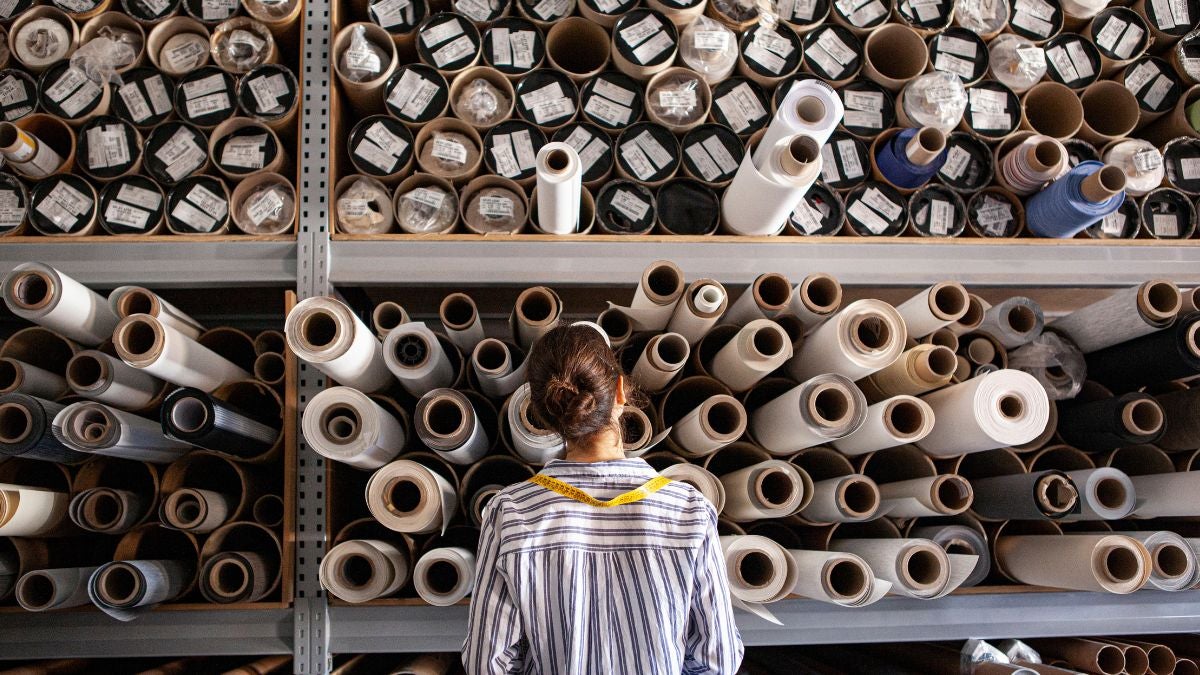
The world of fast fashion got a lot slower in the last three years. Garment companies in Asia have been hit by a series of lockdown orders, while global freight shipping costs have rocketed due to pent-up demand after the pandemic. Global water shortages have also impacted the water-intensive process of making new clothes.
Further disruption is on the horizon with new EU legislation that could hold supply chain managers responsible for abuses of workers’ rights and poor working conditions in overseas factories. “All of these things increase the cost of production and increase the time taken to get new clothing to market, so the fashion industry needs to find ways to reduce costs in other parts of the supply chain,” says Professor Richard Wilding, a former professor of supply chain risk at Cranfield School of Management.
One of the biggest moves to build resilience into fashion supply chains can be seen in the rise of nearshoring and what’s known as late configuration, says Wilding. Companies like Benetton will create a skirt in Asia and ship it to Europe, where it is dyed and customised locally. This allows the manufacturer to benefit from lower material and manufacturing costs in Asia, but also respond quickly to local demand in different regions.
“Maybe you have a skirt that could be red or green, but suddenly the Duchess of Cambridge wears a green skirt, and demand for green skirts goes through the roof. With late configuration, you can get those green skirts to market in a week or two, rather than waiting eight or 10 weeks for them to get to Europe on freight ships,” says Wilding.
