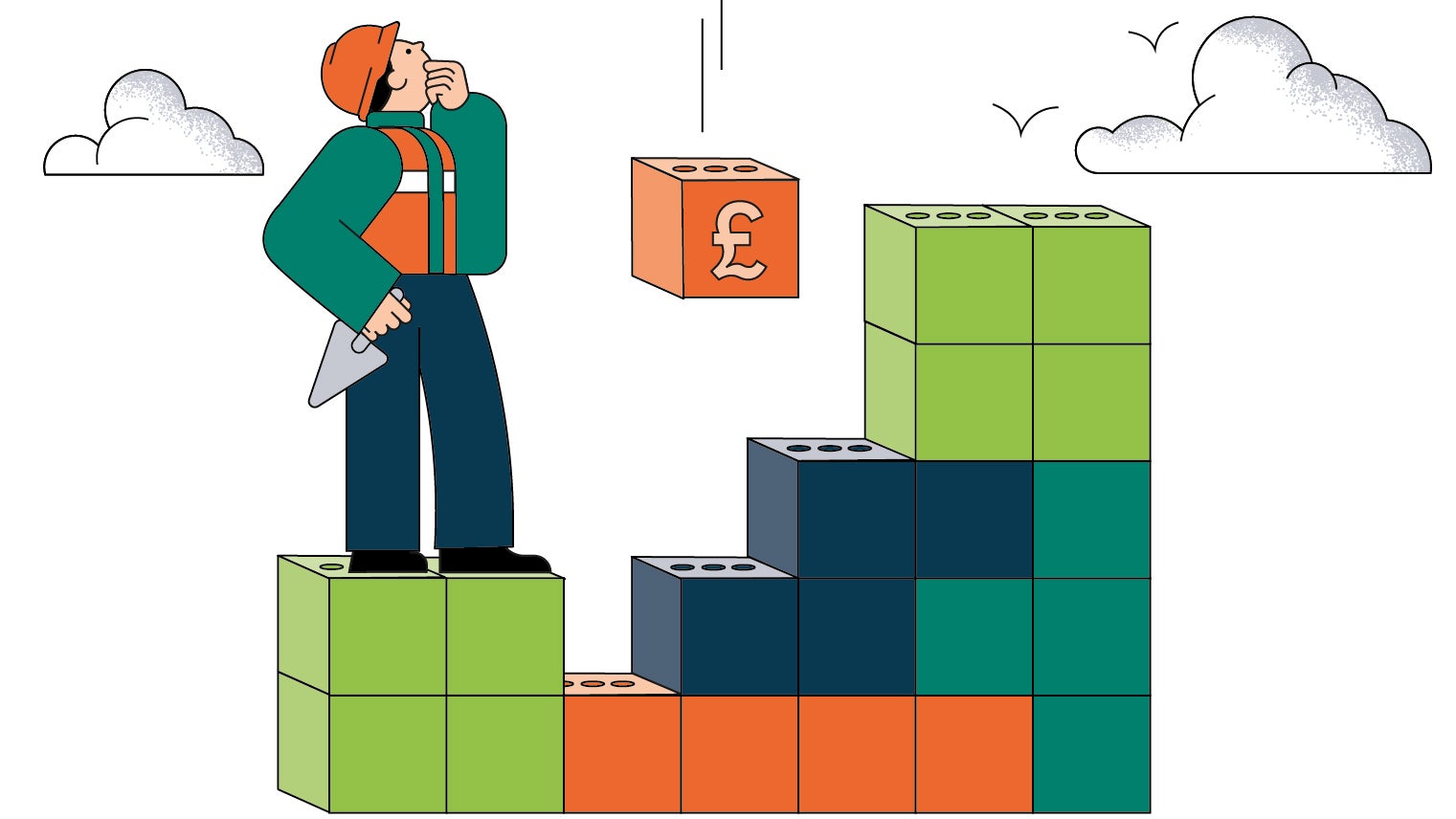
The construction industry has experienced a troubled recovery from the pandemic. Trade tariffs, congested logistics routes, labour shortages, and even climate change are hindering recovery in the construction sector. But the most obvious legacies of lockdown are the shortages of construction materials and unprecedented price hikes.
“The volatility in construction material prices experienced this year is unprecedented,” said Henry D’Esposito, JLL Research Manager, Construction in the executive summary to the firm’s Construction Outlook 2021 report.
“The increases in lumber and steel prices are by far the largest recorded through available government data back to 1949. For other commodities the records are somewhat more recent: aluminum prices have not increased this fast since 1995, plastic since 1976, copper since 2010. The inauspicious distinction this year is that all those records are being broken at the same time. Average material prices for a commercial project increased an astounding 23% in the 12 months prior to August 2021,” said D’Esposito.
