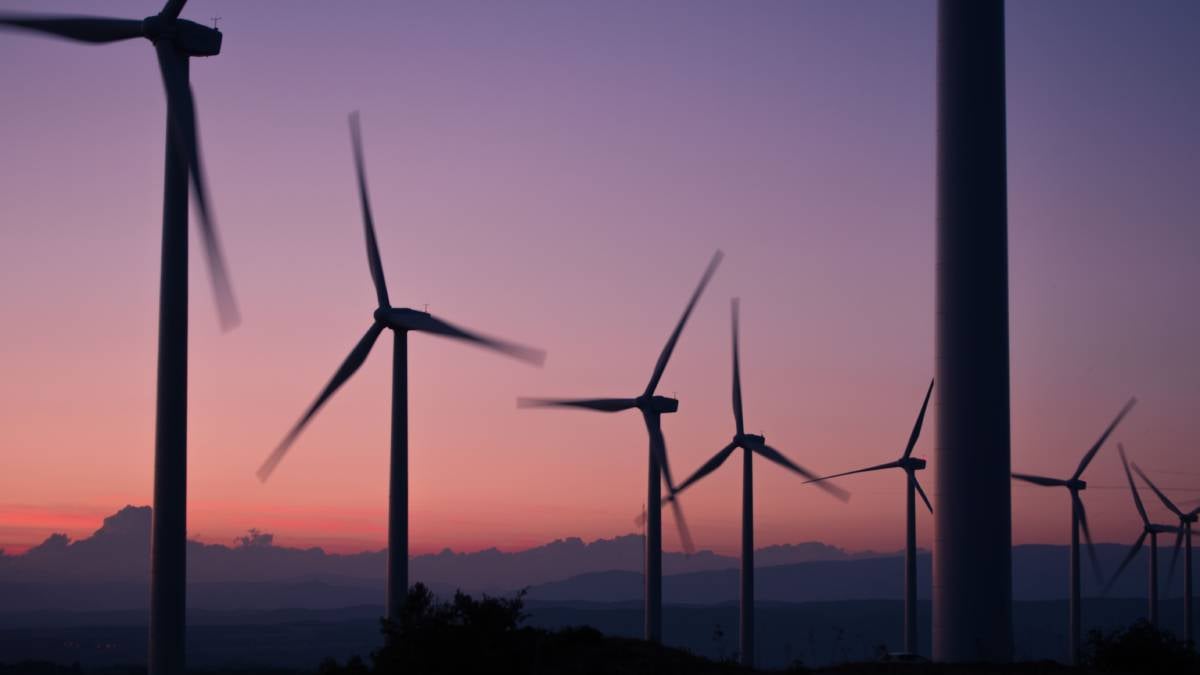
Whether you consider wind turbines to be majestic structures or a blight, there is no denying that they’re an efficient way of producing energy. But what’s not so efficient is there’s a knowledge gap between their design and the operations and maintenance (O&M) stage.
The average wind turbine requires maintenance check-ups two to three times a year and its lifespan is about 20 years or more, depending on environmental factors.
Inspecting and maintaining wind turbines can be extremely difficult, especially if they’re offshore or in remote locations, where engineers can face wind and visibility issues.
In addition, scheduled maintenance can often lead to potential defects being overlooked, which then leads to further unscheduled and reactive maintenance. A study by academics in the UK and Germany has suggested 25% of wind turbine faults can be responsible for up to 95% of downtime.
Digital twins have the potential to change offshore wind management and bridge the disconnect between the design and O&M stages.
As they emerge from the pandemic, companies should be considering using digital twins to better prepare for unexpected shocks and to build an intelligent and resilient ecosystem
By creating a digital representation of a physical asset, engineering teams can monitor the operational performance and health of the asset through real-time data collated by a network of sensors. Using machine learning, the digital twin continuously updates to reflect the real-time working condition of the asset.
Engineers can be alerted to potential defects and carry out maintenance before a fault occurs. This preventive approach to maintenance can lower costs and reduce downtime.
The insight gleaned through the data can also give operators a better understanding of how a wind turbine is performing and is expected to perform over the rest of its life cycle.
This information can then be fed back to manufacturers who can then tweak designs, using generative design software to optimise the lifespan of future wind turbines. This, in turn, can result in a superior product as it takes the drudgery out of the design process and enables manufacturers to focus on delivering the best possible outcome.
An example of digital twins in action is GE’s digital wind farm. Cloud-based models monitor and optimise the performance of turbines as they continue to run and generate energy. GE has demonstrated the technology can help to increase production by around 20% and create an additional $100m in revenue over a turbine’s life cycle.
It’s a growing digital twins market
Digital twins aren’t a new kid on the IoT block. As with any technology with a fancy name, there has been a buzz around it for a number of years. Broadly speaking, though, the true potential and application of digital twins is yet to be fully realised.
