Power to the people: how operations leaders can engage the front line
Providing healthcare and other vital public services, front-line workers form the backbone of society. Heeding their concerns and acting upon them is key to ensuring their safety in the workplace
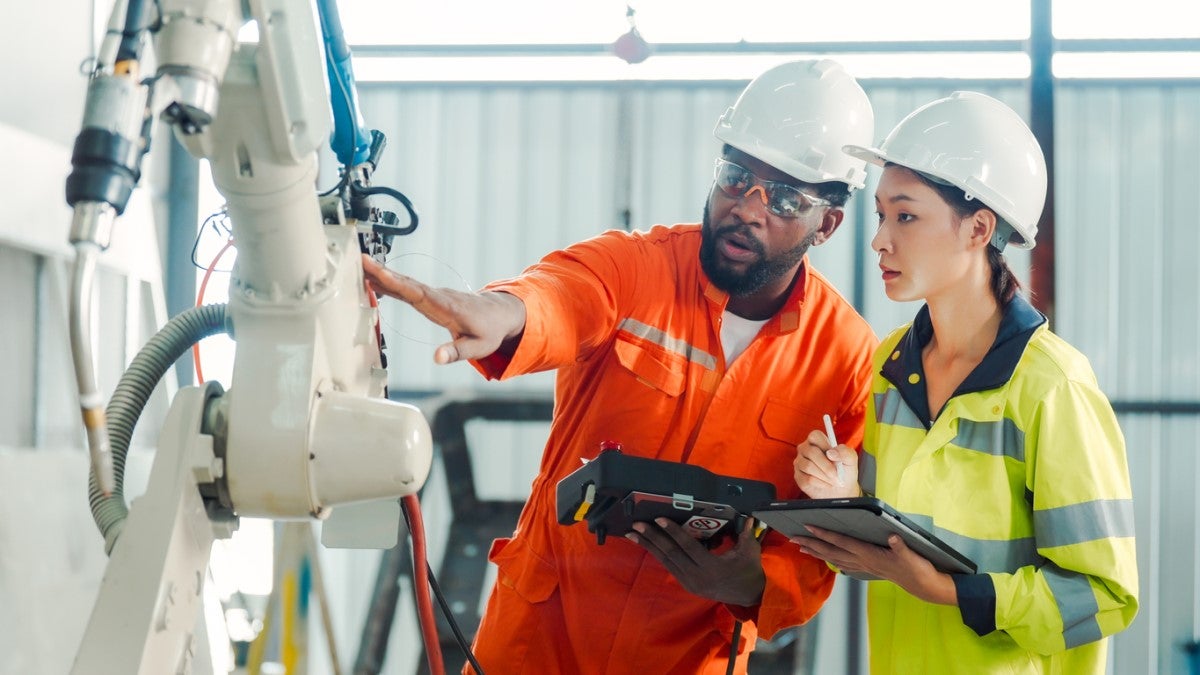
While the pandemic was a tough time for everyone, it imposed particularly high demands on the millions of front-line workers who propped up the economy in the depths of the crisis, providing key services, building critical infrastructure and delivering essential supplies.
This has prompted a notable shift in public attitudes towards front-line workers, who have gained widespread recognition for keeping the country running and, in some cases, risking their lives in the process. Their call to be better rewarded for their contribution to society has led to lengthy industrial disputes in several sectors.
In a survey of front-line workers published by McKinsey & Co last year, 78% of respondents identified pay progression as an advancement need, while 75% and 73% respectively cited learning opportunities and supportive management as important to them. The research also revealed a significant gap between what they want and what their employers think they need. There’s an opportunity here for operations leaders to better understand their staff and create a healthier and safer working environment in which they can thrive and develop their careers.
Give front-line employees a voice
“Front-line teams are the eyes and ears of our business. They’re the ones who provide excellent service,” says Joe Saisi, MD of the London operations of facilities management firm Churchill. “Not actively engaging with them would be a mistake.”
Churchill has established a “challenger board” comprising 12 employees drawn from the various sectors and regions covered by the business. This body has enough clout to influence the senior leadership team’s decision-making.
