Transforming computer-designed ideas into physical objects by applying layers of materials with a 3D printer is moving beyond early-use cases in manufacturing to make logistics more efficient and reduce costs across the supply chain.
MH Development Engineering, specialists in engineering bespoke systems and products, installed a 3D printer to enhance both its manufacturing business and systems design for research and development.
When creating systems that solve engineering problems, the company must be able to test concepts quickly. The 3D printer has aided this process by allowing prototyped parts to be created overnight.
“We wake up the next morning to an email from the printer telling us it has finished the components, while we are making our morning coffee,” says Amy Taylor, a director at MH Development Engineering, which is currently working on electric vehicle projects as a direct result of buying the printer.
“The printer has reduced the cost of second-operation tooling and provided us with an additional income stream in terms of straight make-to-print manufacturing for our customers,” Ms Taylor adds. “We are even printing packaging to house delicate components for one customer, as the printed material is strong and protective yet lightweight enough to optimise freight costs around the world.”
Leeds-based Crispin Orthotics, which manufactures made-to-measure orthoses for the NHS and private sector, uses 3D printers to replace multiple components, which previously made up a product, with one single finished item.
The company can 3D-scan leg braces, insoles and casts for broken limbs to match the person being treated, drastically reducing the logistics and supply chain.
3D scanning and printing have revolutionised the speed and quality of parts we’re able to produce for clients
The required body part is scanned with the 3D image and then imported into Crispin Orthotic’s design software, which orthotic technicians use to adapt the model and make positional changes, such as altering the angle of a joint.
The adjusted model is sent to the design team who create a 3D orthotic device around the virtual model. Printing the model with a 3D printer from HP has halved Crispin Orthotic’s cost per part for producing orthoses, removing the need for multiple components in the supply chain and assembly.
“3D scanning and printing have revolutionised the speed and quality of parts we’re able to produce for clients,” says Mark Thaxter, managing director at Crispin Orthotics. “Having the ability to create a bespoke device that is lightweight, durable and accurate to 0.5mm has obvious benefits to the user.”
Using 3D scanning and printing provides greater freedom on the design of products, particularly those with complex geometry. And by providing the ability to vary the thickness of a device in certain parts, it allows companies to produce products not possible with current manufacturing methods.
