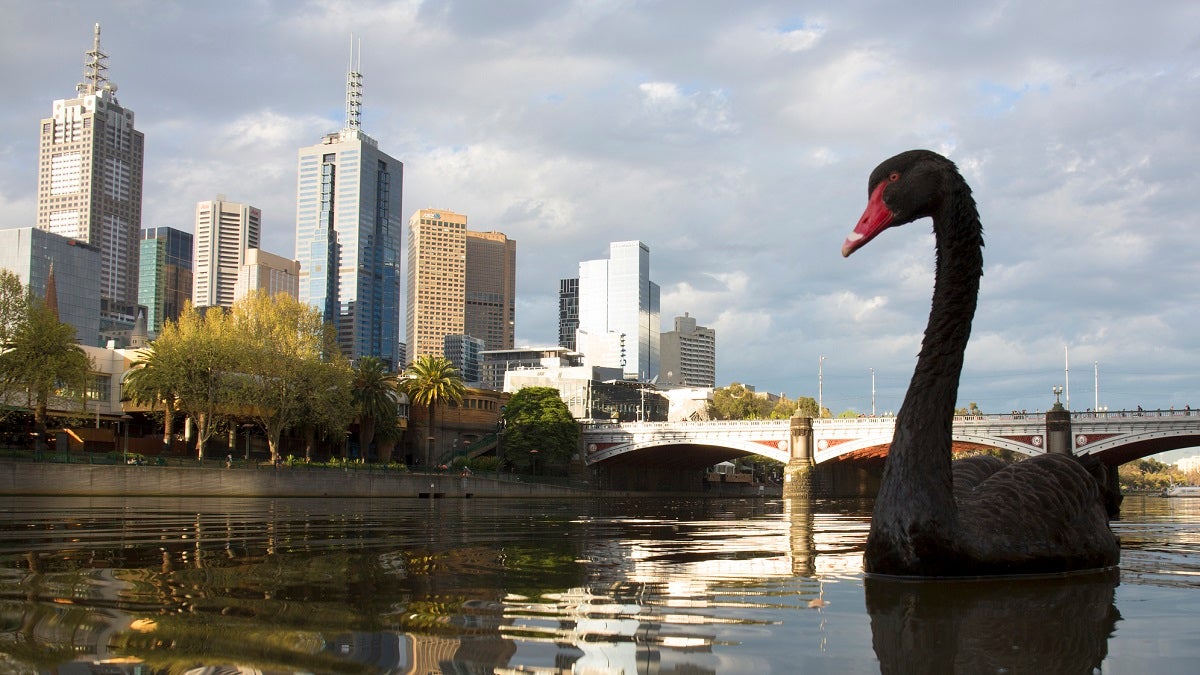
Global supply chains have been tested to their limit over the past 18 months, beset by problems ranging from the Suez Canal blockage and a huge logjam in China’s ports to the UK’s so-called pingdemic and the implementation of new customs rules in the EU.
As standalone events, each has had the potential to disrupt an interdependent system where even the shortest of delays can leave businesses facing millions of pounds in extra costs and lost revenues. Their arrival in such quick succession has amplified the disruption, which has hampered the efforts of linked economies to recover from the Covid crisis. And there is no end yet in sight.
Richard Parkinson, port director of Solent Gateway, one of the UK’s fastest-growing ports, does not believe that this seismic episode has highlighted inherent weaknesses in the system. He argues that global supply chains have become “remarkably robust, efficient and agile”, thanks mainly to advances in digital technology.
“What we saw at the back end of 2020 was that perfect storm of Covid-19, meaning a reduction in the number of shipments; Brexit stockpiling; and the Christmas surge,” Parkinson says. “Everything happened at once and the supply chain couldn’t get enough stuff in or get containers back out to the Far East and India. The whole system clogged up.”
He continues: “I don’t think there’s an endemic problem in the global supply chain, but of course there are black-swan events. They have happened and they will happen again. The most important thing is that the logistics providers gather the right data and analyse it to determine how key risks can be mitigated in the future.”
Restoring parity and price to pre-pandemic norms
One big headache that Parkinson does foresee is that, as demand increases again, there may not be sufficient capacity in the system to respond quickly enough. He notes that container prices have rocketed because there are far fewer ships at sea. With many operators having cut jobs during the Covid crisis, he fears that there will be little incentive for them to risk returning to pre-pandemic resourcing levels, especially as some may be making similar, or even greater, revenues with less inventory.
Parkinson hopes that the three dominant shipping alliances will act to rebalance the situation, but adds that they may need to be challenged to do so by a similarly powerful global coalition of interests.
The air-freight industry is in a similar bind with respect to restoring lost capacity. Throughout the pandemic it has been constrained by the huge reduction in the number of passenger flights, which would usually carry parcels and packets in their holds.
The most important thing is that the logistics providers gather the right data and analyse it to determine how key risks can be mitigated in the future
Simon Batt, CEO of Asendia UK, which carries goods from several fashion etailers to consumers worldwide, says his firm had to charter passenger aircraft to manage the disruption, putting packages on the seats that should have been occupied by holidaymakers and business travellers.
He adds that the shortage of lorry drivers in the UK has been a more recent problem for the business. This has made handling the workload created by the spike in online consumerism during the Covid lockdowns even more of a challenge.
Agreeing with Parkinson that their industry has been enduring the perfect storm, Batt says: “While I don’t think that supply chains are cracking, an enormous amount of pressure has fallen on people, networks and resources over the past couple of years.”