“This gives a voice to front-line employees who deal with clients that use our services daily,” Saisi explains. “Members of the challenger board work together to share best practices, suggest potential innovations and offer solutions to problems. The board of directors then provides feedback on their input. When any of their recommended changes are enacted, they feel they’re being heard.”
Saul Resnick is CEO for the UK and Ireland at DHL Supply Chain, although he sees himself as more of a chief cultural officer working to align everyone with the idea that no job at the firm is more important than any other.
“They need to believe that they are part of one business,” he says. “As part of this, we engage with issues as soon as they are raised, focusing on employees’ health and safety. People in senior roles will often walk the floor, talk to colleagues and set up regular feedback sessions.”
The company also operates a channel through which any employee in DHL Supply Chain’s UK business can ask Resnick questions or give him their thoughts about the business. Every contributor will receive a response.
For operational leaders wondering how best to communicate with front-line staff, there’s no one-size-fits-all approach, but research by Gallup suggests that employees who receive weekly feedback from the management are almost four times more likely to be engaged at work than those who don’t receive it regularly. Gallup’s managing partner for EMEA, Jeremie Brecheisen, recommends holding at least “one meaningful conversation per week”.
Create a culture that promotes safety
Technology can be a great enabler in creating a continuous feedback loop. Employers can use online surveys, social networks and chatbots to learn what front-line staff are thinking, including any health and safety worries they may have. Using software to document their responses can help managers to refer critical concerns quickly up the chain of command.
Nonetheless, Brecheisen warns that these IT tools shouldn’t be treated as a panacea. “If you don’t hold your operations managers and leaders accountable for their behaviour, no amount of technology will create the necessary culture change,” he says.
Leaders must be willing to learn continuously from the experiences of front-line staff and the insights they can offer. There will always be room for improvement, notes Brecheisen, who adds that it’s important that they don’t allow preconceptions to influence their approach to this task.
“If you want to understand how people feel, you need to go in listening – and then listen more,” he argues. “Involving your people leads to ownership. Ownership leads to engagement. Engagement leads to positive change.”
Saisi agrees. He believes that any leader who “actively listens to the concerns of front-line staff and acts on them as a priority will make employees feel respected. This will empower them to keep delivering the best quality of work.”
Such an approach should create a virtuous circle. The idea is that highly engaged employees are less likely to take unnecessary risks or create health and safety problems at work – and that safer and healthier working environments are better for employee engagement.
Four ways in which AI is making high-risk work safer
Artificial intelligence has advanced in leaps and bounds in recent years. Here’s how the technology is being used to improve conditions for people with particularly hazardous occupations
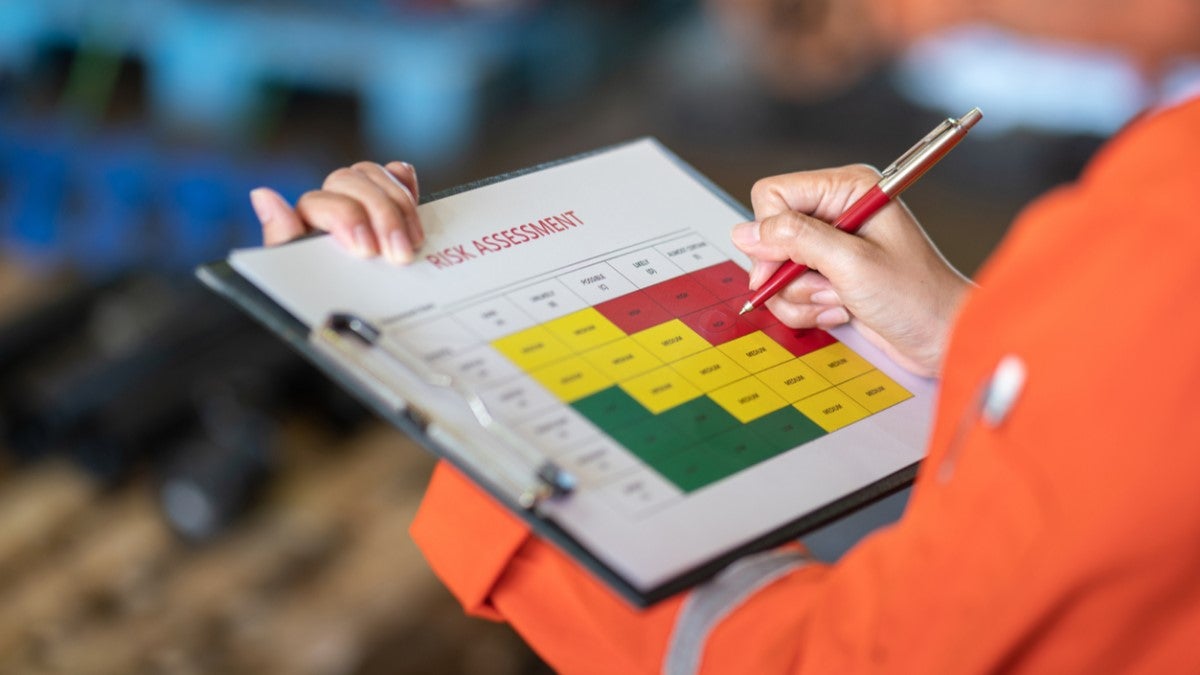