Croom Precision Medical, which manufactures medical devices, has been utilising additive technology for product iteration and production support since 2007. Last year, the company invested in metallic additive manufacturing technology, placing it in a regulated production environment.
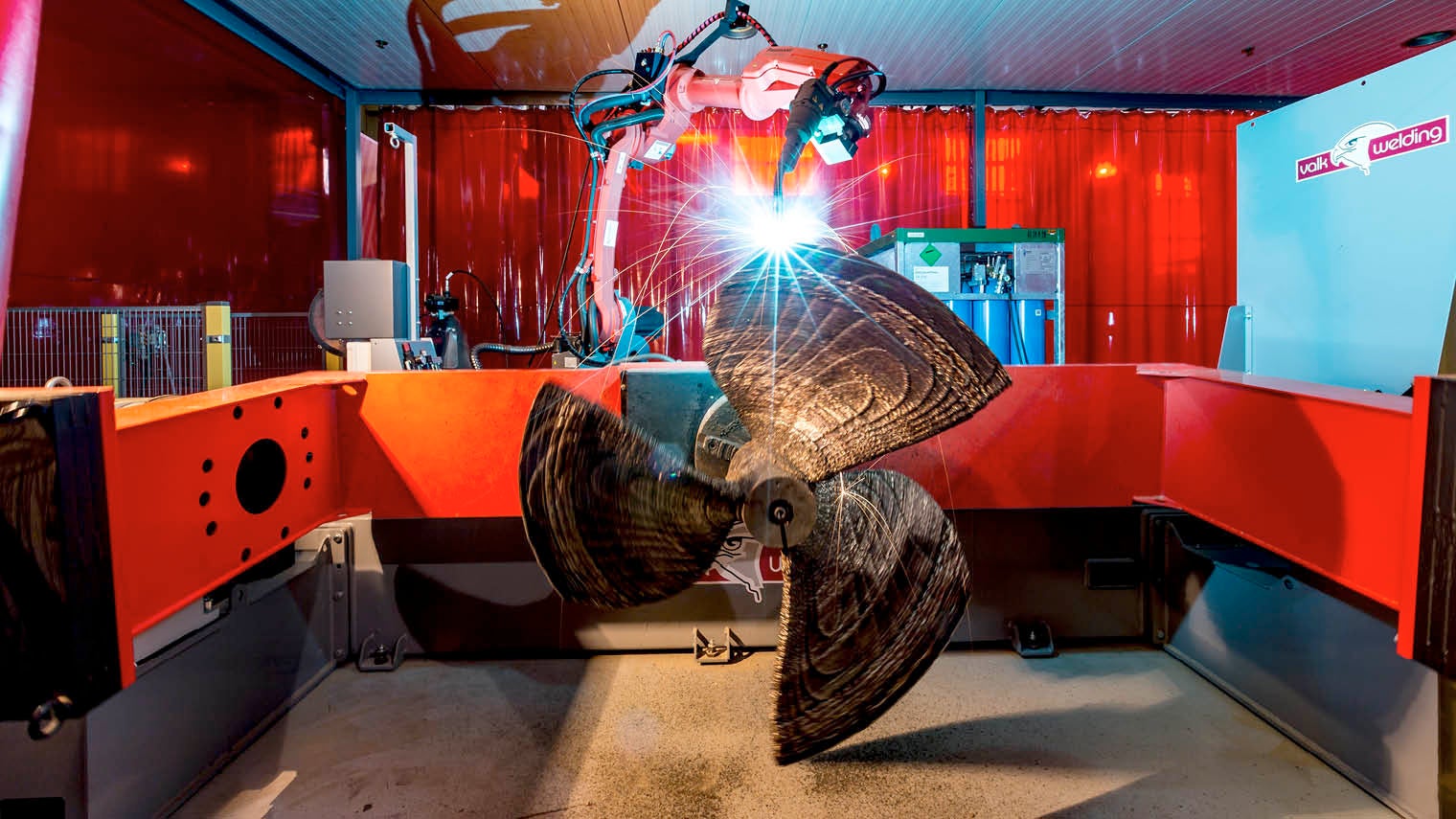
RAMLAB at the Port of Rotterdam combines additive and subtractive manufacturing technologies to 3D-print large ship components
3D printers from engineering firm Renishaw enable Croom’s internal research, development and innovation team to look at all aspects of the additive process, from the incoming materials inspection to the post-processing supply chain.
“It has been an extremely useful technology in creating quick and accurate prototypes for customer use,” says Patrick Byrnes, Croom’s managing director. “It’s imperative that we gain a substantial understanding of what the process is doing at any one time. The technology ensures we supply accurate and compliant parts to our customers.
“Through this technology, we have been able to serve markets we never thought possible. On the other side, we are now dealing with a new group of suppliers from a material and equipment aspect. This has also been a steep learning curve where relationships are formed on evolving competencies on both sides of the fence.”
The Port of Rotterdam, the largest in Europe, deployed the world’s first class-approved 3D-printed propeller. Previously, if a vessel came into port needing a replacement part, it could take months to deliver. It was also costly to keep large stockpiles of parts in warehouses around the world.
To tackle this challenge, the port opened an on-site facility, RAMLAB, which combines additive and subtractive manufacturing methodologies, including a pair of six-axis robotic arms capable of additively manufacturing large metal industrial parts. Assisted by software firm Autodesk, the hybrid approach allows RAMLAB to 3D-print large ship components in metal and then finish the pieces within a matter of days, saving time and money without sacrificing precision or performance.
“With the work being done at RAMLAB, the group hopes to accelerate the cross-industry adoption of hybrid manufacturing for making large-scale parts on demand,” says Vincent Wegener, managing director at RAMLAB. “Our aim is to make the Port of Rotterdam not just an important gateway for Europe, but also a leader in the development of new manufacturing methods.”
From product development and manufacturing to maintenance and delivery, managing the supply chain for a product made up of many materials is a deeply complex task. 3D printing continues to gain pace across sectors as a technology for improving logistics and greatly simplifying this process.
