The food industry is undergoing huge transformation, with the emergence of new super markets, new ingredients, and new proteins; retailers coming up with new ideas, from smart packaging to clean labelling; and new legislation to comply with. This creates massive challenges for food manufacturers.
However, their ability to innovate and adapt in order to meet those challenges makes the factory the real trailblazer in the world of food production.
Factories have always been smart, and they are getting smarter
Spare a thought for the factory planner, tasked with ensuring that output meets demand, while factoring in weather patterns that can affect yield, transport issues that can affect deliveries, and even which cookery programme people watched on TV the previous night that could influence what they will want to eat the next day.
For example, I recall one company that manufactured sandwiches and whose main outlets were motorway service stations manually adjusted sales forecasts by up to 40 per cent based on whether certain football teams were playing at home or away, to account for the movement of their supporters.
All of this information has to be gathered and fed into the factory systems, and this is what factories have been doing for decades, admittedly using older technology and mainly data from internal sources, like sales and forecasts. But factories have always been smart, and they are getting smarter.
New technologies, such as artificial intelligence (AI) and the internet of things (IoT) enable large volumes of external data to come into the factory environment via the cloud and integrate with the internal data for analysis. This provides the clearest insights into what might happen to a production plan, and allows the factory planner to make better decisions in real time.
The external data can be drawn from a variety of sources. Drones, for example, are being deployed to monitor crops and estimate yields, generating remote data that can be sent by growers and suppliers to buyers. Ultimately it can be fed directly into factory model.
Nowadays, most delivery trucks have some sort of GPS system that makes them visible and able to be tracked. With this data planners can accurately predict a truck’s arrival time at the factory and staff production accordingly. Likewise if the truck is likely to be delayed by heavy traffic, other delivery slots can be rearranged and staff can be organised to be available when they are needed.
Bringing this remote data into the factory environment creates efficiencies, saves costs and improves yields.
Another pillar of the food business is automation, a new technology for many industries, but adopted by food factories years ago to monitor, measure, adapt and improve products.
Take rice, for example. In the factory every single grain of rice is measured for colour, length and breakages to differentiate between premium and lower grades of rice. I saw this process 20 years ago, using much less sophisticated technology of course. Food factories today are using the latest AI-based laser systems to check every individual item of product for size and colour, and reject any that don’t meet the exact specification, driving up quality, speed and cost efficiencies.
Automation technology is evolving to become smarter and more versatile, with greater use of AI to self adjust to maximise yields, and to drive efficiencies in other areas such as production-line cleaning. When a factory switches from making organic to non-organic products, or allergens to non-allergens in products, the washing of the line is critical, but can take four hours to complete – a huge amount of production time. AI-controlled self-cleaning lines are the solution.
That said automation in food factories does have its limitations, especially where processes rely heavily on dexterity. For example, it is still more cost effective to fillet fish by hand. Machines can be programmed to do it, but they lose around six per cent of the fillet. With their 3D vision and more accurate sense of touch, humans can get higher yields with certain products.
For this reason I don’t see robots ever completely replacing people in factories. Yet the same technology is providing solutions to that other industry challenge: labour shortages. The trend we are seeing is for more ‘co-bots’ – people working alongside robots, in the factory space. This technology is smart, flexible and able to take on much of the mundane work done by an operator where it is possible to do.
Automation, AI, IoT and the fact that factory assets are no longer autonomous but connected to networks and other database handling environments, is the key to unlocking data that determines so many factory decisions and operations. For the quality management team, this data is crucial.
The modern food factory is the unsung hero of the food industry
Retailers can and frequently do conduct on spec audits of the factories supplying them with products. Failure to provide the right data in a timely manner can lead to huge fines or contracts being terminated. I’ve seen companies that have spent a fortune on their line lose it overnight because of a failed audit. The key to avoiding that is to have everything connected – quality systems and information, factory systems and information – and be able to produce required data very quickly.
With that combination of data, people, automation, AI and IoT, we have the technology infrastructure – the digital string – that pulls it all together. Today we have factories that are effectively self monitoring and factory planners making better production decisions on labour usage, product specifications, and speed of line, in a more sophisticated way than people could ever appreciate, all in real time.
The modern food factory is the unsung hero of the food industry, at the very heart of that unique field-to-fork food journey. When people talk about the future of food, in the factory the future is already here.