According to analysts at Research and Markets, the digital twin market will grow at a compound annual growth rate (CAGR) of 41.7% between 2021 and 2027, by which time it will be valued at $63.5bn. Adoption of digital twins will only gather pace as more companies and industries embrace Industry 4.0 technologies, the research notes.
While predictive maintenance and performance monitoring applications are expected to dominate the market, business optimisation applications are forecast to see a CAGR of 42.2% through 2027. Inventory management applications are expected to grow at a rate of 42.7%.
Adoption of digital twins is being accelerated by the Covid crisis, with IoT technology being used to model the post-pandemic recovery. Digital twins can help manufacturers to easily identify potential defects with designs that could cause supply chain bottlenecks further downstream.
“As they emerge from the pandemic, companies should be considering using digital twins to better prepare for unexpected shocks and to build an intelligent and resilient ecosystem,” says Andrew Duncan, partner and UK country head at Infosys. The global IT consultancy teamed up with GE in 2015 to develop the world’s first digital twin for aircraft landing gear.
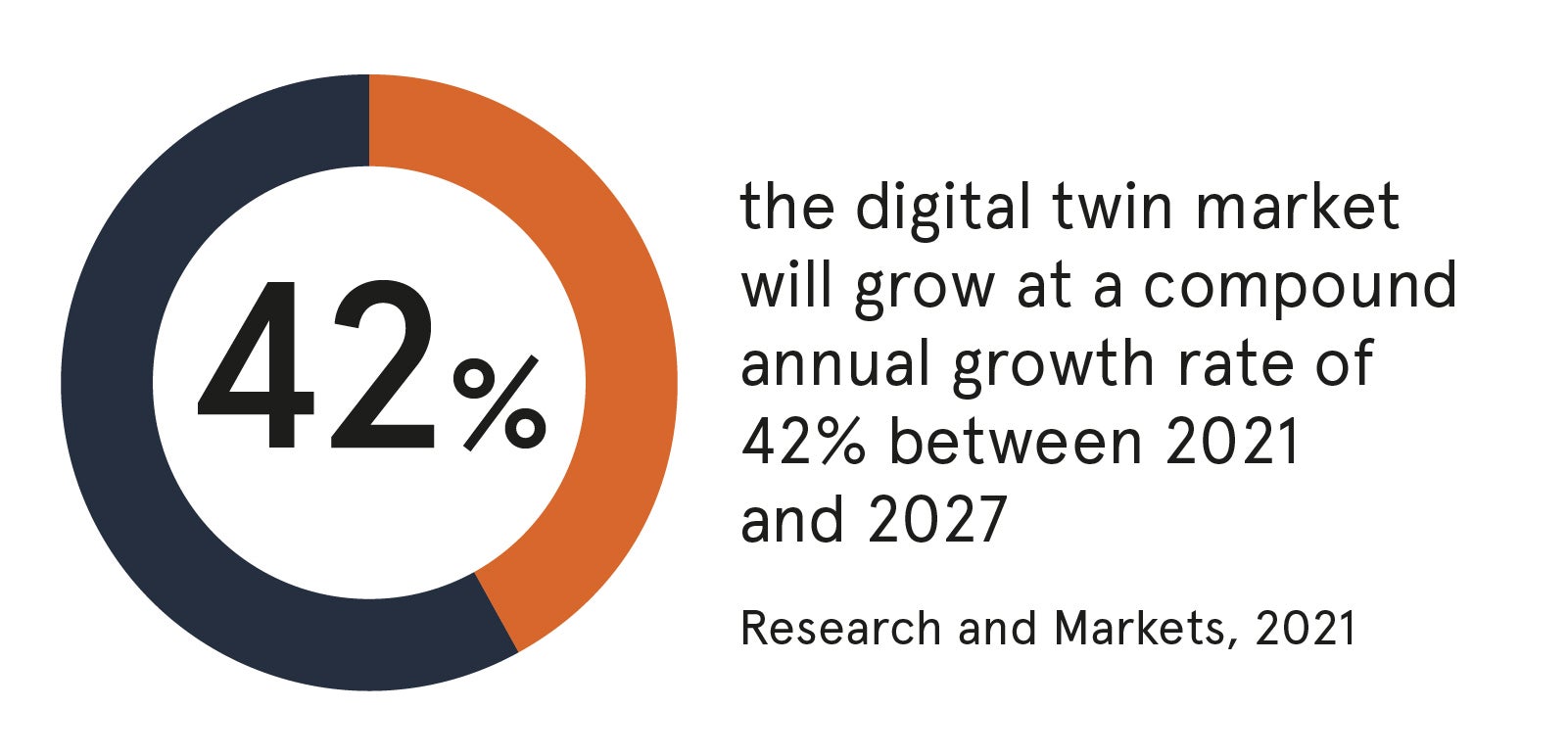
Many smaller companies still rely on legacy systems and outdated applications, while there’s a mountain of technical debt that needs to be culled, he says.