In high-risk workplaces such as construction sites, offshore wind farms and nuclear power stations, effective health and safety management is paramount, as any lapse could cost lives. With the power to detect problems before they cause accidents and help front-line workers to avoid unnecessarily hazardous situations, AI has huge potential to reduce the level of operational risk in these hostile environments. Here are some of the technology’s more striking applications in the danger zone.
As well as reducing downtime and maximising efficiency in production, AI-powered maintenance can reduce the risk of workers operating faulty – and therefore more hazardous – equipment.
“Organisations are using AI’s ability to look back and find patterns in data and then look forward and create predictions for how various scenarios could play out,” says Simon Geale, executive vice-president of procurement at supply chain consultancy Proxima.
The data it collects can be used to predict likely machinery failures before they occur. This enables the manufacturer to perform proactive maintenance work on the hardware identified, minimising the need for unplanned repairs to broken equipment, which tend to be lengthier, costlier and more disruptive.
Geale, who describes such practices as “putting AI safety rails around the human workforce”, reports that it’s become possible to “train a machine to support or perform a hazardous task, taking the human away from that task and making them the operator rather than the performer. Take this up a level and we’re seeing where the human moves from operator to orchestrator.”
More workers died in construction than in any other industry between April 2022 and March 2023, according to the Health and Safety Executive. A key part of what makes it such a hazardous occupation is the high number of moving objects on a typical building site.
Machine learning, a branch of AI, is being used in risk assessments, analysing data from cameras, internet-connected devices and sensors placed around sites. These feeds are monitored to ensure that machinery is working properly, people are using it correctly and the appropriate protective equipment is being worn.
“This can flag a dangerous situation far more quickly than a human could, triggering an alarm to warn employees and, where required, shutting off machinery before an accident happens,” says Martin Kahl, MD of digital transformation consultancy Monstarlab Germany.
“Imagine a workplace where AI serves as the environment, health and safety lead’s third eye, continuously monitoring CCTV footage for trends in unsafe behaviour,” says Dan Hobbs, co-founder and CEO of Protex AI, a provider of hi-tech safety systems. “Beyond serving as a safety net, it can become a rich source of knowledge. It can process vast quantities of data efficiently, converting it into valuable insights. This enables EHS teams to make more informed choices about resource allocation, safety protocols and training. It’s like having a trusted adviser guiding you through the complexities of risk management.”
The inherently risky nature of maritime work means that an offshore wind turbine is likely to be inspected by a human just a few times a year and only then if the weather and sea conditions are safe enough. On top of this, a manual inspection requires the turbine to be deactivated.
The Aquada-Go project is developing AI-backed drone technology to examine turbine blades while they’re still spinning. The drones will be equipped with thermal cameras capable of detecting subsurface damage that would be invisible to the naked eye.
The project is being led by RWE Renewables Denmark, whose CEO is Nils Leseberg. He says that the system’s advanced data analysis capabilities will give wind farm operators a better picture of their assets’ health and enable them to optimise their maintenance work schedules.
