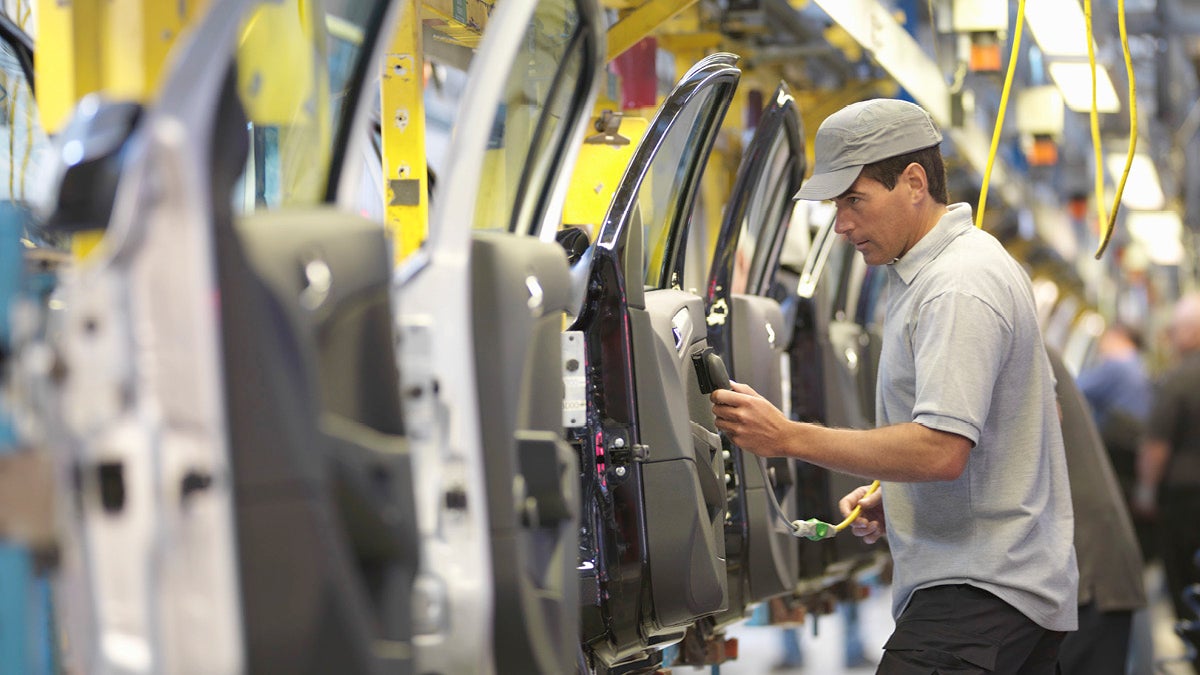
China has been the locus of low-cost manufacturing for decades. But as China’s factories shut their doors in early-2020, and then other countries followed suit, businesses around the globe have been forced to reconsider what has long been considered an expensive way to make products: reshoring.
Reshoring represents the opposite of sprawling global supply chains. Moving production and labour back to business’s home countries, or where the actual demand for a product lies, has become a necessity as global supply chains ground to a halt.
Dr Sam Roscoe, senior lecturer in operations management at the University of Sussex Business School, points out that while globalisation has been the accepted method of mass production for many years, this year its weaknesses are becoming apparent.
“UK businesses have been extending their supply chains in search of low-cost labour since the 1970s. That means we have these hugely complex supply chains all over the world,” he says.
“One of the big issues that’s come up during the pandemic is European companies have seen key sources of supply close. China shut down, then India and recently it’s Latin America. Many weren’t aware of what this could mean for a critical component of their vehicle engine or for a pharmaceutical product.”
Reshoring initiatives could mean survival for some industries
The automotive industry was particularly hard hit by the shutdown of international manufacturing capacity. Vehicle sales plunged during lockdown and, once factories and showrooms reopened, supply was hit by months of delays for deliveries of raw materials, parts and completed products. Researchers at Statista now expect global car sales to drop 20 per cent in 2020 compared to last year.
Companies that can source and make their products locally might therefore be the ones to emerge from the pandemic less scathed than those that favour sourcing from overseas.
Chris Ford, managing director of Ford Engineering in South Tyneside, which manufactures parts for the aerospace and automotive industries, says buying materials and hiring staff as locally as possible has meant the firm has been able to keep working and keep its supply chain intact. The firm has also managed to avoid the rising costs of importing into the UK.
“We don’t source materials from East Asia, but we’re hearing from our contacts that the cost of shipping and air freight has gone through the roof,” he says,
We’re hearing from our contacts that the cost of shipping and air freight has gone through the roof
Businesses may have to accept that the days of searching the globe to find the cheapest labour to make the cheapest products possible may be over. “It has been a very difficult time for the automotive sector over the past couple of years because it is so cost focused. Sales volumes are low at the minute. And global supply chains have become quite fragile because there’s so much pressure on price,” says Ford.