Discover ways to help the unsung heroes of the factory reach new levels of efficiency here: www.ifsworld.com
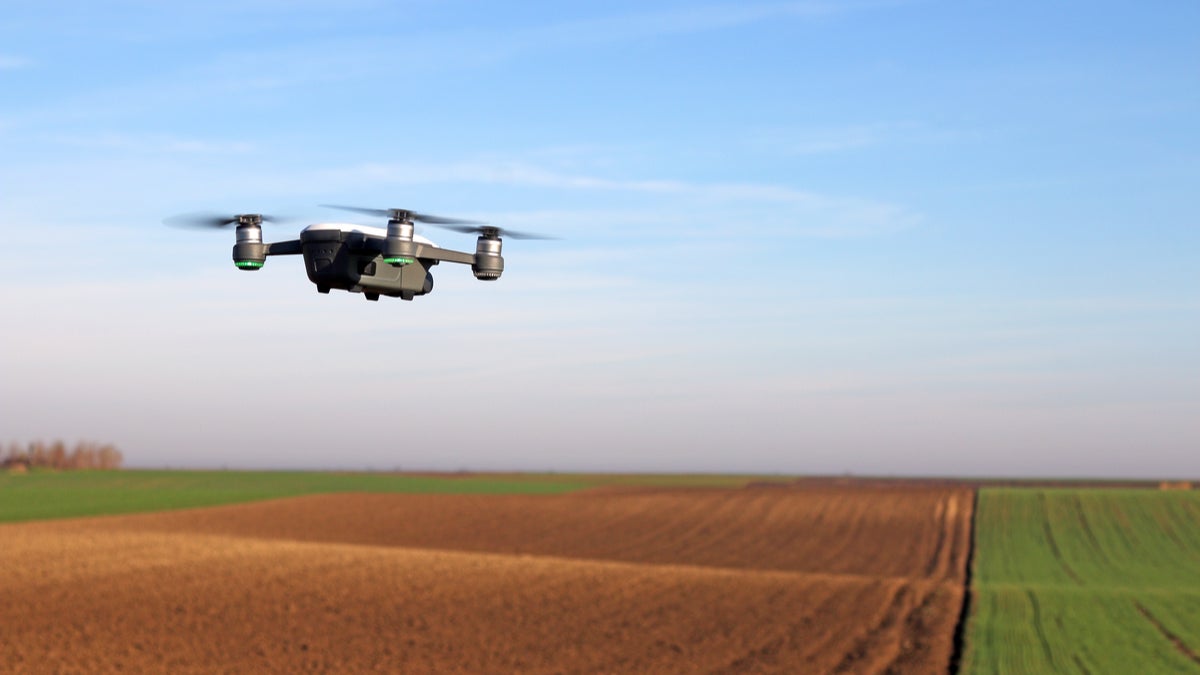
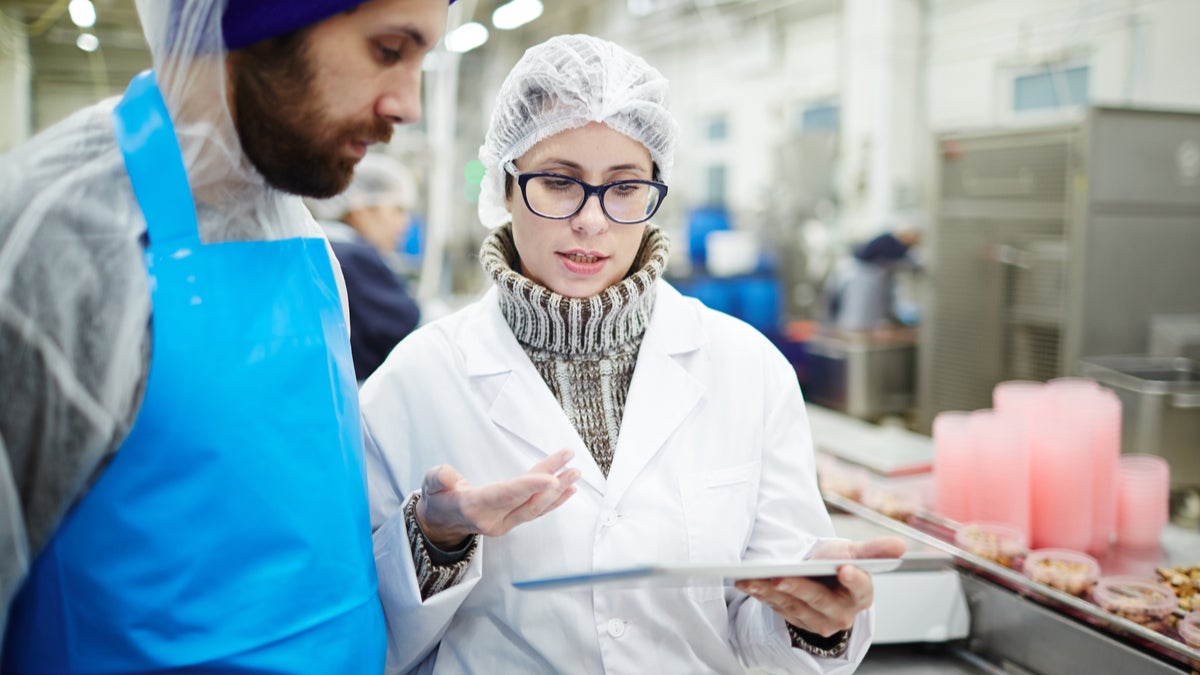