Retail
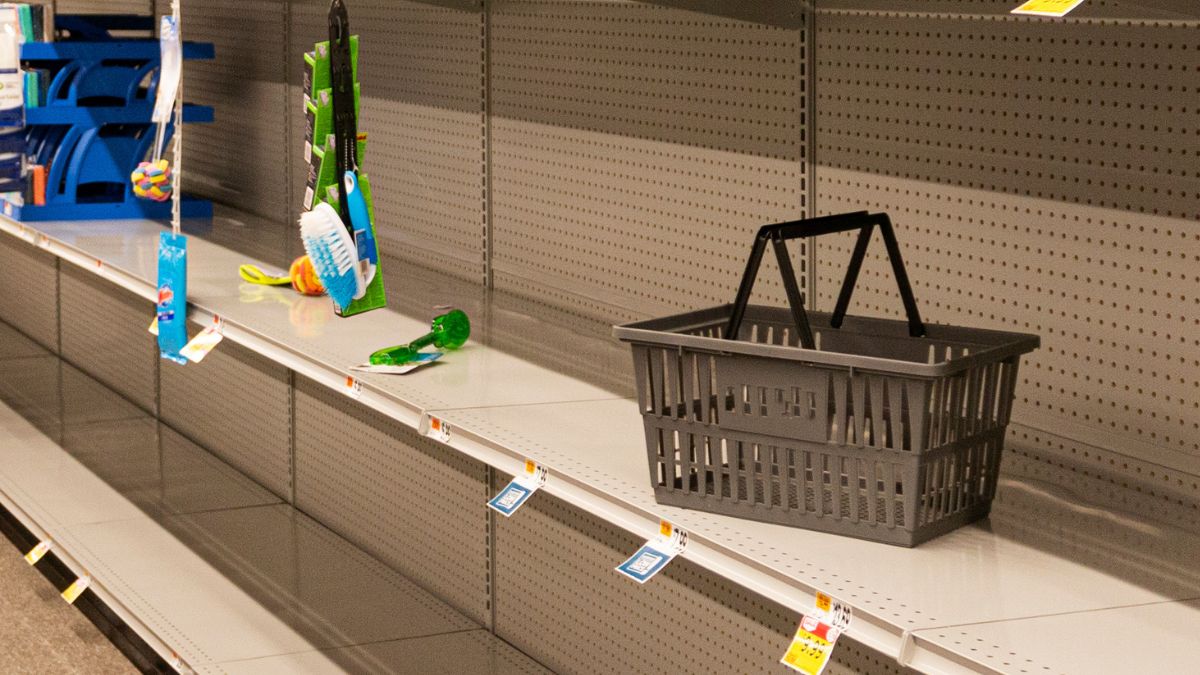
The retail industry was hit by supply chain delays throughout 2020 and 2021. These were caused by problems with sourcing materials and logistics challenges getting products from manufacturing sites in East Asia to customers in Europe.
With peak trading season just around the corner, the sector has already taken steps to reduce the risk of shortages this Christmas. “What we’ve seen is the retail sector shorten planning cycles dramatically and look to build much more agile supply chains,” says Geale. “Many retailers of smaller items in sectors like home goods or toys moved their buying cycles earlier and are building up inventory to minimise the risk of shortages during that peak trading period. It isn’t unusual to see retailers that have tripled their warehouse space in the last year.”
The flip side of this approach is that many retailers have huge amounts of working capital tied up in inventory; if there is a slowdown in consumer spending at Christmas, Geale says we will likely see steep discounting as retailers look to clear that stock in 2023.
Agriculture
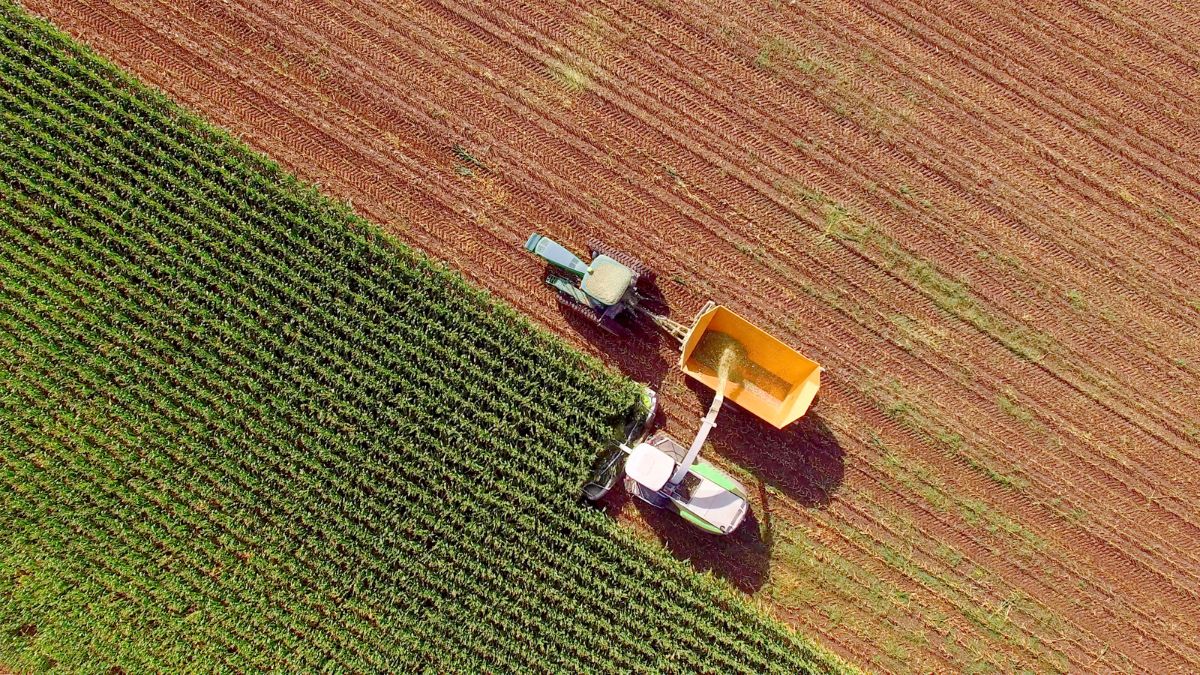
