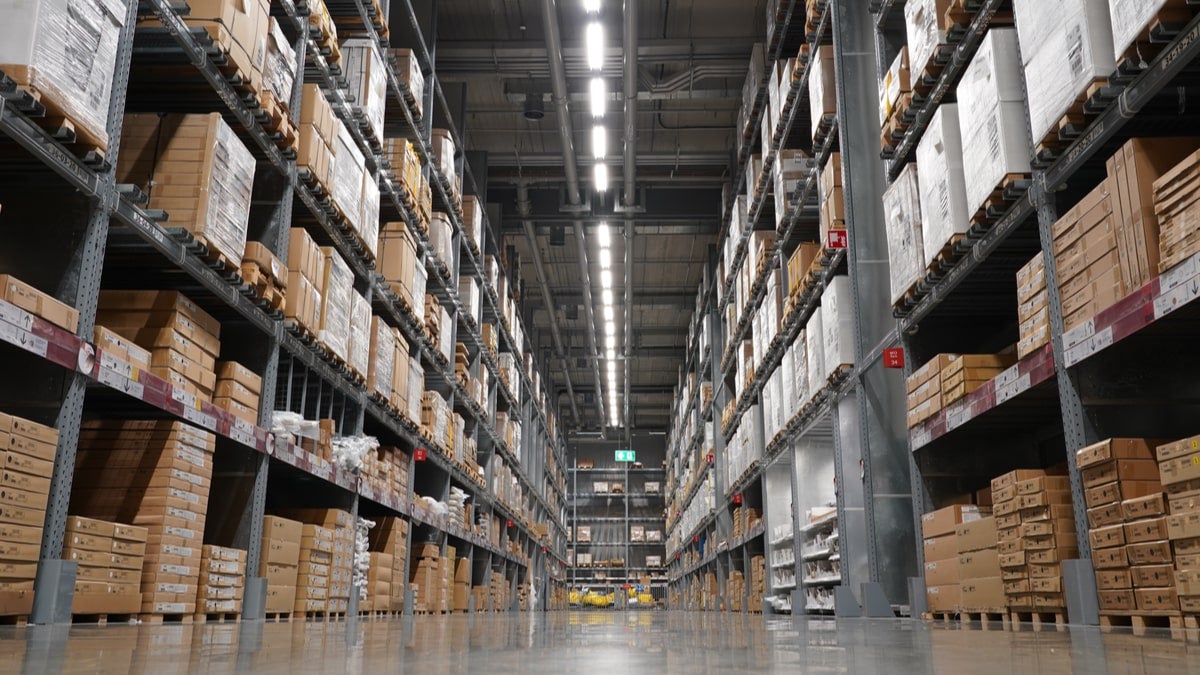
The pandemic-induced growth spurt in UK online sales over the past 18 months has forced etailers to expand their operations to such an extent that they spent a record £6bn on building new warehouses in the first six months of this year, compared with £2.7bn in H1 2020, according to Knight Frank.
The estate agency forecasts that the amount of warehouse space being created in developments exceeding 4,500m2 nationwide in 2021 will be double last year’s total of 1.9 million m2. Yet no matter how quickly these big sheds are being built, the demand for storage facilities still far exceeds the supply.
“The availability of high-quality space in particular has diminished owing to robust levels of occupier take-up over the past 18 months,” reports Charles Binks, partner at Knight Frank and head of its logistics and industrial agency. “Our figures show that only 3.9 million m2 is available – and much of that space is either under offer already or not of the right specification for potential occupiers.”
Struggles to meet demand
The industry finds itself in this situation because of two main factors: Covid and Brexit. At the start of the pandemic, fears of shortages prompted many consumers to stockpile household essentials. When supermarkets introduced rules to prevent hoarding, this put their home-delivery capacity under massive pressure.
Although the vaccination programme has since enabled high-street retailers to reopen, a significant proportion of consumers who started doing their shopping online at the start of the crisis are sticking with the relative ease and safety that ecommerce has offered. This has led to intense competition among ecommerce specialists (and clicks-and-mortar retailers) for prime warehousing facilities.
Research by Savills indicates that Amazon leased a quarter of all available space in the UK in 2020. In August this year, the John Lewis Partnership signed an 11-year deal to lease a 93,000m2 distribution centre in Milton Keynes from Tesco. This will support John Lewis’s move from physical retail to ecommerce – during the height of the pandemic, the online channel’s share of the partnership’s total sales jumped from 40% to 60%.
On top of this, the reintroduction of customs controls at the border between the UK and the EU resulting from Brexit has inevitably caused delays to imports and exports. This supply-chain disruption has increased demand among retailers for extra storage space as a precautionary measure.
Binks notes that a shortage of adequate facilities in the right locations is encouraging speculative development, in which warehouses are being built before any companies have been lined up to occupy them.
“There is 840,000m2 of space currently under construction on this basis,” he says. “But, even with this, lack of availability is particularly acute in the big-box market, where occupiers seeking units of 33,000m2 or larger have very limited options.”
To make matters worse, shortages of materials and/or labour are delaying some warehouse construction projects, all of which serves to push up costs.
The general increase in the value of property in most parts of the country has also been having an inflationary effect. Philip Woolner, joint managing partner at Cambridge-based estate agency Cheffins, reports that annual rents for new industrial units in sought-after locations around the East of England are between £110 and £140 per m2, while those for warehouses in the very best locations can be even higher. Only five years ago, the top industrial rents ranged from £75 to £90 per m2.
