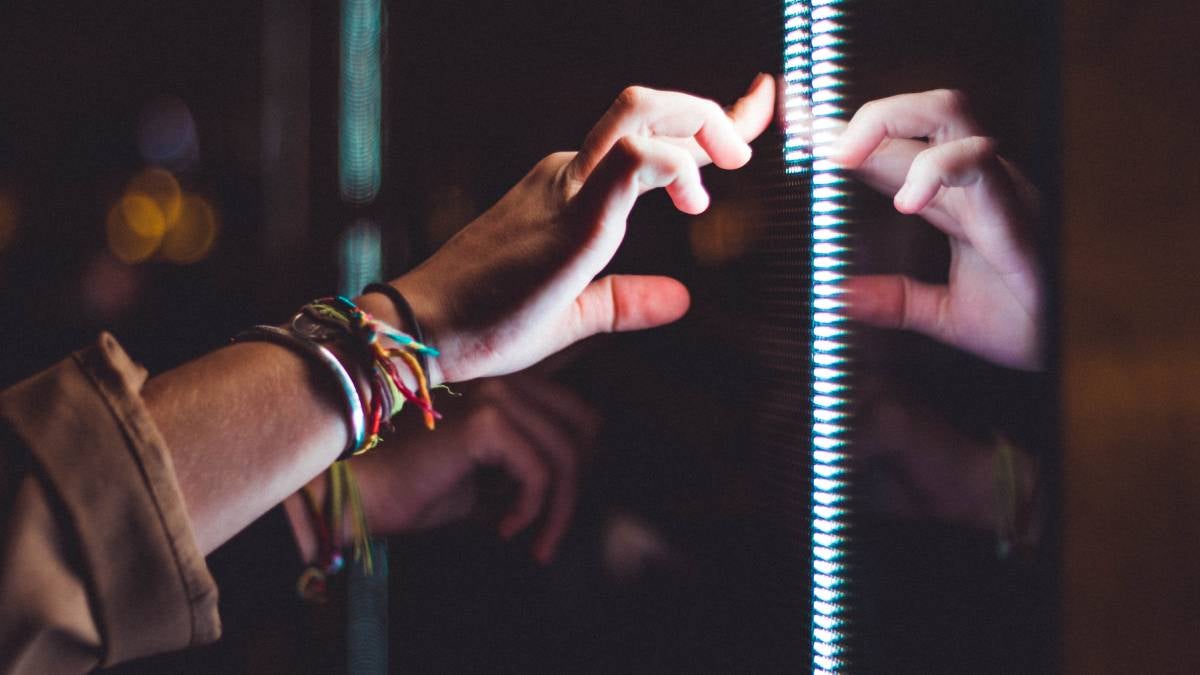
In the wake of the pandemic, manufacturing sector margins have never been thinner. Relying on lean inventory management and at times just a skeleton staff, with workers off sick suffering Covid, many manufacturers have found their operational output has been reduced, causing supply chain bottlenecks.
Lean inventory management, also known as just-in-time (JIT) manufacturing, is designed to reduce flow times and minimise delays to work processes. Components, parts and materials are ordered as close to when they are needed as possible. The thinking behind this is that stockpiling inventory for long periods can be unpredictable. Not only are there holding costs, but the quality of a component, part or material could deteriorate over time.
According to Sam Roscoe, senior lecturer in operations management at the University of Sussex, the advantage of JIT is that components, parts and raw materials are “pulled through the supply chain based on demand signals and finished goods are made only when customers need them”.
However, the downside to a lean approach to inventory management is manufacturers have no buffer if there’s an imbalance between supply and demand.
As Roscoe points out, JIT is suitable for localised supply chains or international supply chains where there are open borders. But in the case of the semiconductor industry, the majority of the world’s chips are produced in Taiwan.
When demand for electronics surged at the start of the pandemic, chip foundries decided to prioritise them over cars as the margins were higher, which led to automakers scrambling for a limited supply. Due to the automotive industry’s reliance on JIT, the majority didn’t have a buffer of components to meet the demand for new vehicles.
Industry 4.0 is an enabling layer for data management. The data collected isn’t always perfect, or complete, but that’s fine. As they utilise the data better, companies’ understanding improves, resulting in faster decision-making
Although the chips were down for most, one automaker that managed better than others was Toyota. In the third quarter of last year, for the first time the Japanese automaker sold more cars in America than US auto giant General Motors.
How did Toyota achieve this? Partly by building a stockpile of chips. Although a pioneer of JIT and waste management, Toyota had seen its supply chain devastated by the Fukushima earthquake and tsunami in 2011 and so set about identifying the weak points in its supply chain. The company asked its semiconductor suppliers to have several months worth of chips to hand at any one time, so it could procure them in the event of future major supply chain constraints.
Connecting the dots
Analytics dashboards, powered by the internet of things (IoT), can help manufacturers to get a better grasp on inventory management. Enterprise resource planning (ERP) software can monitor and capture data on components or raw materials as they move along the supply chain. Manufacturers can then decide whether they need to break from the JIT model and build up a stockpile, as Toyota did, to navigate potential shortages in the future.
Even with ERP software in place, however, manufacturers can sometimes struggle to identify the weak points in supply chains. A major reason for this is because the software hasn’t been connected and fully synchronised with other applications and data sources. Not integrating the ERP software with other systems, data is underutilised and the technology isn’t leveraged to its full potential.
Failing to connect the dots in manufacturing operations means not all supply chain risks and potential bottlenecks are identified and tracked early enough. This can result in unexpected delays and overstocking, which can ultimately result in higher carrying costs and waste.