The automation of inspections not only promises to reduce turbine downtime. It should also mitigate the risk to human safety by reducing the need for technicians to make site visits.
When a nuclear reactor comes to the end of its life, workers are still generally required on site to operate equipment during the decommissioning process. But this approach is not ideal on both safety and cost grounds, so an alternative solution is necessary.
“Decommissioning requires people to make many entries into contaminated areas wearing air-fed suits, which requires a significant investment. It’s been estimated that each suited entry costs £10,000,” explains Professor Barry Lennox, co-director of the University of Manchester’s Centre for Robotics and AI. “There are also areas that are simply unsafe for humans because of the radiological hazard.”
He is part of a team that has developed Lyra, a robot that’s been used to inspect ventilation ducts at the redundant nuclear laboratories at Dounreay and pinpoint radioactive materials. According to Lennox, the project is an example of how AI-powered robots can be used in conditions unsuitable for human workers. Another one is Spot, a four-legged robot that’s being used to inspect and clean areas of the old Sellafield power station that remain highly radioactive.
How do front-line employees feel about their workplaces?
Where are the pressure points and how much confidence do workers have in management?
Improvement engine in action: how a salmon packing factory optimised operations
Organisational software is helping businesses to digitise their processes, create a continuous loop of feedback from the factory floor to the C-suite and optimise their operations
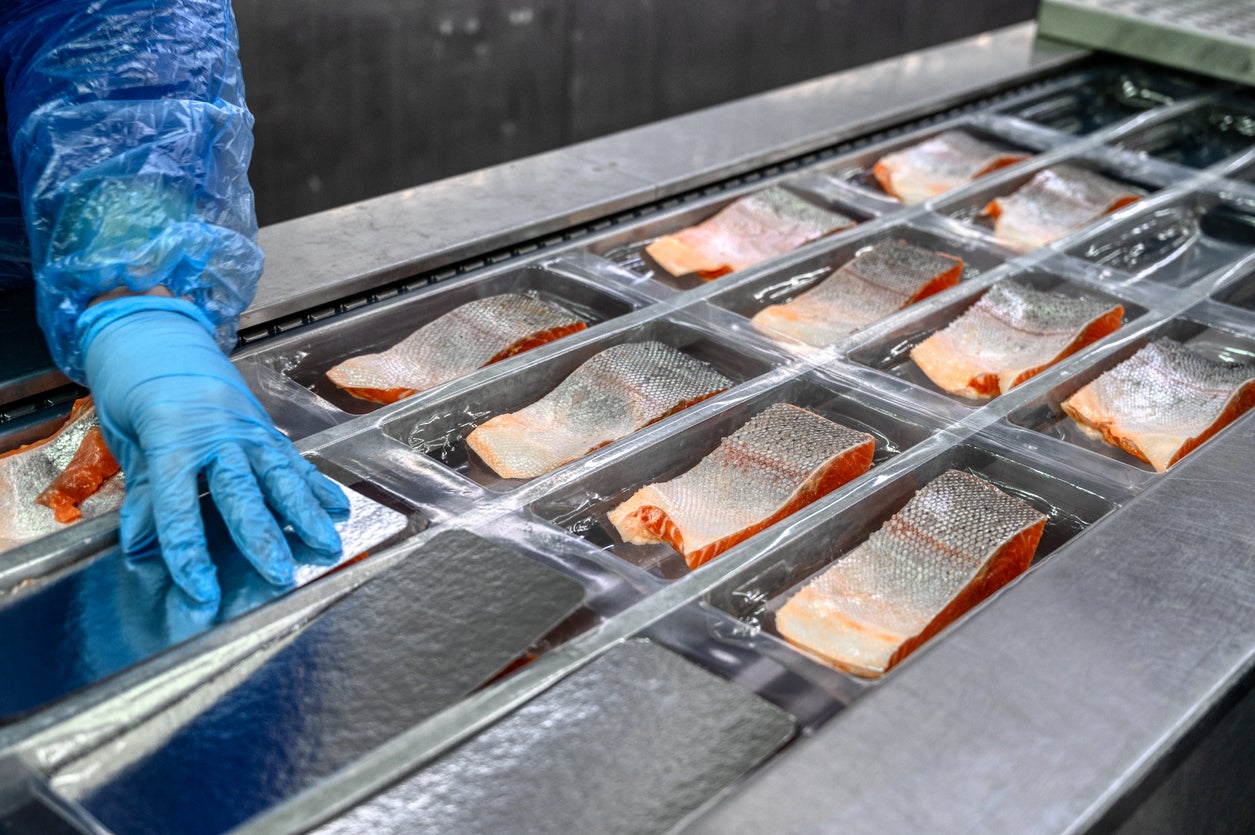
Rosyth is a humble town in Scotland, three miles south of the city of Dunfermline. It’s home to around 13,000 people and is most famous for a sprawling dockyard that was once a key naval base during World War One. It’s also the home of Forth Road Bridge, an iconic landmark that used to be the longest suspension bridge outside of the United States.