Factoring logistics into government-led schemes
“The combination of strong demand, very short supply and increased building costs have contributed to a rental growth rate that shows no signs of abating. Without a significant increase in the amount of industrial land coming forward to the market, the supply of high-quality logistics space will continue to be constrained,” says Woolner, who adds that the problem is being exacerbated by planning constraints, such as the time it typically takes to secure permission to build an industrial unit.
So how can the industry get enough space in the right place at pace?
“Perhaps one way the UK could surmount this challenge would be to allocate significant acreage to industrial development in some of the larger state-led schemes,” Woolner says.
He notes that the government is forming a long-term strategic plan to help co-ordinate the infrastructure, environment and new developments in an area that it calls the Oxford-Cambridge Arc, a tract spanning five counties and centring on Milton Keynes. To this end, it started a public consultation this summer.
For its part, Cheffins is seeking interested parties for a 24,000m2 development of mixed-use commercial space (including storage) in Cambridgeshire. It’s hoped that the inclusion of space for research and development facilities in this scheme should attract potential occupiers interested in updating their warehousing and fulfilment processes.
“While logistics might not be the most exciting part of the commercial sector, it shouldn’t be overlooked,” Woolner says. “It needs to be factored into these government-led programmes if we’re to feed the demand.”
The intensifying competition for prime space will encourage innovation in logistics, according to Mike Trainer, real-estate partner at law firm Gowling WLG. He believes that etailers with the proprietary technology that can host the branded websites of other companies – and the capacity to handle fulfilment and delivery themselves – will undoubtedly have a competitive edge.
“Innovation is at the heart of the technology-led online market”, Trainer says, “and logistics is essential in making this all work.”
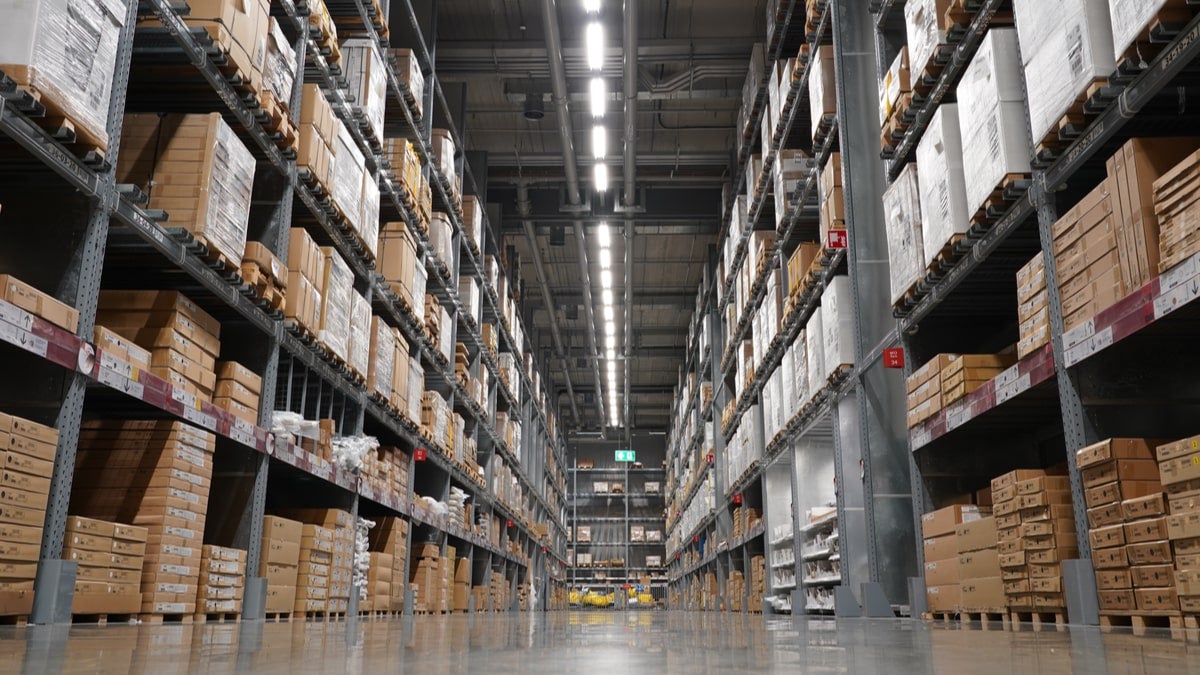
The pandemic-induced growth spurt in UK online sales over the past 18 months has forced etailers to expand their operations to such an extent that they spent a record £6bn on building new warehouses in the first six months of this year, compared with £2.7bn in H1 2020, according to Knight Frank.
The estate agency forecasts that the amount of warehouse space being created in developments exceeding 4,500m2 nationwide in 2021 will be double last year’s total of 1.9 million m2. Yet no matter how quickly these big sheds are being built, the demand for storage facilities still far exceeds the supply.
“The availability of high-quality space in particular has diminished owing to robust levels of occupier take-up over the past 18 months,” reports Charles Binks, partner at Knight Frank and head of its logistics and industrial agency. “Our figures show that only 3.9 million m2 is available – and much of that space is either under offer already or not of the right specification for potential occupiers.”