The global agriculture sector is facing unprecedented pressure from climate change, geopolitical instability, and the after-effects of the pandemic. Any one of these challenges has serious implications for agriculture, says Simon Davis, agricultural practice lead with sustainability consultancy Anthesis. “We’re in uncharted territory,” says Davis. “Because it’s such a just-in-time industry, it’s very easy to tip into food insecurity when supply chains fail.”
The latest challenge to farmers has been a rapid rise in energy costs. This has had a knock-on effect on the price of fertiliser, which rose by 80% in 2021 and by a further 30% in 2022. Add to that a global heatwave leading to water shortages for crops and livestock and it’s a perfect storm.
In response, the farming industry is likely to see consolidation as smaller farmers exit the sector. Those that remain may adapt the crops they grow, says Davis, focusing on increasing the number of hardy crops grown, increasing yields during hotter, drier seasons. “In the mid-term, I expect to see farmers adopting more regenerative practices that improve soil quality and yields, alongside crop diversification, with innovation funded in part by retailers who want to secure their own supplies,” Davis says.
Food
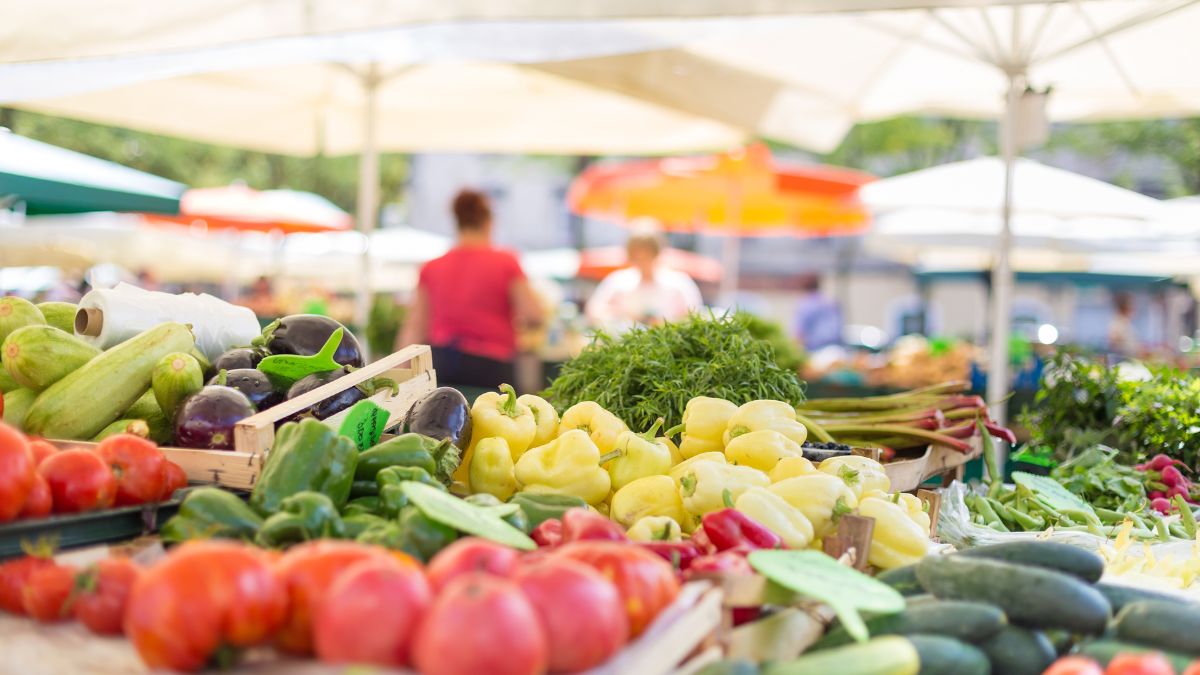
The food industry has been hit by all the challenges that have affected farming and agriculture. As a result, many food businesses are starting to see stress on their supplies, which could easily get worse, says Geale.
