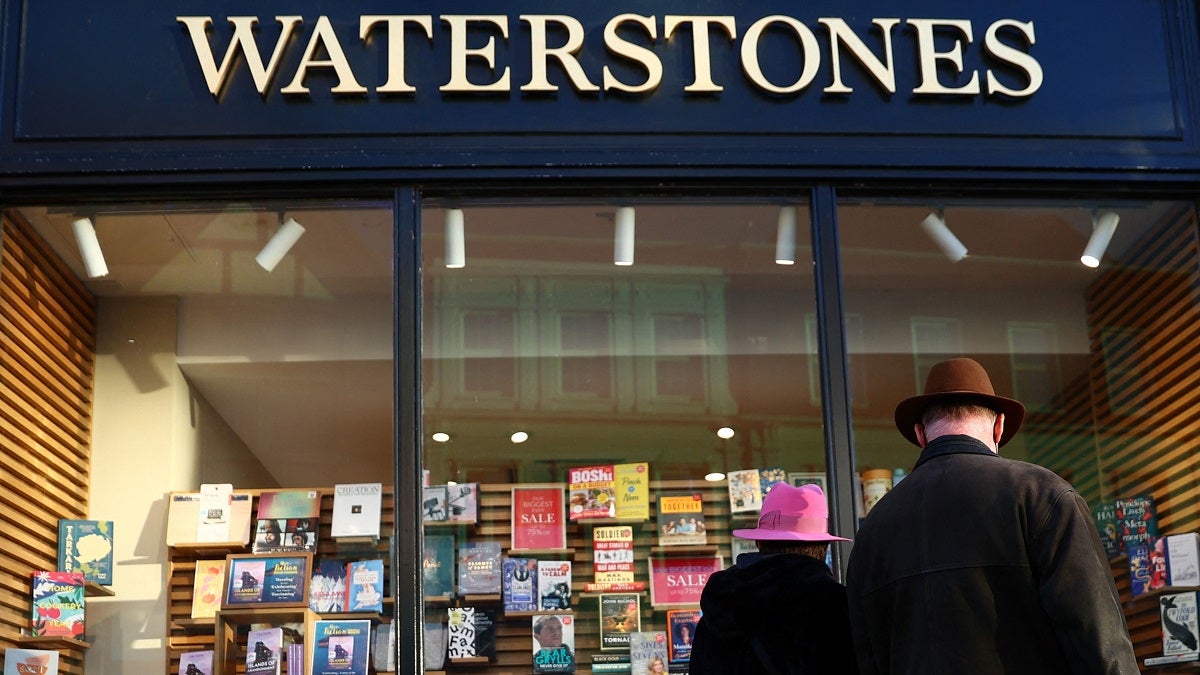
Delivering a digital migration at the best of times is a trying experience. But when you’re upgrading from an outmoded technology, it can be even more challenging.
That was the issue facing book retailer Waterstones in the summer, when the company’s 300 stores shifted to a new system to handle its stock from centralised warehouses. It found that the migration was less than smooth, contributing to stock shortages, while frustrated frontline employees were unable to locate books or order new ones for customers who wanted the latest bestsellers.
Waterstones did not respond to a request to comment for this story. However, the company is believed to have come a cropper when it upgraded to a new system that manages stock distribution run by Blue Yonder, an AI-driven supply chain platform. Waterstones believes that it can plough through its backlog of orders to get back on an even keel by September, when it can take advantage of what it calls a “much more sophisticated program”.
A spokesperson for Blue Yonder said the company had been brought in to help Waterstones manage stock distribution from its warehouse. “While complexities arose, all parties involved in the implementation are working diligently and cooperatively to resolve the issue as quickly as possible,” the spokesperson said.
Learning lessons
For many businesses, Waterstones’ tale is a cautionary one – and a situation they’ll be thankful they avoided. “Technology is going to become a mainstay and a larger piece of the logistics supply chain function of any business now,” says Neil Jordan, vice president of logistics and supply chains at Proxima. “But with that comes greater risk.”
Waterstones isn’t the only retailer to face challenges and hiccups in efforts to improve its IT stock management systems. In 2019, online clothing retailer Asos decided to update its warehouse tech stack. Algorithms designed to tell staff when to pick items for orders misfired, meaning those orders had to be cancelled when they were incomplete. In all, the Asos imbroglio cost the company £25 million in disruption costs and lost sales across its European markets, with France and Germany the worst affected.
The situation came as a shock to Asos, just as it has to Waterstones. It also happened at roughly the same time of year – an indication that both companies chose to try to do their warehouse digital upgrades at a time when business was comparatively quiet.
It is a failure if you’ve pursued a migration so wholeheartedly that there’s no way to reverse a change without losing all your systems
The fact that the failure came as a surprise to both businesses is itself surprising: IT upgrades are difficult. “Upgrading a warehouse to become a smart warehouse has many rewards, as well as unique challenges – namely, issues related to digital migration,” says Heico Sandee, chief technology officer and founder at Smart Robotics, a warehouse robotics system.