Data-sharing and collaboration ideal
Waste management is critical in the fast-moving consumer goods or FMCG sector, especially when it comes to perishable food manufacturing. Perishable goods depend on JIT manufacturing because they can’t sit in storage for long periods.
ERP software can help food producers to keep supply chains flowing. But more than that it enables improved operational efficiency and reduced waste and carbon footprint.
Food producers are continuously advancing their net-zero goals by lowering the amount of energy and water used. “They’re increasingly finding ways to see through the data fog to understand how they manufacture the same volume of product with fewer resources and adapt lines that are not working to full capacity,” says Dean Griffin, senior services solution manager at a packaging giant Tetra Pak.
With food producers looking to shift more products using fewer materials, the packaging industry also has a role to play, optimising packaging designs so they can be manufactured using much less energy and water. This can lower the amount of scope 3 emissions – the result of activities from assets not owned or controlled by the reporting organisation – absorbed downstream by end-users.
In an ideal world, all food producers and packaging manufacturers would be sharing data on energy and water consumption. Stakeholders in the food supply chain would also be monitoring and tracking the movement of raw materials and products in real time through packaging and distribution. This would reduce carbon footprint as well as enhance food quality and safety, lowering the risk of supply chain contamination.
“Industry 4.0 is an enabling layer for data management. The data collected isn’t always perfect, or complete, but that’s fine. As they utilise the data better, companies’ understanding improves, resulting in faster decision-making,” says Griffin.
While there is legislation in place designed to prevent incorrect labelling on packaging, and food fraud and contamination, the UK Food Standards Agency has called for a “data trust framework” to promote information exchange. This technology would allow commercially sensitive data to be shared between stakeholders.
“By arming a workforce with more data, they can make more informed decisions, work more productively as a team and collaborate on solutions that address issues like food security and safety,” Griffin adds.
The benefit of manufacturers sharing data is it enables stronger supply chain collaborations. But if an upstream stakeholder hasn’t embraced IoT technology, and isn’t utilising data from different sources and systems to manage risks, then this can weaken supply chains. The more stakeholders there are in a supply chain and the further downstream they are, the further away they are from knowing the true extent of supply chain bottlenecks upstream.
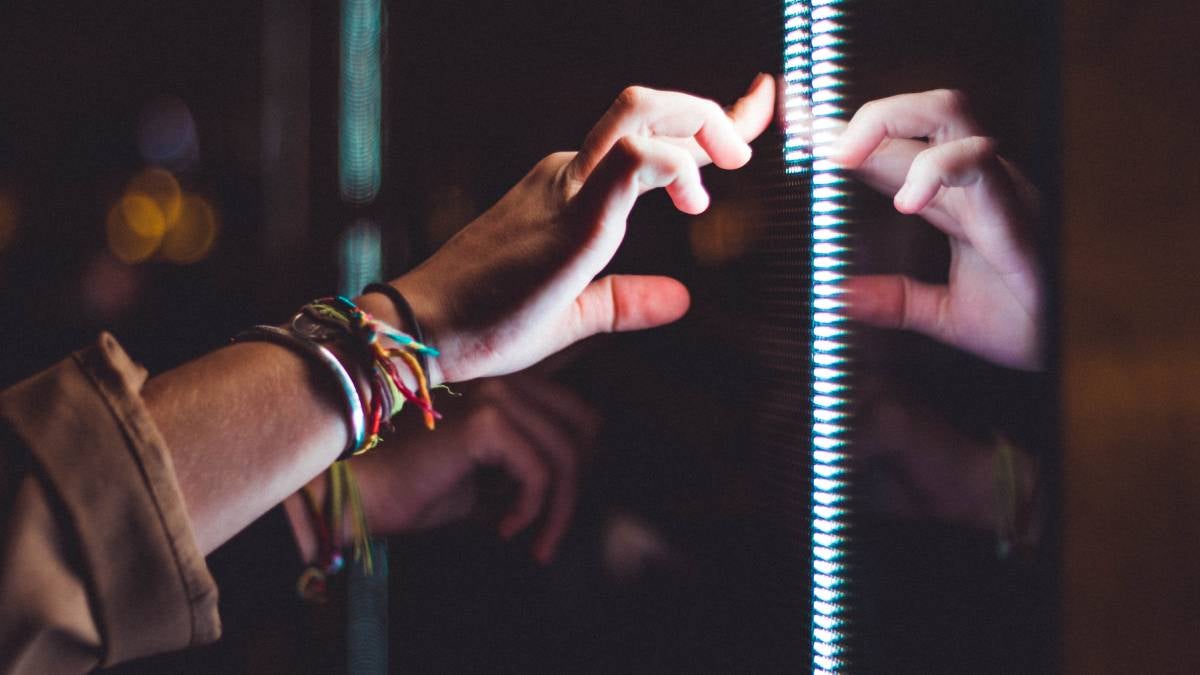
In the wake of the pandemic, manufacturing sector margins have never been thinner. Relying on lean inventory management and at times just a skeleton staff, with workers off sick suffering Covid, many manufacturers have found their operational output has been reduced, causing supply chain bottlenecks.
Lean inventory management, also known as just-in-time (JIT) manufacturing, is designed to reduce flow times and minimise delays to work processes. Components, parts and materials are ordered as close to when they are needed as possible. The thinking behind this is that stockpiling inventory for long periods can be unpredictable. Not only are there holding costs, but the quality of a component, part or material could deteriorate over time.
According to Sam Roscoe, senior lecturer in operations management at the University of Sussex, the advantage of JIT is that components, parts and raw materials are “pulled through the supply chain based on demand signals and finished goods are made only when customers need them”.