Some towns age and stagnate with the passage of time, but green shoots of change are emerging in Rosyth. Nestled beside the bridge is a £30m state-of-the-art food factory. MOWI Salmon is the largest salmon packing site in the UK and employs 800 full-time and part-time staff from around the world who produce 250,000 fresh salmon products for supermarkets every week.
On the factory floor, the smallest of details matter. Each salmon product must undergo a multitude of checks as part of a stringent technical and health and safety audit to satisfy the highest of standards demanded by internal leaders, industry regulations and retailers. The result is a premium product that’s delivered to supermarkets across the UK.
But for David Bett, technical manager at MOWI, that wasn’t enough. “We used to use paperwork and handwritten notes for our entire auditing process,” he says. “We would archive the paperwork at the end of every month and then that was taken to off-site storage after three or four months. It was quite a rigid process and a lot of manual work for staff. It also made it difficult and costly to locate and retrieve documents from physical files.”
Bett downloaded a seven-day free trial of the SafetyCulture business operations platform. Its software and support teams give businesses the knowledge, software tools and confidence to set higher standards of performance to continuously improve their operations. At first, Bett’s sole aim was to digitise the auditing process. “I was a novice with the app,” says Bett. “All I wanted to do was create electronic versions of the paperwork we used. We were successful with that but I didn’t realise how much more we could do.”
It was a front-line employee who had the lightbulb moment. Anna Giusti, who had moved to Rosyth from Venezuela a few years earlier, was working on the factory floor when the app was first rolled out and saw an opportunity to do more. “Initially, I felt we could customise the audit templates to reflect the order in which we carried out checks on the factory floor,” she says. “Then I felt we could optimise the forms to add in new checks to spot common mistakes that we, as operators, tended to make.”
Giusti’s insight sparked a change in communication between MOWI’s leadership and its operational staff in the factory. “Previously we were more top down in terms of our communication,” Bett explains. “The leadership team would tell staff the changes we were making but Anna made us realise that we could use the software to get real time feedback from workers in different departments and create a continuous loop of improvement.”
MOWI’s leadership also spotted an opportunity to further exploit the potential of the SafetyCulture platform and empowered Giusti to use the software to drive the business forward. Giusti was promoted to a technical role as a Quality Infrastructure Analyst and set about modifying templates and adding feedback functions for factory workers to add their comments to each step of the audit.
She then tapped into a data analysis function that processed the data and enabled the business to gain valuable insights, such as the frequency of checks, the types of incidents that typically occurred, how often they arose and where and when they happened. This data was collated into dashboards to create weekly, monthly and annual reports, along with feedback from workers, to accelerate and optimise operational change.
The app has now been used across other areas of the business. A daily technical shift report is completed by quality controllers using an iPad to detail key incidents and how they were handled. The app’s exporter tool exports the information to an Excel spreadsheet, which is reviewed by quality managers, who discuss whether the right corrective action was taken and how their decision-making could be improved. This information is delivered back to controllers on a weekly basis, while a KPI report is sent to senior leaders.