Looking beyond labour costs
To solve the issue of higher labour costs in Europe, some industries are deploying digital technology to replace factory man hours. Aerospace is already making a move into more localised manufacturing through the use of emerging technologies. Rolls-Royce, for example, is trialling 3D-printing technology to make engine parts.
“The automotive industry is also getting into 3D printing,” says Roscoe. “It really opens up the possibilities of more localised manufacturing because it makes your labour costs significantly lower.”
It will take a while to replace the current, human labour-intensive automotive manufacturing model, however, as 3D printing is yet to be deployed on a mass scale.
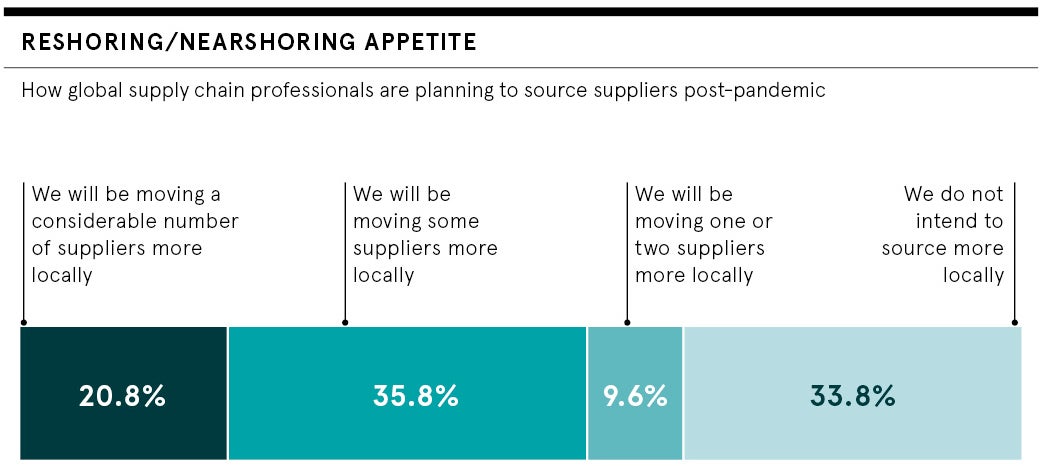
The focus on finding the cheapest labour costs ignores the economic benefits that can come with reshoring initiatives. “By being closer to the centre of demand, you can be more responsive. You can sell products quicker. And if there are shifts in consumer demand, then a company is able to adapt faster,” Roscoe argues.
“At the moment, we’re seeing a huge downturn in car sales, for example. If you’re making your cars in China, and it takes three or four months to ship them here, [when demand drops] stock is already on boats sailing to Europe. You have money tied up in that inventory.
“This idea of being closer to the point of consumption means you can quickly scale production down until demand picks up and you’re also saving a significant amount of money by not needing additional warehouse space. This will bring down your overall costs.”
We’re hearing from our contacts that the cost of shipping and air freight has gone through the roof
Sourcing at home and abroad could be the answer
Yet moving production closer to demand is unlikely to take place completely in the wake of COVID-19. If the vulnerabilities of offshoring have been exposed, but reshoring is prohibitively expensive, the solution perhaps lies somewhere in the middle.
“The reality is we can’t say to all companies, ‘Listen, you have to reshore everything’,” says Roscoe. “Because they won’t; the costs do not make sense. But if we’re arguing that we need to have more resilience in our supply chains, and more flexibility, then companies are going to have to eat some of those costs and begin to look at having a component of their manufacturing based within their home countries.”
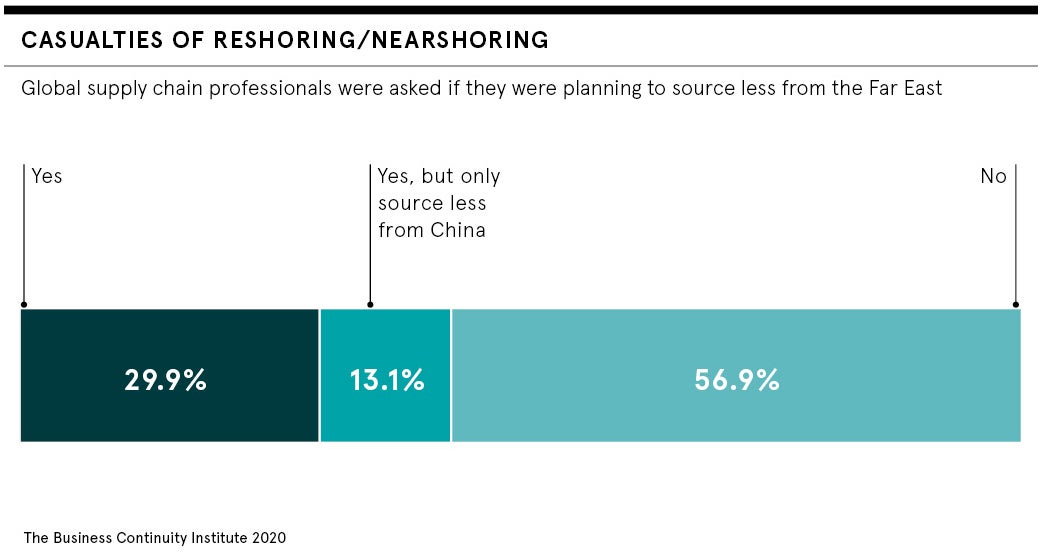
Business costs aside, the potential public health consequences of making goods thousands of miles from where they are needed became clear in the scramble for ventilators in the UK this spring. As COVID-19 infection rates spiralled and individual nations competed to stockpile available medical equipment, the UK became one of many nations urgently calling upon its domestic manufacturers to suddenly design and produce essential equipment.
