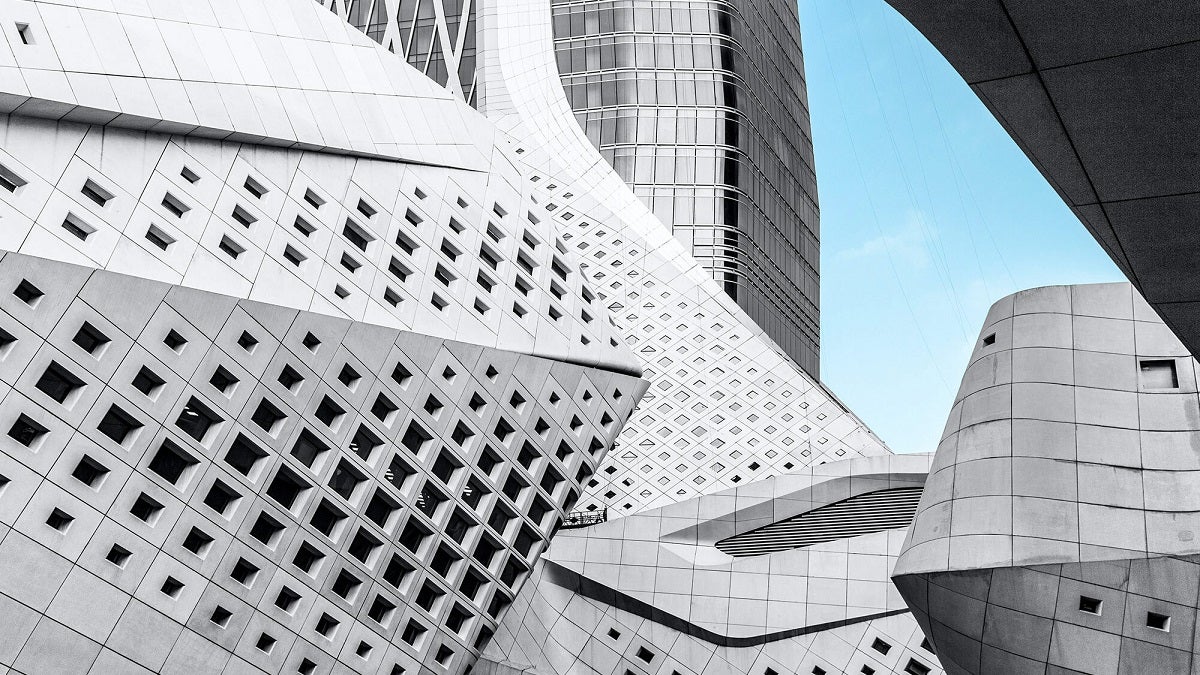
Digital twins
Traditionally, construction firms only delivered the building itself. If it didn’t leak when it rained and the doors and windows opened and shut, then effectively your job was done and you moved on to the next project. But in the modern world there’s also a digital version of that building to deliver — its digital twin — which is arguably just as important as the physical building.
These twins go beyond 3D models by providing information on, for example, the material a wall is made of, where it came from, whether there’s a cavity inside of it, and much more. But to get to this point you need to do the hard work of building up and organising the data that informs digital twins.
On the construction side, new skills are also needed to deliver them, so individuals with information architecture and modelling abilities may need to be added to existing teams. But digital twins are causing more disruption during the operations phase of the building.
Facilities maintenance teams need data on how the building is functioning to do their job effectively — and previously they haven’t had much to go on. So a digital version of the building that can be handed over post-construction is really disruptive.
3D printing
3D printing (otherwise known as additive manufacturing) is already quite widely used in the construction industry. One of the main benefits is repeatability. For example, if you have ten printers running through the night producing construction components, and the quality of those components is up to standard, that’s potentially as revolutionary for the construction industry as the Ford assembly line was for manufacturing.
What makes this technology even more exciting is the potential to move it on-site. Think about it: if you’re building 100 instances of something 50 miles from the site where they’re needed, you’ll eventually need to transport them there. But if you move the 3D printer to the site instead, you eliminate that need, which reduces logistics costs, traffic and emissions.
Although 3D printing used to be limited to silicone and plastic materials, printers that can print with metal are also becoming available, which represents a significant advance in the technology. At the same time, the printers themselves are also becoming larger. In fact, there are projects in the UAE where 3D printers are producing eight by twelve-meter wall sections, in metal, in a matter of hours, which are then being used in skyscrapers.
AR & VR
Both these technologies are disruptive, but AR is more applicable today because it deals with the intersection between the physical world and the digital one. So if you have an existing space and you want to see how certain changes to it might look, you can use AR glasses or a phone app to overlay those changes onto it — and that’s clearly useful in the construction industry.
For example, you could visit a half-finished building, put on some AR glasses and see where a wall is going to extend out from. But you could also click on a physical window or other object to view information about it, which is another strong use case for the technology.