What’s challenging is the cascade of disruptions right now. It’s not just one. We’re dealing with systemic issues as well as acute issues right now
It’s tempting to explain away such stark statistics as Covid-related. But there are long-term issues at play, there is no sign of immediate bounce-back.
“The speed of recovery from the pandemic is slower than hoped for as the Purchasing Managers’ Indices indicate,” says Duncan Brock, group director of the Chartered Institute of Procurement and Supply (CIPS). He believes that the scarcity of supplies is unlikely to abate any time soon.
“The Bank of England governor has warned that the UK is likely to go into recession towards the end of the year… This is worrying and supply chain managers will have to draw on their creativity in the sector as affordability rates for housing, for instance, are likely to be affected.
Covid is an obvious reason for the shortages in construction materials. Worldwide lockdowns shut down building sites and factories alike. But while construction has reopened, the processes that facilitate the trade are still faltering. Ongoing lockdowns in China mean that much of its manufacturing is stalled. Of equal, if not more importance, the logistics and supply routes that run through the country have been hit hard. Ports are congested and many urgent supplies are stuck in the stacks. The labour required to ensure the smooth running of the world’s supply chains is unavailable.
But not all of this is due to Covid. The lack of available labour, and the cost of it, are long-term issues that Covid exacerbated.
Geopolitical events are also long-term and difficult to forecast or mitigate. The conflict in Ukraine may have been predicted by political experts but many construction firms were taken by surprise. Brexit bureaucracy jammed warehouses and the Trump administration’s trading tariffs contributed to price fluctuations, such as restrictions on Canadian timber. The effects of these are still playing out and there will surely be more to come.
The shortage of lumber is another ongoing challenge, linked to a tangential cause: climate change. Planning for freak weather events has always been a feature of supply chain management but it’s difficult to tackle such a broad subject as climate change when it is one factor among many.
“What’s challenging is the cascade of disruptions we have right now. It’s not just one,” says Abe Eshkenazi, CEO of the Association of Supply Chain Management. “You’re not just talking about rerouting around an ash cloud, which is temporary and maybe in a few weeks will dissipate. We’re dealing with systemic issues as well as acute issues right now.”
The volatility in construction material prices experienced this year is unprecedented in contemporary history
Addressing systemic issues is a complex task. As gifted as project managers are, reversing the labour shortfall, unclogging ports, rescinding tariffs and solving climate change is a lot to ask. But there are strategies that can address some of the worst effects of materials shortages and even have a positive impact on long-term concerns such as sustainability.
“It’s tough to take our eye off the ball in terms of the acute issues to focus on the systemic,” says Eshkenazi, but he says they shouldn’t take a backseat. “We are not mitigating or minimising the challenges but climate change and the impact on our environment need to be addressed as we deal with the short-term issues.”
It’s easy to leave big change to large firms. They have the resources to research and invest in new methods and materials. But larger businesses can use quick fixes that address systemic flaws but don’t tackle the causative issues. Even if the big operators recover faster, businesses that have taken the opportunity to adapt their long-term processes may recover stronger.
A longer-term approach includes exploring sources or types of materials. Brock says that CIPS research from late 2021 showed that supply chain managers were looking at local sourcing, which would speed delivery times while viable alternative materials could improve sustainability and reduce carbon emissions.
Data and visibility are essential tools to manage supply chains. “If you haven’t developed your risk profile on key commodities and supplies, do it now and use data to find additional risks potentially by geography and sector. Hire people who know how to build resilience into your supply chain,” says Brock.
The speed of recovery from the pandemic is slower than hoped
Solid, practical advice. But data itself is in short supply. Without knowing when the people of China will return to work, we cannot know when supplies will become available or where they will go. “The current unpredictability is creating significant challenges,” says Eshkenazi. Without data, there is no end in sight to materials shortages.
But, the cheapest and arguably the most effective tool for mitigating the crisis of materials supply is available to all levels of builders: communication. Eshkenazi favours talking to tier 1, 2 and even tier 3 suppliers to anticipate and iron out bumps in the supply chain. Likewise, communication with clients goes a long way. It is always difficult to go back on timelines and set prices, but providing timely information to clients may foster the respect that can keep the contract alive despite delays.
Shortages of materials have been something of a wake-up call for the construction industry. The costs of ignoring long-term issues have been made clear and perhaps unprecedented price hikes will prove to be an impetus for systemic change.