“We have just seen a drought in China just before harvest season starts, in a country that relies heavily on hydro-electric power,” he notes. “The result could be that there is less food available to export from China, but also that China will need to import food that previously would have been bought by other countries in Europe or Africa.”
The first impact is likely to be product rationalisation, where food manufacturers reduce the number of product lines available to cut manufacturing costs. Geale also expects to see food companies paying more to secure supplies or switching to nearshore or onshore alternatives, which may cost more.
To offset these price increases, Geale says the food industry is already investing heavily in innovation and structural changes to reduce supply chain and operating costs. “I think they are going to have to be pretty bold, and we’ll see big structural changes, increased automation and smarter supply chains as they struggle to maintain what are already quite fine margins.”
Airlines
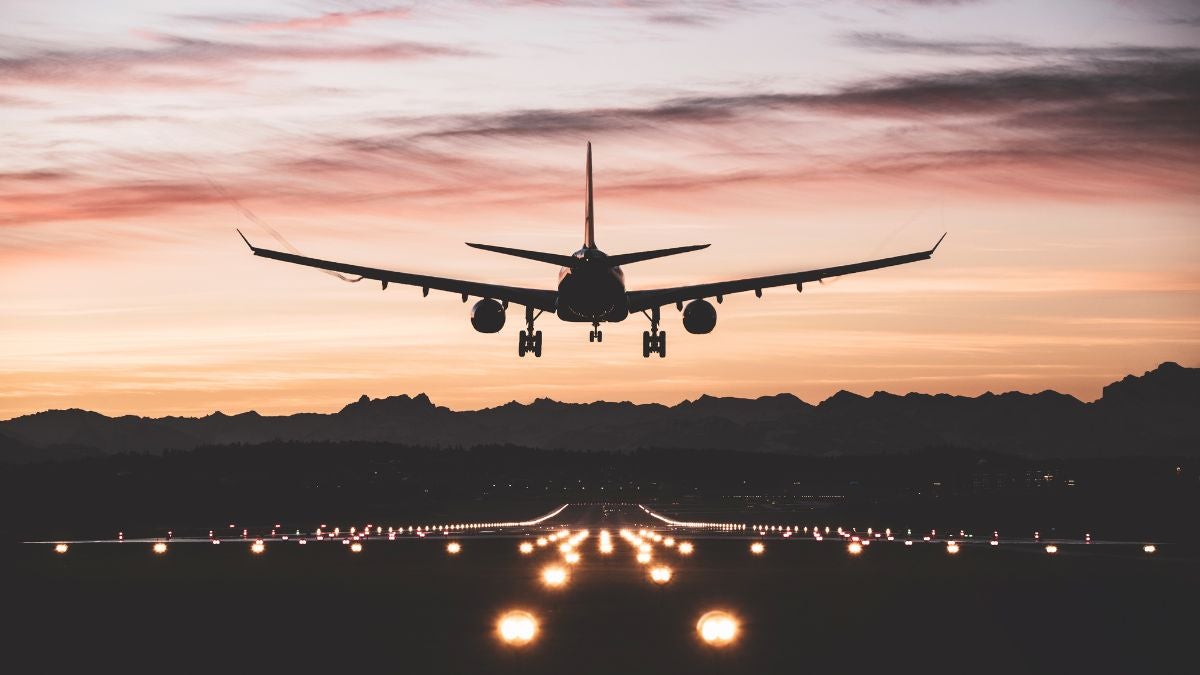
This summer, budget airline Ryanair flew 15% more passengers than it did in the summer of 2019. Few in the airline industry expected demand for air travel to bounce back so quickly after the pandemic.
The most visible challenge for the airline industry has been a staff shortage. Staff who were furloughed during the pandemic haven’t returned to their jobs, especially where many are facing less attractive working conditions imposed by airlines looking to recoup costs.