VR, on the other hand, is purely digital. It allows you to immerse yourself in a space before it exists in the physical world. That means you can see not only how it will look, but how people might interact with it too. You can then make any necessary changes to the design before you build it. That’s very important in the construction industry, because the sooner you can make changes the better.
Robotics and automation
Modern assembly lines incorporate robotics in various ways, and similar technologies are becoming increasingly prevalent in construction — a trend that will continue to grow as the number of off-site construction facilities increases. But we also need to ensure that these robots can safely work alongside humans on-site, which is a more challenging environment than a factory floor.
However, robots can actually help to improve on-site safety too. That’s important given that health and safety, which the construction industry hasn’t always excelled at historically, is a key concern today. For instance, using robots for work at height can help to prevent accidents. Or you could use a robot with a camera to assess the safety of certain locations so you know exactly what you’re dealing with before any work begins.
Looking further ahead, there’s no reason why we can’t send robots to a site to build what needs to be built. But there are always unforeseen circumstances that humans can adapt to, so these robots will need to be capable of adapting as well — and that will require AI.
Smart materials
Smart materials encompass things like self-healing concrete — i.e. concrete embedded with microcapsules containing various healing agents to autonomously repair cracks — as well as more sustainable materials, which are particularly important given that approximately 40% of global carbon emissions come from the built environment. In other words, smart materials have a significant role to play in helping us to build a better world.
The materials used within a building can also be “smart” in the sense that they’re capable of receiving and transmitting information about themselves and the wider environment. That could be something as simple as a brick containing a sensor that can detect when there’s a fire nearby, or if there’s too much airflow around it.
In fact, there are countless different sensors you can use to generate useful data. So if you imagine hundreds of thousands of them embedded throughout a building, you can see how smart materials connect the physical world with the digital one, and feed into the very first disruptive technology mentioned in this piece: the digital twin.
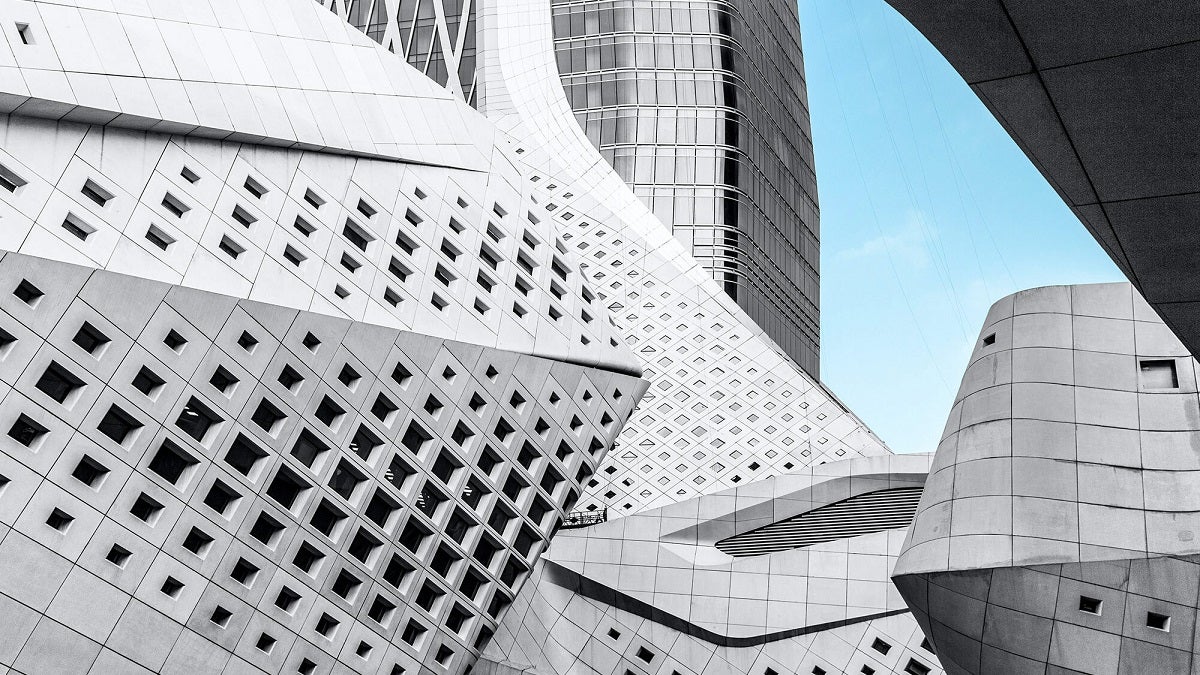
Digital twins
Traditionally, construction firms only delivered the building itself. If it didn’t leak when it rained and the doors and windows opened and shut, then effectively your job was done and you moved on to the next project. But in the modern world there’s also a digital version of that building to deliver — its digital twin — which is arguably just as important as the physical building.
These twins go beyond 3D models by providing information on, for example, the material a wall is made of, where it came from, whether there’s a cavity inside of it, and much more. But to get to this point you need to do the hard work of building up and organising the data that informs digital twins.