Solutions aimed at digitalising production are not new, but next-generation automation tools present an array of new possibilities for food processing businesses.
“If you think about automation on a broad scale, many exciting technologies are available for the food and beverage industry to use,” says Ulrik Lund Jakobsen, head of food applications at GEA, one of the largest suppliers of food processing technology.
“From growing concerns around food safety and quality to increasing energy costs and environmental considerations, automation plays a key role in addressing these issues.”
Introducing elements of automation to manufacturing processes not only unlocks substantial cost-savings, but food safety is also more closely kept in check, by ensuring the production of goods is observed at every step of its journey to the customer.
The future of food and beverage production will see robotics and automated factories take hold in the sector, fundamentally improving security, sustainability and speed.
“Food safety and quality verification are key,” says Mr Jakobsen. “If the focus is on the health and nutrition of a product, we need to be sure that nothing went wrong in the process. For example, if an item is overcooked, vitamins may be lost; an automated system can instantly flag this and remove the product from the line.”
Consumers are the real winners when it comes to modern food processing as they now have access to deeper insights about where their products come from. The use of sensors in the supply chain provides end-to-end traceability for producers and, in the process, enables regulatory requirements to be better met.
As the topic of food fraud becomes increasingly relevant, detailed data around food creation and the supply chain will bolster consumer trust in the authenticity and legitimacy of the foods they purchase.
GEA believes that looking at the entire value and supply chain is not only a question of responsibility, but also gives producers a way to take more control over their businesses. The primary aim of GEA digitalisation projects in the last few years has been to afford producers maximum flexibility along the supply chain, while simultaneously reducing their level of tied-up capital.
For example, GEA uses an IT-based brewery environment capable of connecting production technology with the storage, delivery and order management system. This integrative approach begins with the supermarket behaviour of consumers, which is the starting point for organising the whole supply chain. This data is vital for business processes, including raw material yield, plant availability and efficiency, while supporting preventive maintenance.
“Can we do this without automation? Yes, we could, but then we would miss out on the scale and cost benefits,” says Mr Jakobsen. Ultimately, automation is about harmonising interfaces and standardising the exchange of data between automation and engineering systems, which leads to shorter time to market, greater flexibility, improved product quality and efficiency.
This shift in production will require employees to take part in advanced training so they can adapt quickly and get accustomed to working with cutting-edge machinery.
Digital twin technology, where a digital replica of a physical asset is created, enables companies to train operators in a simulated factory or on a piece of new equipment before they begin working in the real plant or new system. The advantages are many, including risk minimisation, early detection and elimination of errors, shorter commissioning times, as well as more time to train operating personnel safely on a test platform before production begins.
At GEA, exciting new automation-based solutions are keeping costs down and enhancing food quality.
“The cost of leveraging preventative or remote maintenance based on feedback from an automated system is far less than compared to a plant that’s standing idle because of a missing spare part; these are two very different situations. The fact is that in an automated plant it’s much easier to do proactive management and predict the lifespan of machinery,” says Mr Jakobsen.
“For us it’s not just selling a plant, it’s about helping our customers be successful. The whole service concept is what matters.”
For more information please visit gea.com
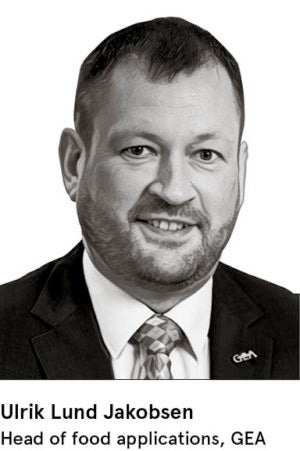