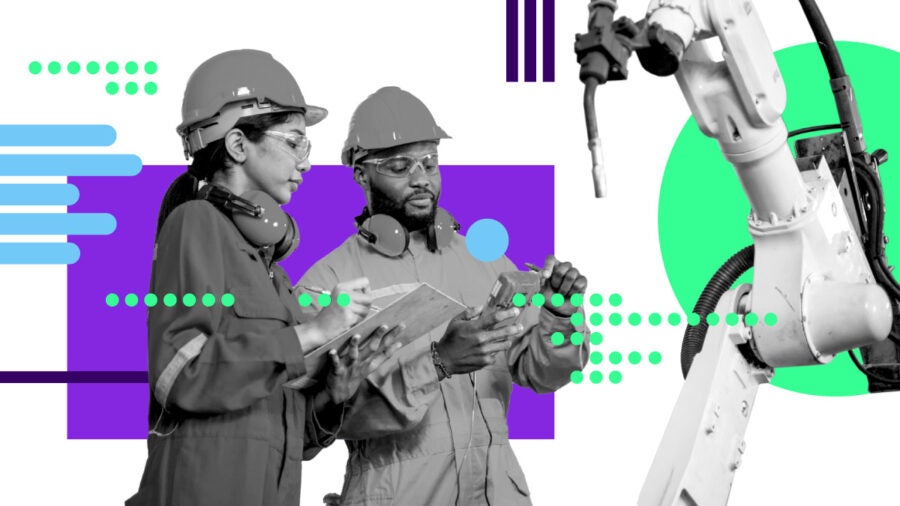
In many ways there has never been a more uncertain time to be a global manufacturer. While there are still huge opportunities out there for the taking, long-standing problems such as economic volatility, talent shortages and supply chain risks continue to put pressure on firms.
Moreover, new and more complex business challenges have come to the fore, including a fast-evolving regulatory landscape, the increased risk of cyberattacks and the disruption caused by rapid technological change.
This requires new strategies if manufacturing leaders are to thrive in a changing world and, in turn, many are turning to innovation and embracing smart manufacturing technologies to improve their competitive positioning.
Advancements in robotics, artificial intelligence (AI) and the internet of things (IoT) have the potential to revolutionise manufacturing processes while enabling companies to become more agile, resilient and efficient. Similarly, firms can better model opportunities and risks thanks to the powerful insights yielded through big data.
But while the manufacturing industry is well aware of the benefits of these innovations, it remains a relative laggard when it comes to digital adoption and many firms risk falling behind braver peers.
So how can global manufacturers overcome their “digital inertia” and harness the seismic opportunities offered by digital transformation?
Leaders versus laggards
In July, the global enterprise software provider, IFS, surveyed leaders from more than 800 manufacturers in 19 countries about their priorities and concerns. All had turnover of more than £150m a year and hailed from a range of sectors, from automotive and chemicals to food & beverage and life sciences.
According to the research, some 83% of leaders said they believe new technology will transform the way their products are made over the next five years, while a similar proportion felt their business would not be able to survive more than three years without further investments in new digital technologies.
‘Decision paralysis’ hampers digital initiatives and makes it hard to progress
Worryingly, though, fewer than 10% said they considered themselves to be “digital leaders” while some 65% classed themselves as “digital laggards”.
Maggie Slowik, a global industry director at IFS, says that some of this reticence is down to concerns about the costs and disruption associated with digital transformation projects. Additionally, many respondents spoke of a lack of “clear strategy” around digital transformation, which might include setting clear goals, identifying KPIs and creating a clear implementation and adoption roadmap.
“Unfortunately, most manufacturers are still in the early stages of digital transformation, running pilot projects or deploying digital tools but struggling to move beyond these initial steps,” says Slowik. “Many are confused about how to get the best out of new technologies like AI; they are also fazed by the pace of change and sheer volume of options out there. The resulting ‘decision paralysis’ hampers digital initiatives and makes it hard to progress.”
Better control over data
Manufacturers must urgently tackle these blind spots, as technology is likely to play an outsized role in addressing the industry’s pain points over the next five years.
The area of digital innovation that most concerns leaders is how to harness the power of cloud computing, says Andrew Burton, an industry director for manufacturing at IFS. Manufacturers have traditionally taken a conservative approach to technology with many firms still relying on legacy IT infrastructure, such as on-premise services, he explains.
Yet this creates barriers that can hold firms back. Many can find it harder to push and scale new technologies such as AI or react quickly to change, while also facing a much greater IT maintenance burden. More crucially, firms not operating in a cloud environment often struggle to process the large volumes of insight-rich data they generate.
“Data is the lifeblood of any leading company these days as it enables you to better understand your customer, make smarter decisions, operate more efficiently and model both opportunities and risks,” Burton says. “By moving to a secure cloud environment, manufacturers can get a much better oversight of their data landscape, breaking down silos and extracting what they need with ease.
“All stakeholders can access and analyse this information remotely helping to drive smarter business decisions and efficiency gains, with little in the way of downside risk.”
Robust data processes can also make it much easier for firms to manage regulatory compliance issues, especially the growing burden of meeting sustainability regulations. Manufacturers are increasingly expected to report detailed ESG data from across their operations, but more than a third face challenges in collecting and managing the necessary information, putting them at risk of significant fines and reputational damage.
“Manufacturing firms are genuinely trying to develop robust sustainability strategies that go beyond a box ticking approach,” says Burton. “But without effective data processing arrangements facilitated by the cloud, the job is so much harder.”
Build smarter
Beyond the cloud, a host of other digital solutions are now available to help firms improve logistics, offset supply chain risk, refine production processes and model financial decisions. IoT technology is also helping to enhance operations on the shop floor.
