Over the last few years, manufacturing companies have greatly improved the efficiency of their operations through the use of automation. This has enabled them to control variables such as temperature, pressure and chemical compositions as well as manage the performance of an operation.
However, companies have noticed that driving efficiency in one area has a knock-on effect on others. Improving efficiency, for instance, has often involved pushing assets and plant equipment to their limit. This impacts safety so real-time control has been used to improve this too. In addition, driving equipment hard can have a detrimental effect on its reliability so this has also been drawn into the expanding remit of real-time control.
Now a new factor is being improved by real-time control, alongside efficiency, safety and reliability. It might be a newcomer, but it’s the most important aspect of any business.
“For 100 years or so industry has been ignoring the fact that profitability rather than efficiency is really at the heart of the manufacturing or production process,” says Dr Peter Martin, vice president and Edison fellow at Schneider Electric, where this new chapter in process control is being written.
“We’re discovering that now, with the latest developments in technology and in control theory, we’re able to apply control beyond just efficiency, safety and reliability, but to profitability as well. We call it Smart Control.”
The speed at which industry is operating is accelerating rapidly, Dr Martin points out, and he cites electricity as an example.
“Some 20 years ago, you’d negotiate an agreement with your electricity supplier to fix the price for, say, a year in advance. Today, with open power grids, the price might change every five to twenty minutes. The cost of other inputs such as natural gas and raw materials can vary just as quickly,” he says. “This variation is equally evident at the consumer end. Thanks to Google and Amazon, the price of a product can change between morning and evening.”
Traditional enterprise resource planning (ERP) systems tend to focus on closing the books once a month. However, as prices change every few minutes, the monthly snapshot that managers see doesn’t give them the information they need to make the right decisions.
Dr Martin and his team have discussed this problem with more than 1,000 executives. “We realised that by using sensors in a plant we could model real-time accounting at each cost and value point in the process, and these measurements would allow us to provide profitability control, pulled together with efficiency, safety and reliability,” he explains.
Operational profitability can be measured in real time as key variables change faster than monthly and this information can be used to control profitability in a manufacturing operation.
So how does Smart Control improve profitability in practical terms? Dr Martin gives the example of a mineral processing plant, producing copper and bronze from base materials. Typically, in this linear process, ore is crushed and then ground to a sand-like consistency before a concentrator separates the metals from the ore. A smelter evaporates the water to leave the metals that will then be refined.
“Here you have ore and electricity entering the crushing circuit, and ground materials coming out. Three factors affect profitability – energy and material costs at the time consumed, and the value of the final product at the time it is produced,” he says. “You need to calculate these three variables and put them into the control system. The traditional control algorithm will, say, open a valve or manage the speed.
“But with real-time accounting, an algorithm will calculate the production value at each stage for each particular time period and put that value into a historian for storage and future analysis. As a result, you have a day-long list of values at every point where cost is incurred.”
Managers can check these costs and work out how to improve profitability in a way that is considerably more sophisticated and more accurate, working as it does, on a second-by-second basis, rather than traditional monthly accounting methods that just use the average cost factor. This real-time accounting information can be used to empower the workforce to make better real-time decisions to drive the greatest operational profitability.
According to Dr Martin, a group of about 50 companies are already benefiting from this new Schneider Electric technology and that number is growing rapidly. Using the latest technology, such as EcoStruxureTM Profit Advisor, implementation is faster than ever.
“We’ve started to deliver this new process control as a service using a big data analytics tool,” he says. “Instead of a couple of months to do a full analysis and implementation, we can do it in a week. We can also extrapolate backwards, using historical data to look at when profitability was good and not so good. With this we can help our clients to replicate the circumstances that delivered the best profitability.”
A benefit of using Smart Control to improve profitability is that it can be implemented bottom up rather than top down, as is the case with most ERP systems. “We say to clients ‘pick a small section and try it on that first’,” says Dr Martin. He argues that rather than just jumping on the latest technological bandwagon, this new approach to controlling critical business variables answers the question “should we?” rather than just “could we?” In other words, it’s about practical benefits.
The whole concept of industrial automation systems design will go through a major transformation over the next five years, he predicts. “We’re a conservative industry and so the items that we’re selling today will still work in 20 years’ time, but there’ll be more of a focus on asset performance. Each and every asset will act as its own autonomous system. After all, if we can make autonomous cars, we can make autonomous compressors and reactors,” says Dr Martin.