If manufacturers want to compete in an increasingly complex and digital world, Duncan adds, “it’s more important than ever that they review and upgrade legacy core systems to support the agility and innovation which fuel digital transformation”.
Better connectivity leads to better designs
Failing to modernise legacy systems and embrace Industry 4.0 can be problematic. Even if a manufacturer is using digital twins and generative design software to optimise production, a supply chain can be brought to a screeching halt by a single stakeholder not leveraging data.
Although some manufacturers may be resistant to new technologies, IDC isn’t expecting this to be too much of an issue. Seven in 10 respondents surveyed by the global market intelligence firm have identified digital twins as an important strategic initiative going forward.
What’s more, IDC research has forecast that 65% of global manufacturers will see savings of 10% in operational expenses by 2023. And as digital twins continue to advance, thanks to IoT and machine learning, manufacturers will only get more value out of the technology.
Emerging technologies, such as edge computing and 5G wireless connectivity, will further enhance the capabilities of digital twins, enabling even faster decision-making.
That said, the more IoT devices there are in manufacturing operations, the more opportunities there will be for cybercriminals and hackers to exploit. For this reason, it’s important that manufacturers have robust cybersecurity strategies in place.
“Security teams need to collaborate with C-suite leaders to ensure cybersecurity decisions support the company’s strategic goals,” says Duncan. “It’s absolutely vital for good security practices to be baked into business strategies.”
As long as digital twins are deployed in a secure and safe way, the technology has the power to transform manufacturing quality.
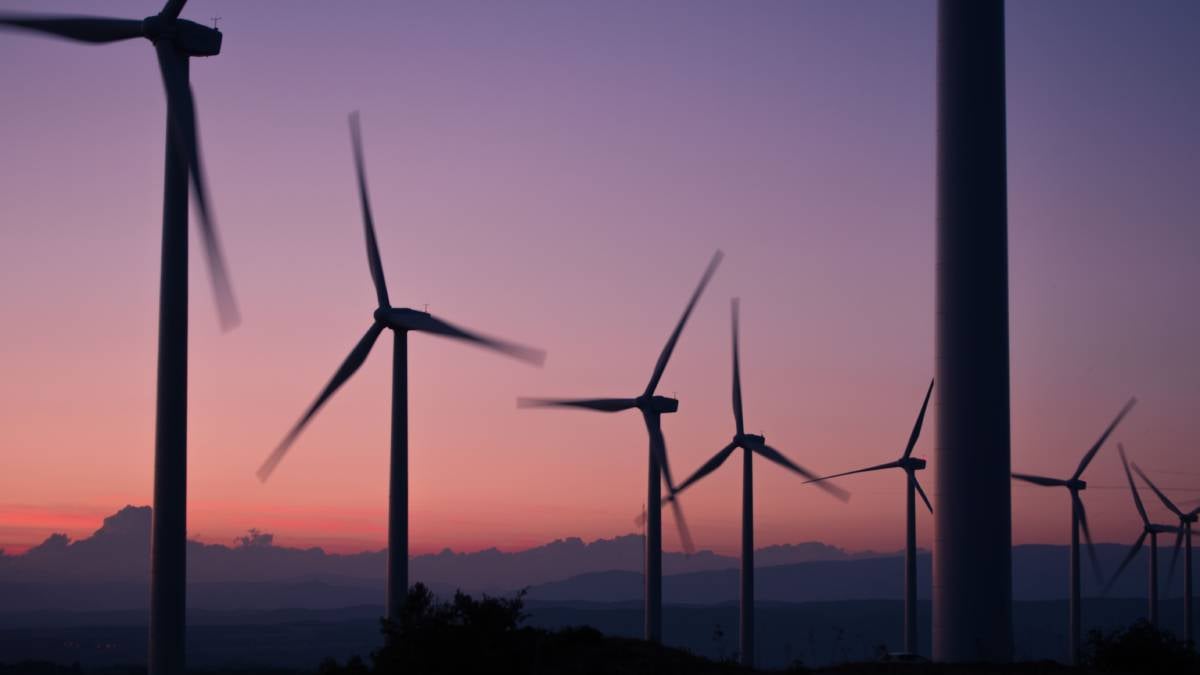
Whether you consider wind turbines to be majestic structures or a blight, there is no denying that they’re an efficient way of producing energy. But what’s not so efficient is there’s a knowledge gap between their design and the operations and maintenance (O&M) stage.
The average wind turbine requires maintenance check-ups two to three times a year and its lifespan is about 20 years or more, depending on environmental factors.
Inspecting and maintaining wind turbines can be extremely difficult, especially if they’re offshore or in remote locations, where engineers can face wind and visibility issues.