As 3D printing moves towards the mainstream, it is set to unlock millions of pounds in cost-savings, which businesses can reinvest in their research and development to progress innovation.
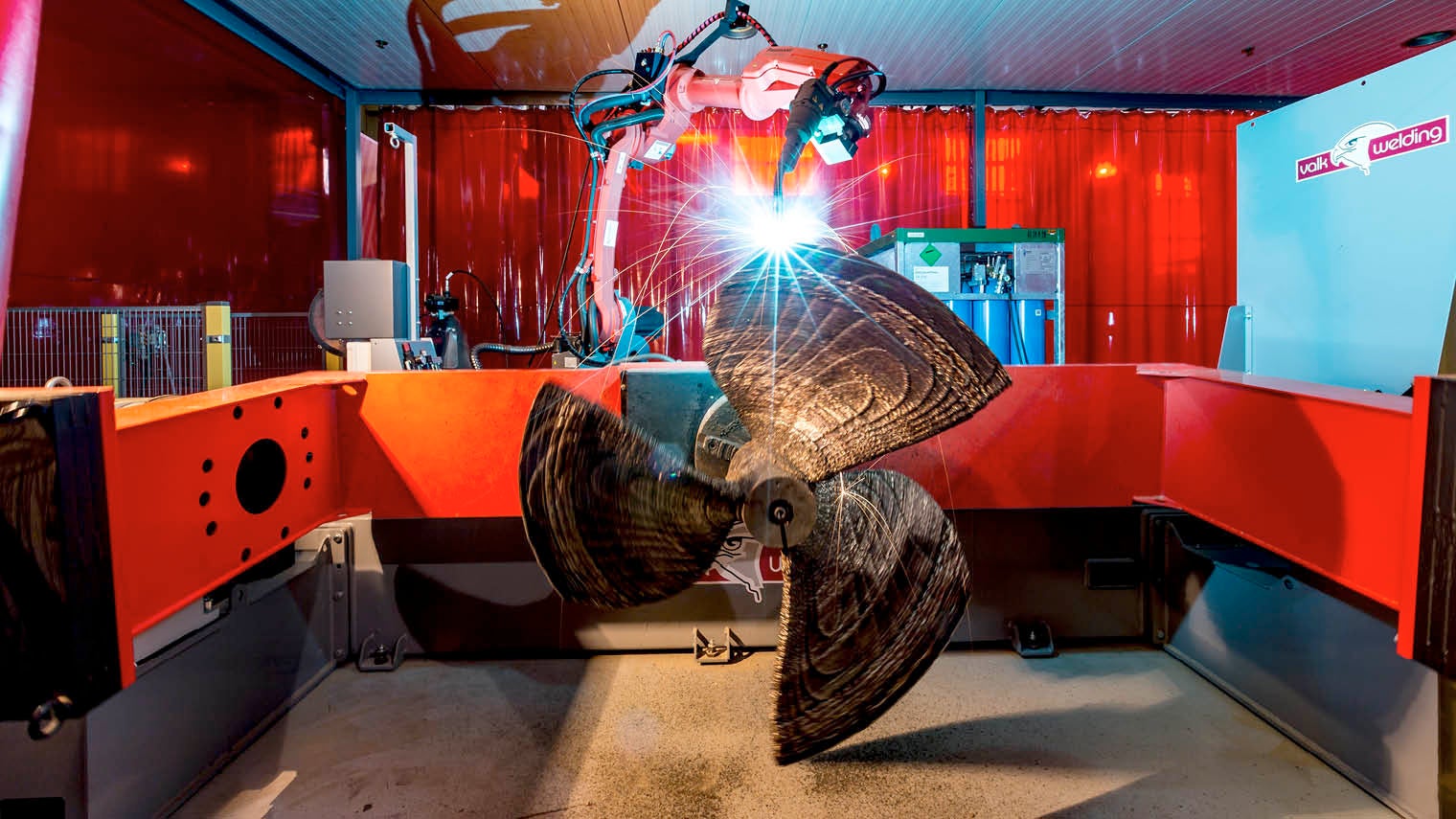