Take for example the use of sensors to predict when machinery is close to breaking down, allowing firms to order in replacement parts in advance to avoid costly pauses in production. Encouragingly, almost two-thirds (63%) of manufacturers say they are starting to deploy this technology, which is a reassuring trend even if the industry still has some way to go to achieve a more fully comprehensive level of monitoring.
Innovations in AI, machine learning, AR and VR will enable manufacturers to do even more in future, adds Slowik. However, firms will only be able to reap the benefits with a change in mindset, she believes.
“Digital adoption is too often seen as a burden or challenge, when in fact it is about being more agile and future-proofing your business,” she says. “Our survey research shows digital leaders are already reaping the rewards of their investments, with returns evident in metrics like a 50% increase in agility, a 44% increase in operational efficiency and a 44% increase in enhanced data-driven decision making – well above the industry average.”
The IFS difference
IFS develops and delivers cloud enterprise software for companies who manufacture and distribute goods, tailoring solutions to firms’ industry and functional needs. The benefits of applying a consistent digital environment for organisations offers clear benefits, such as those seen at the robotic solutions provider Cimcorp Group, which has implemented the IFS Cloud to create an enterprise-wide IT system.
Cimcorp makes advanced robotic solutions for intralogistics that are used to optimise material flows in warehouses, distribution centres and manufacturing facilities in 40 countries. The firm relies on its IFS-built, global IT system to ensure employees have a consistent digital environment wherever they work in the world.
“The aim of moving to a single IFS platform was to reduce complexity, which often translated into costly delays,” says Burton. “Since adopting IFS in 2016, Cimcorp has been able to unify vast quantities of data from disparate locations, reduced unnecessary work and improved decision-making through real-time access to information.”
IFS also worked with Cheer Pack North America, a global leader in packaging which is run as a partnership between three manufacturing giants: Hosokawa Yoko from Japan, Italy’s Gualapack and CDF Corporation from the US. Explosive growth at Cheer Pack had required it to rapidly expand its manufacturing operations and workforce. But the firm faced pressure to maintain production volume and product quality in the face of rising customer demand.
Against this backdrop the firm integrated major new ERP and CRM systems based on IFS’s cloud architecture. IFS also helped it roll out Microsoft Surface tablets to key staff, enabling them to interact with the IFS platform on the go, anywhere in the plant.
“By being able to answer questions from customer service or sales quicker, a warehouse coordinator can now get answers to customers faster,” says Slowik.
By being able to answer questions from customer service or sales quicker, a warehouse coordinator can now get answers to customers faster
“Manufacturing is also able to order the parts they need in a timely manner and keep production processes flowing. Overall, we helped Cheer Pack to increase efficiency in its warehouses and enhance its competitive positioning.”
Overall, IFS is committed to helping manufacturers become more agile, resilient, productive and profitable. Whether it be re-engineering existing products to deliver more value, unlocking new revenue streams through circularity and servitisation, or simply delivering more with fewer resources, the firm has enabled customers to garner huge benefits through its best-in-breed capabilities.
Yet a large proportion of manufacturers are still at a very early stage on their digital journeys and need to take a more proactive stance.
“Many manufacturers have become too comfortable with their existing systems, and significant events are often required to force change. But this sudden change can come at an unplanned financial cost and impact the business,” says Burton. “Even if manufacturers have already made investments in digital initiatives, it is critical to keep pace with the changes the technology undergoes to ensure they always stay current.”
As manufacturers look to compete in a digital world, it’s increasingly clear that cloud software can help leaders optimise their operations and workforce, while also helping to underpin the forward-thinking strategies that will help them navigate a rapidly changing manufacturing landscape.
To find out more visit IFS
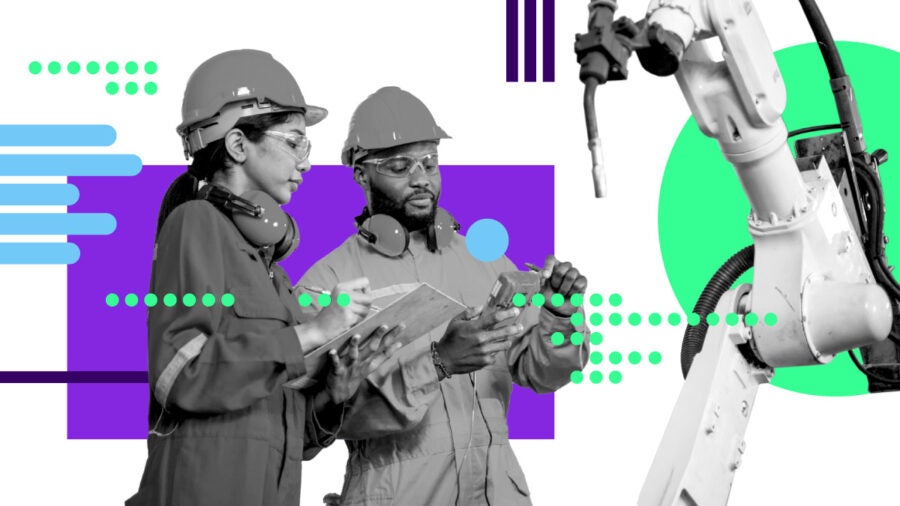
In many ways there has never been a more uncertain time to be a global manufacturer. While there are still huge opportunities out there for the taking, long-standing problems such as economic volatility, talent shortages and supply chain risks continue to put pressure on firms.
Moreover, new and more complex business challenges have come to the fore, including a fast-evolving regulatory landscape, the increased risk of cyberattacks and the disruption caused by rapid technological change.
This requires new strategies if manufacturing leaders are to thrive in a changing world and, in turn, many are turning to innovation and embracing smart manufacturing technologies to improve their competitive positioning.