Logistics and health and safety processes have also been optimised. All deliveries to the factory are photographed and recorded using the app as part of an inspection check to optimise traceability. Foreign body reports investigate how unwanted objects may have entered the production line to optimise health and safety and avoid accidents.
Outside of the factory, SafetyCulture boot camps are helping MOWI to learn from the experiences of other businesses. “The support offered by SafetyCulture is second to none,” says Bett. “We can contact them using an online chat function and we have an account manager as well so we get individual solutions crafted to the needs of the business.”
For Giusti, the app has provided a behavioural model for the business to replicate. “The app itself is an improvement engine in action,” she says. “It’s built from the feedback of its users.” In Rosyth, everchanging lines of code in a software app are helping this business, its employees and the town to learn, grow and flourish.
The cutting edge of occupational health and safety
Businesses in a range of industries are investing in virtual reality, robotic suits and even barbers trained in mental healthcare to protect their employees’ wellbeing
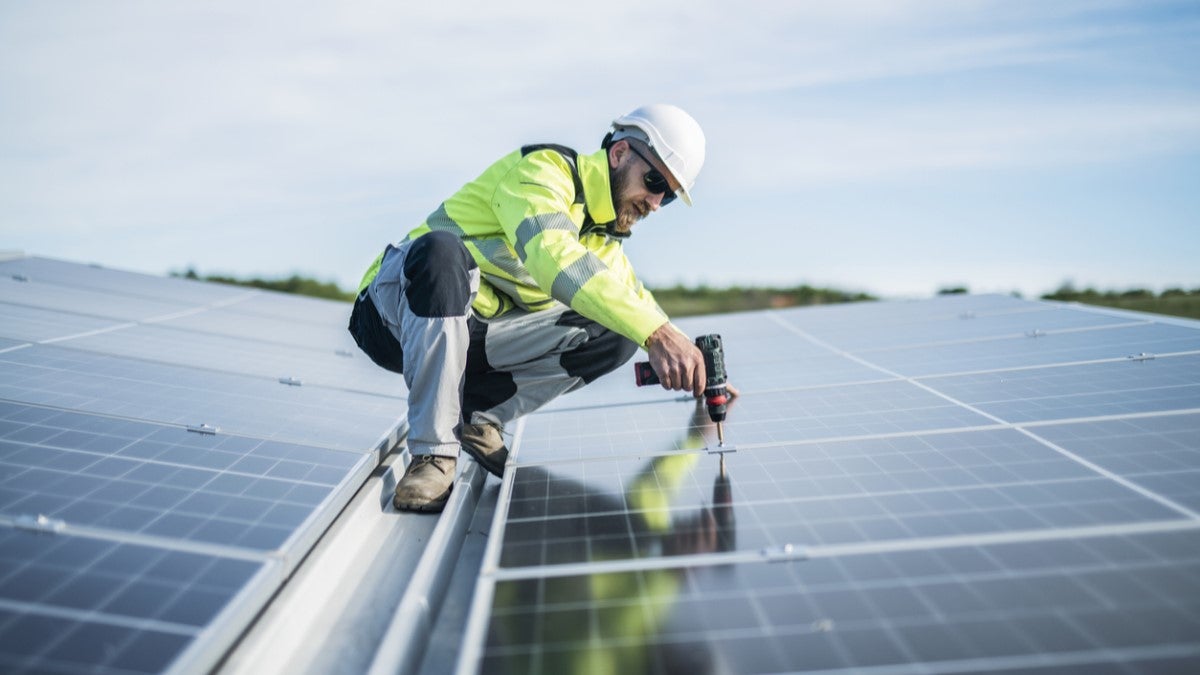
In the late 1800s, London’s East End was home to Bryant and May’s match factory. From 6.30am to 7pm each day, 3,000 teenage workers, mostly girls, inhaled toxic fumes from the white phosphorus used in the production process. Many developed phosphorus necrosis, commonly known as phossy jaw. This was a painful, disfiguring and often fatal disease whose symptoms started with toothache and progressed to gum abscesses, the death of bone tissue around the mouth and brain damage. Without timely surgery to excise the dead tissue, patients would typically die of organ failure.
