From product design studios, engineering departments and manufacturing plants, to schools, hospitals and dental labs, the next industrial revolution has clearly arrived.
For solutions providers at the forefront of this game-changing technology, appetite for uptake of 3D printing in the UK is proving spectacular, as Andy Middleton, senior vice president, Europe, the Middle East and Africa, at Stratasys, explains: “For us, the UK is the fastest-developing and largest market in Europe, showing 70 per cent year-on-year growth.
“The 3D-printing revolution really seems to have taken off in the UK, rethinking the way people work and play, from corporations to consumers, manufacturers to makers.”
PRECISION PERFORMANCE
Stratasys is a world leader in the manufacture of 3D printing equipment and materials that create physical objects directly from digital data. Its systems range from affordable desktop 3D printers to large, advanced 3D-production systems, making 3D printing more accessible than ever. Its clients range from Nespresso to Nasa.
Manufacturers use 3D printers to create models and prototypes for new product design and testing, as well as to build finished goods in low volume. Educators use the technology to elevate research and learning in science, engineering, design and art. Hobbyists and entrepreneurs use it to expand manufacturing into the home, creating gifts, novelties, customised devices and inventions.
All Stratasys 3D Printers build parts layer by layer:
- FDM (fused deposition modelling) technology, known for its reliability and durable parts, extrudes fine lines of molten thermoplastic, which solidify as they are deposited;
- PolyJet technology, known for its smooth, detailed surfaces and ability to combine multiple materials in one part, employs an inkjet-style method to build parts from liquid photopolymers in fine droplets immediately cured with ultraviolet light; and
- WDM (wax deposition modelling) technology produces finely detailed wax-ups for investment casting, particularly in dental applications.
Though the mix of material, geometry, finish and colour may differ with every user requirement, the essentials of 3D printing remain the same: precision, potential and performance.
INNOVATION AND ASSURANCE
Commercial clients are turning to 3D printing to help them work more efficiently and expand production possibilities, while still achieving ultimate final-product realism. Customers are seeking competitive advantage, demanding a combination of cutting-edge technology and high-quality performance.
Unique to Stratasys, triple-jetting technology is PolyJet 3D printing at its most advanced. Not only does this produce the most sophisticated multimaterial prototypes and parts, but it offers surprising workflow benefits.
For mixed parts, it can reduce or eliminate the need for assembly, even when building as many as 82 distinct material properties into a single part in one automated job. Complex products can be prototyped with flexible, rigid, colourful, translucent and opaque components just by hitting “print”.
Stratasys is a world leader in the manufacture of 3D printing equipment and materials that create physical objects directly from digital data
However, for 3D printing to deliver fully on the promises of production teams made to colleagues in the board room, such technological innovation needs to come with a level of business assurance, says Mr Middleton. “Being ahead of the game is almost de rigueur for any successful technology company, but what the market wants is innovation, not risk. As the only company to have achieved material certification fit for the aerospace sector, we understand the need for assurance, too.
“3D printing is a serious business, with big plans. This combination of innovation and assurance is critical for investors, and industry seeking a trusted technology partner.”
ACCESSIBILITY
While talk of the latest technology may be exciting for growth prospects in production terms, it does not tell the whole story.
The future of 3D printing is about much more than just kit. In effect, it is not so much the “what” that matters, as the “who”, “when” and “where”.
Access and availability are the multiplying factors that will leapfrog the process forward, faster and further into the mainstream. As with many developments in the digital economy, portals and cloud-based solutions will therefore prove global market-makers for 3D printing.
Stratasys is again in the vanguard of current developments in this connective and creative space, via its Brooklyn-based subsidiary MakerBot, which maintains the Thingiverse design-sharing community.
The implications of a widespread upsurge imminent in access and availability are enormous for 3D printing, and will both complement and accelerate the way the world of work is changing as a whole, concludes Mr Middleton. “This virtual ecosystem for 3D printing will bring together the greatest number of people and diversity of global users, with maximum flexibility in terms of time and place,” he says.
“Collaborative working is the way forward for manufacturing, and the explosion of access and availability in the 3D-printing industry will both feed and speed that change. We are all in the business of co-creation now.”
NASA CASE STUDY
3D PRINTED FOR LIFE ON MARS
An agile white vehicle roams the Arizona desert, manoeuvring the unforgiving terrain as the wind and sun beat down and temperatures swing from one extreme to another. Nasa astronauts and engineers are test-driving a rover over rocks and sand, up and down hills in an environment that simulates the brutal conditions of Mars.
To design such a tenacious and specialised vehicle, Nasa drew on ingenuity and advanced technology. About 70 of the parts that make up the rover were built digitally, directly from computer designs, in the heated chamber of a production-grade Stratasys 3D Printer. The process of FDM technology, or additive manufacturing, creates complex shapes durable enough for Martian terrain.
PRECISION PERFORMANCE
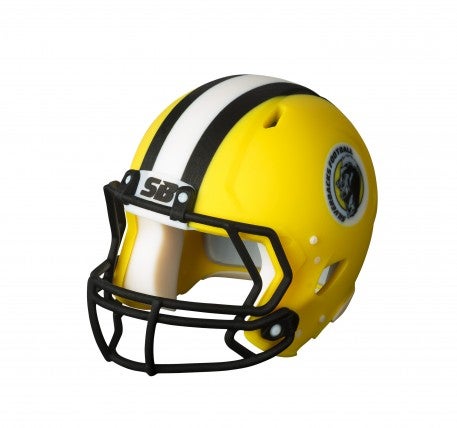
INNOVATION AND ASSURANCE