What are “parallel supply chains”?
A concept Roscoe recommended to the UK’s International Trade Committee (ITC), as it investigated the COVID-19 pandemic and international trade in April, is the idea of parallel supply chains. Under this concept, reshoring initiatives would not aim to dismantle existing global supply chains. Instead, multiple supply chains are set up.
A pharmaceutical firm, for example, could locate a third of its critical drug manufacturing in the UK, while the remainder is still made overseas. Having a parallel supply chain in place would mean local production volumes can be ramped up at short notice and, if one country or supplier fails, there are alternative options available. The ITC has included the proposal in its recommendations to the government.
In extreme circumstances, perhaps a pragmatic approach is needed, one where neither reshoring or offshoring is the answer, but a considered mix of both. “Globalisation was fine when things were relatively calm, but we’re now living in a business environment where we have not only COVID-19, but a possible no-deal Brexit in the next couple of months,” says Roscoe.
“We also have a US-China trade war, which has really driven up costs in tariffs on aluminium and steel. Then we have natural disasters, which are occurring more frequently. Companies are really waking up to the realisation that you can’t just focus your supply chain on low-cost labour and making efficiencies.”
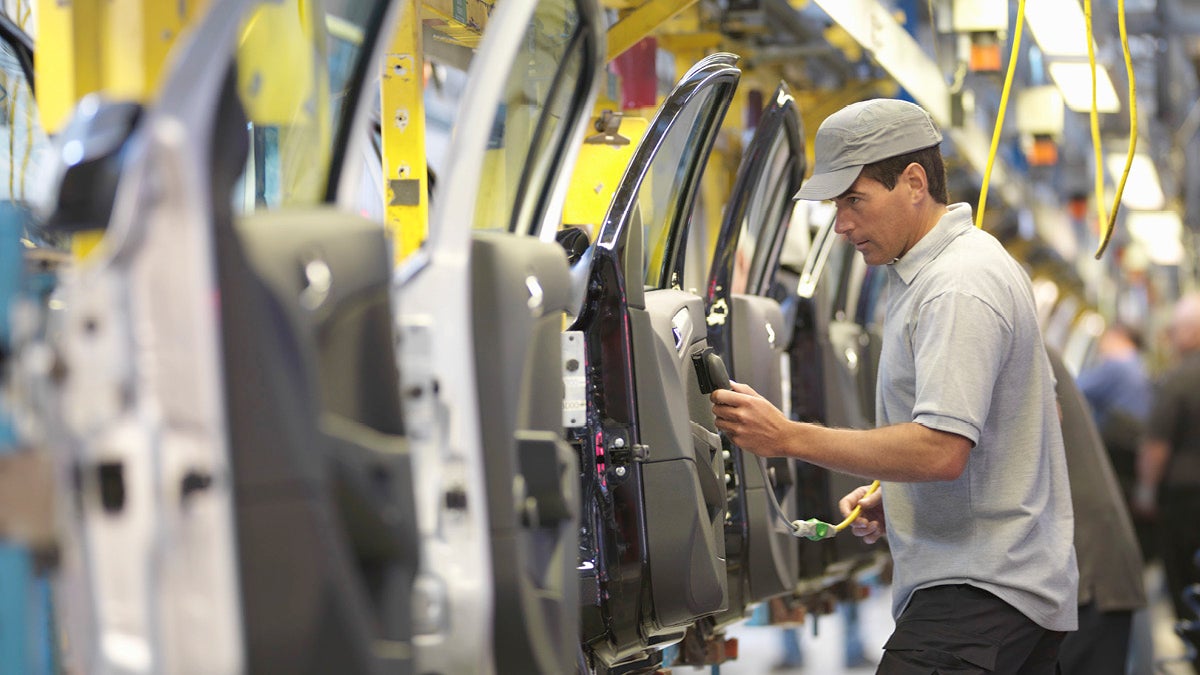
China has been the locus of low-cost manufacturing for decades. But as China’s factories shut their doors in early-2020, and then other countries followed suit, businesses around the globe have been forced to reconsider what has long been considered an expensive way to make products: reshoring.
Reshoring represents the opposite of sprawling global supply chains. Moving production and labour back to business’s home countries, or where the actual demand for a product lies, has become a necessity as global supply chains ground to a halt.