British workplaces are far less dangerous than they were 150 years ago, of course, but people in certain occupations still face significant risks. Research published by the Health and Safety Executive (HSE) in July revealed that 135 people died in work-related incidents in Great Britain in the 12 months to March 2023, for instance. The most common causes of death were strikes by vehicles or other moving objects (killing 49) and falls from height (40).
Smart accident prevention
Construction company Willmott Dixon has adopted virtual reality (VR) to target one of the industry’s biggest killers.
The firm’s regional head of safety, Alistair Donaghey, explains: “We use actors to create a virtual simulation of working at, and falling from, height, so as not to put workers at risk during training. The trainees, who wear VR headsets, can identify the main hazards before, during and after the fall.”
In a bid to reduce the number of injuries occurring in its warehouses, logistics firm Europa Worldwide has been investing heavily in a different technology.
“In 2021 we spent £11m on an automated picking solution,” reports its COO, Dionne Redpath. “This has reduced the amount of manual handling and physical labour our staff have to do.”
Wearable tech is another tool being used by businesses to reduce the risk of injury at work. In preparation for Black Friday last year, for instance, Currys invested more than £250,000 in robotic exoskeleton suits to help workers at its distribution centre reduce the strain on their joints while handling heavy goods.
Wearables have even helped workers in the hospitality industry to avoid injury. Research in that sector by actuary Perr&Knight in 2021 concluded that a device monitoring the wearer’s posture and providing instant feedback if it deemed it unsafe reduced the frequency of injuries by up to 60%.
Protecting mental health
Workplace health and safety isn’t just about preventing physical injuries, of course. Mental ill-health is an increasing concern for employers, particularly those in the building trade. Data from the Office for National Statistics covering England and Wales shows that workers in that sector are nearly four times more likely than people in other occupations to take their own lives. In 2021, for instance, 507 construction workers died by suicide.
The Lighthouse Club is a charity working to ensure the wellbeing of people in the construction industry. Among other facilities, it provides a 24/7 helpline for workers to discuss their problems. It cites job insecurity and loneliness as two factors contributing to builders’ poor mental health.
Karen Brookes, chief people officer at construction firm Sir Robert McAlpine, reports that concerns about money have also become a big issue for those in the industry.
“Over the past 18 months, financial worries caused by the cost-of-living crisis have been one of the main problems,” she says. “In some instances, we’ve provided interest-free loans and one-off hardship payments for workers who’ve been sending money back to their families in Ukraine.”
The company is also using more creative solutions. Barbers trained in mental healthcare have been invited on its building sites to offer workers both a trim and a trained ear if they want to discuss any problems, while 150 mental health first aiders work across the organisation.
Brooks says that acting workshops have become another way for the company to address mental ill-health in its workforce.
She explains: “We work with a company called Acting Out Productions. Its performers come in and run a workshop where they act out a typical conversation in which an employee being questioned by their manager about a decline in performance struggles to communicate their mental health problems. We then invite the attendees to suggest better ways for managers to speak to employees and invite them to open up.”
Psychologically safe environments
Business leaders have a key role to play in developing psychological security – that is, a culture in which employees feel secure enough to offer constructive criticism without fear of repercussions.
Andrew McNeill, the co-founder and director of LXLeaders, has spent 25 years helping employers create psychologically safe workplaces.
“I get businesses to create ceremonies,” he says. “This is an official process that confirms how people are going to work together and the behaviour they will and won’t accept. I ask teams to sign statement cards – these could concern kindness, conduct or performance. They act as a contract and give staff at all levels permission to call out behaviour that doesn’t match what’s been stated.”
Businesses are increasingly prioritising the physical and psychological safety of their employees to create workplaces that feel like an extension of a happy home.
Redpath says that Europa Worldwide wants its employees to “enjoy being at work, so we ensure that our warehouses are pristine, with temperature control so that it’s warm in winter and cool in summer. We have amazing canteen facilities and provide healthy menus for staff with different themes every week.”
Maintaining a sense of camaraderie has been key at Willmott Dixon, according to Donaghey. “We want to create a family environment on every project,” he says. “I’ve been in this business for 50 years – and that’s what has kept me in it.”