“More connectivity and computing power, smarter, connected products, like those compressors, will be able to control, monitor and secure themselves. The data and information the assets provide will enable the industrial workforce to extend that better, automatic real-time control to every industrial asset, all the way up the enterprise value chain. That is the epitome of Smart Control and it will enable manufacturing companies to move from trying to manage their business month by month to controlling it in real time.
“This will enable manufacturing companies to develop from managing their business month by month to controlling it in real time and ultimately turn their industrial automation investment into a profit engine.
For more information please visit www.schneider-electric.com
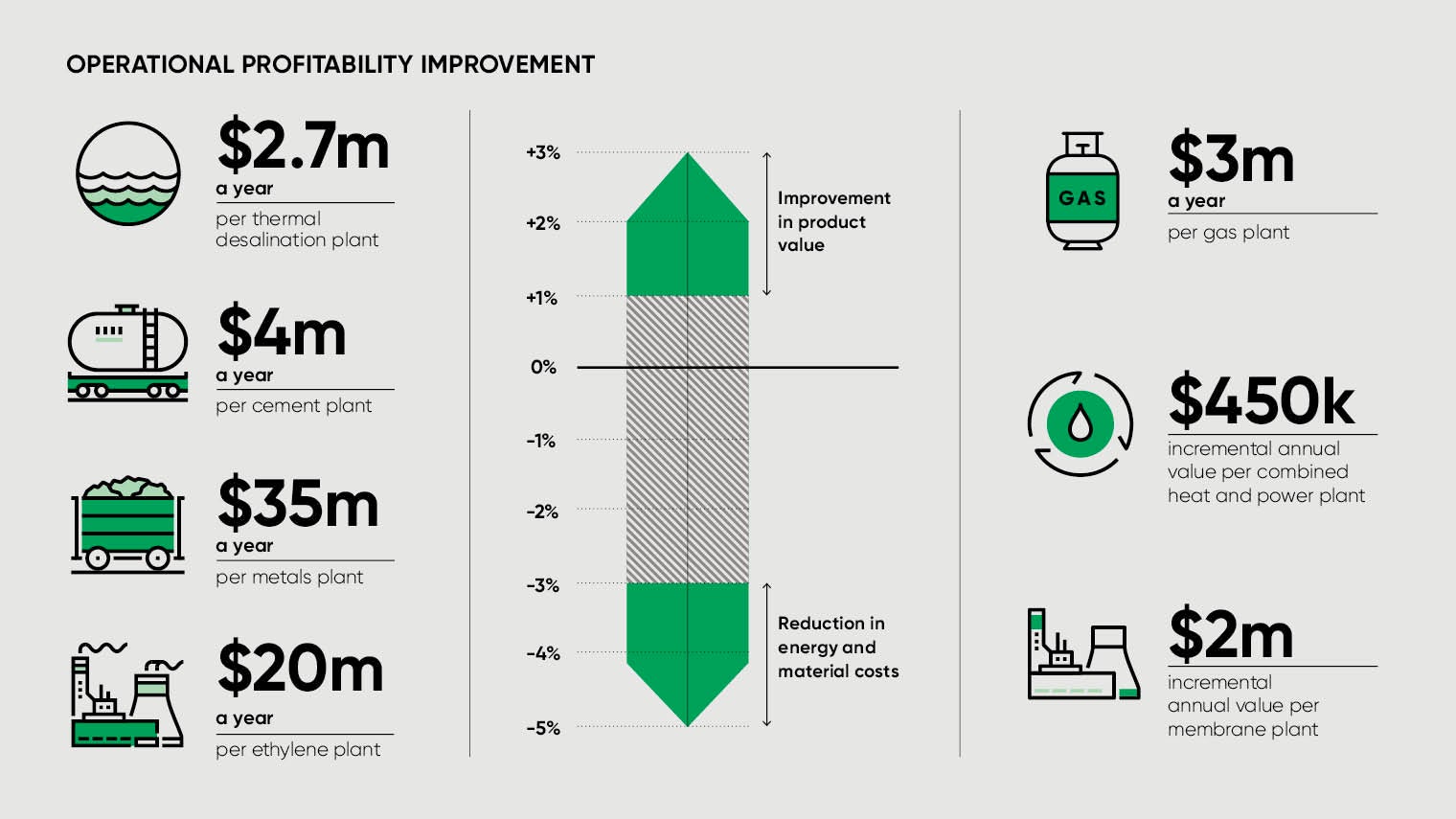