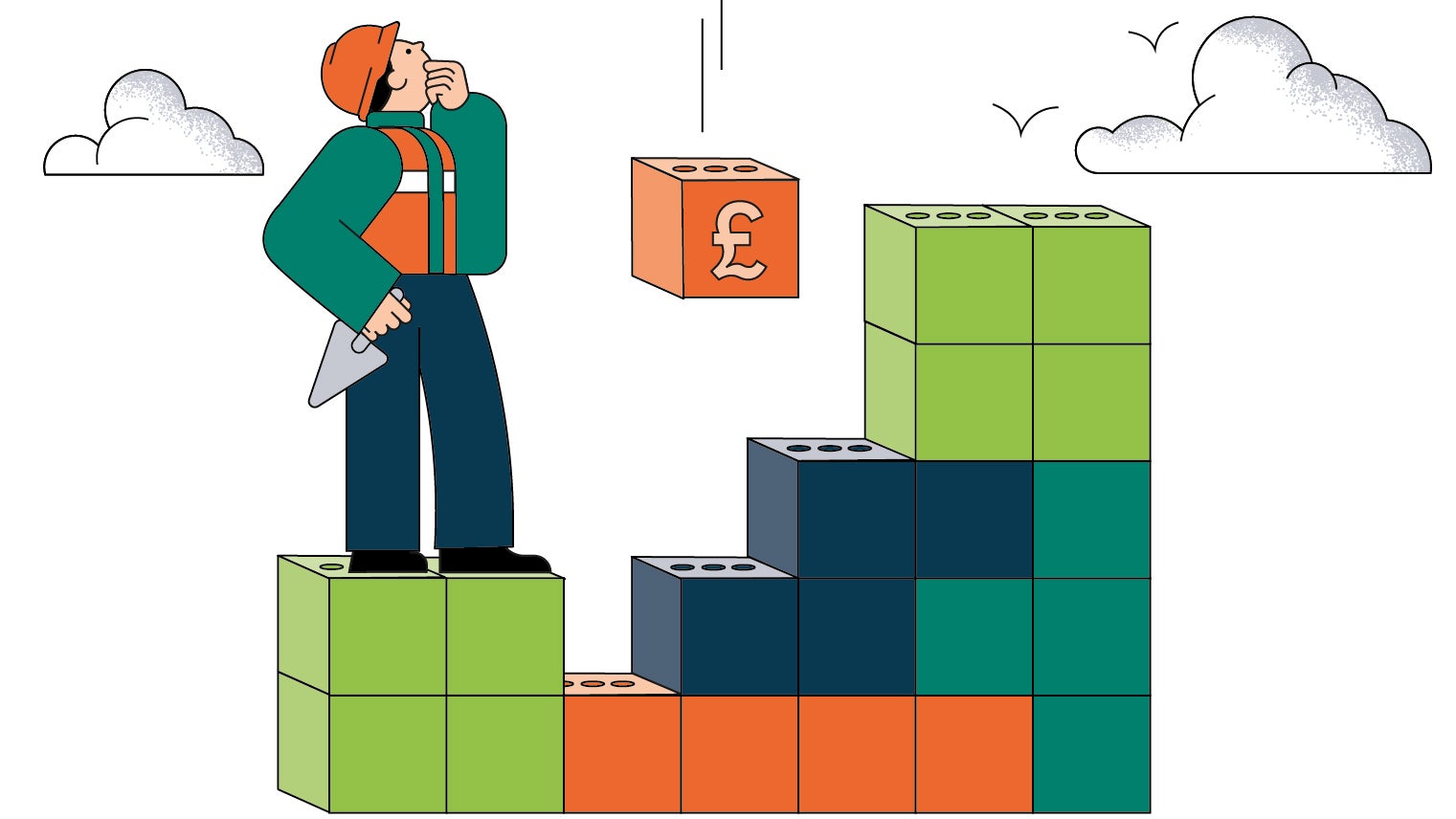
The construction industry has experienced a troubled recovery from the pandemic. Trade tariffs, congested logistics routes, labour shortages, and even climate change are hindering recovery in the construction sector. But the most obvious legacies of lockdown are the shortages of construction materials and unprecedented price hikes.
“The volatility in construction material prices experienced this year is unprecedented,” said Henry D’Esposito, JLL Research Manager, Construction in the executive summary to the firm’s Construction Outlook 2021 report.
“The increases in lumber and steel prices are by far the largest recorded through available government data back to 1949. For other commodities the records are somewhat more recent: aluminum prices have not increased this fast since 1995, plastic since 1976, copper since 2010. The inauspicious distinction this year is that all those records are being broken at the same time. Average material prices for a commercial project increased an astounding 23% in the 12 months prior to August 2021,” said D’Esposito.