A less visible issue is a huge shortage of materials and spare parts to build new planes and keep existing planes running. When the pandemic hit and the airline industry shut down, a lot of the sites that produced fiberglass and carbon fibre for planes simply ceased operations. “The furnaces all closed down, and airlines were storing new planes in the desert because they didn’t know what to do with them,” Wilding says. “When demand for all those materials bounced back, the furnaces had been destroyed and needed to be completely rebuilt. That’s going to take some time.”
Building resilience into airlines will need a shift in supply chain strategy. Wilding expects to see a move towards “buying for resilience” over “buying for cost”. There will be a “massive increase in scenario planning, because the airlines that had done better scenario planning were much better able to respond to the last two years than those that focused on ‘respond and recover’ as a strategy”, he says.
At Tiny Box Co, Watkyn is building resilience into her own supply chain in various ways. Tiny Box Co is currently negotiating to create a joint venture manufacturing site in Europe. The firm has also moved 20% of its production to a previously disused factory in Cornwall, which has offset the increased price of sourcing materials overseas.
“We’re really focusing on building more efficiency and investing in technology to drive internal efficiency,” says Watkyn. “There’s only so much cost we can pass on to our customers, so we have to think smarter when it comes to supply chain strategy.”
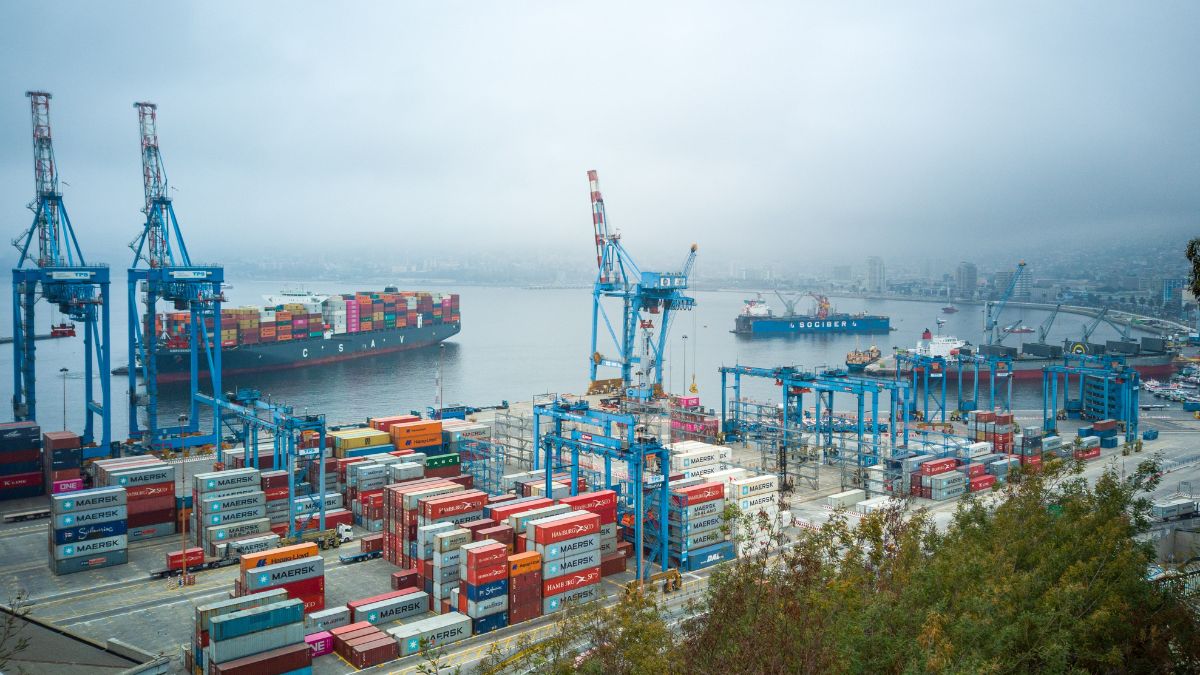
One of the first emails Rachel Watkyn opened in 2022 was from an overseas supplier, advising her that prices were being increased by 40% - with immediate effect.
Over the last 18 months, Watkyn’s packaging business, Tiny Box Company, has seen a massive increase in supply chain costs. The cost of a single shipment of boxes from East Asia has increased from £2,500 to £18,000, while the cost of sourcing raw materials in the UK has risen by more than a quarter.
“Supply chain costs used to account for 10% of our costs but that’s increased to 40%. It’s a huge challenge and it’s not possible for us to pass on all those costs to customers while remaining competitive,” says Watkyn.