Batt also questions whether it was right to introduce so many regulatory changes in the UK and EU over such a short period.
“Governments and other authorities clearly do a great deal of work to negotiate treaties and write legal documents. What they don’t do enough is actually talk to the people who’ll have to live with their decisions thereafter,” he says. “Writing a treaty is one thing, but in the supply chain it is the logisticians who must pick it up and run with it. It’s therefore important that the authorities get more industry bodies and representative companies involved in how things are done.”
World trade must anticipate more uncertainty
Jens Roehrich, professor of supply-chain innovation at the University Bath School of Management, sees these recent events as simply the latest in a long list of disruptions for those with the task of managing global supply chains, “no matter how sophisticated their systems and risk-planning processes are”.
He cites examples such as the Eyjafjallajökull volcano eruption in Iceland in 2010 and the pirate attacks off the Somalian coast that were regular occurrences between 2005 and 2013.
“While disruptions to supply chains are never easy to deal with, these trying times require, more than ever, a combined approach among buyers, suppliers and governments, so that we can cope with disruptions. The situation could maybe even stimulate more innovative ways of working,” Roehrich says.
Joanna Konings, senior economist for international trade at Dutch banking group ING, believes that, while the litany of recent disruptions is extraordinarily long and varied, it highlights some of the ways in which global trade is changing. For instance, “trade barriers between countries have been going up, often in much less visible ways than tariff increases”.
She thinks that the sector should have learnt from its experiences during the pandemic that “a reshoring response [the reversal of offshoring] won’t save us. Countries and companies may well decide that they need to use a more diverse range of suppliers and markets, and to stockpile certain goods. But building inventories in response to the uncertainty is simply piling more pressure on the system.”
Konings concludes with a stark assessment. “The way that costs are mounting on different fronts, from trade barriers to the rising price of shipping”, she says, “is a threat to business as usual.”
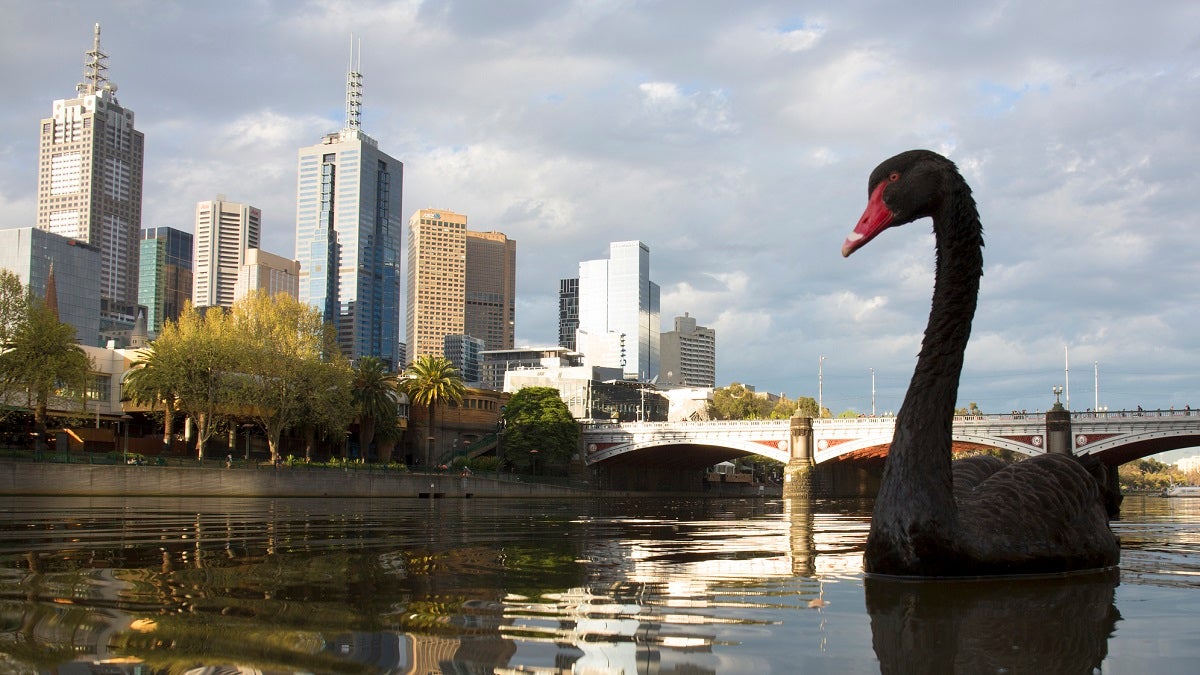
Global supply chains have been tested to their limit over the past 18 months, beset by problems ranging from the Suez Canal blockage and a huge logjam in China’s ports to the UK’s so-called pingdemic and the implementation of new customs rules in the EU.
As standalone events, each has had the potential to disrupt an interdependent system where even the shortest of delays can leave businesses facing millions of pounds in extra costs and lost revenues. Their arrival in such quick succession has amplified the disruption, which has hampered the efforts of linked economies to recover from the Covid crisis. And there is no end yet in sight.
Richard Parkinson, port director of Solent Gateway, one of the UK’s fastest-growing ports, does not believe that this seismic episode has highlighted inherent weaknesses in the system. He argues that global supply chains have become “remarkably robust, efficient and agile”, thanks mainly to advances in digital technology.