No one really knows what’s gone wrong at Waterstones and the secrets of Asos’s botched warehouse upgrade are kept within the company. Still, there are some clues on common pitfalls that can be avoided. “Maintaining the unchanged content, context and structure of the data is absolutely critical,” says Sandee. “Smart warehouses rely on accuracy in data to maintain a smooth flow in operations. If disturbed, huge capital losses are certain to follow.”
Practice makes perfect
Jordan believes that Waterstones’ issue likely stemmed from something simple. “If something slightly goes wrong in the processes, and the mapping hasn’t been done, it can have a significant impact,” he says. “There will be something that has just been missed.” He advises that practice makes perfect – and preparation is key.
When advising businesses, Jordan suggests that they look at robustly testing environments that will be used for real in warehouses to ensure that every scenario that could occur in a normal weekday has been trialled, and the system shown to handle it. “Companies I know who have done this very well take a lot of time and invest a lot of money in this,” he says. They’ll often run the two systems in parallel – old and new – to ensure that there are no hiccups that can occur in the new one that could take the whole system offline. The old system is left running as a failsafe to fall back on in the event of a catastrophic error.
Sandee also thinks this is important. “A migration with all content, users, and integrations moving in mass to the new system is never a good idea,” he says. Best practices involve planning for a gradual, hybrid or rolling migration, where small parts of the entire process and system are moved onto the new software bit by bit to ensure nothing goes wrong.
Backups are key
The ability to go backwards as well as forwards when implementing a warehouse digital migration is essential, cautions Sandee. “Easing into relocating data is key,” he says. “It doesn’t matter if you’re moving data from one application to another or from hardware to the cloud, warehouse optimisation relies on the safekeeping of the original data sets.”
Not doing so is foolhardy, he says. “If the new system fails, be sure you can fall back on your original system to ensure warehouse processes keep moving forward,” says Sandee. “As long as data can be retrieved, you can roll back without any disruptions.”
It’s not a failure of a migration if you end up being forced to revert to what you had before to iron out issues. But it is a failure if you’ve pursued a migration so wholeheartedly that there’s no way to reverse a change without losing all your systems and the good running of your business.
And be aware: there will be disruptions. “I’ve never seen a system launch where there’s been no issues,” says Jordan. “There will always be issues. It’s the magnitude of the issue that causes the challenges.”
It’s about how companies respond to those problems, and whether they’re able to swiftly solve them, that will make the difference between viable stocking and shelves standing empty – with the resultant effect on the bottom line.
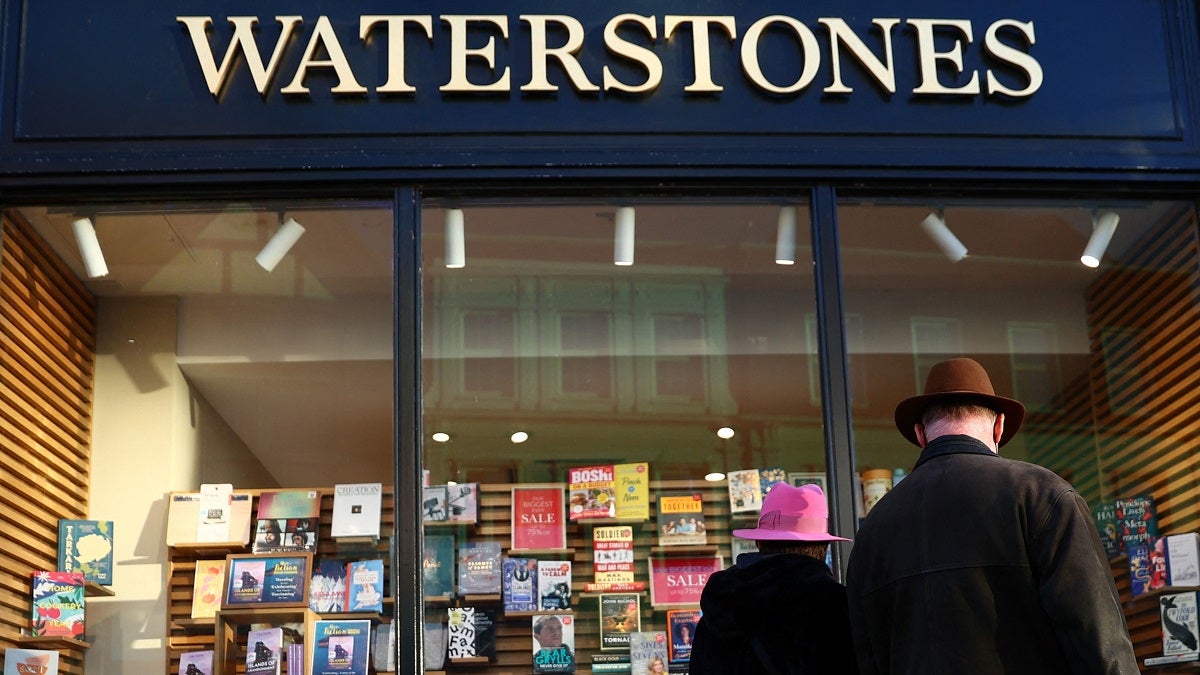
Delivering a digital migration at the best of times is a trying experience. But when you’re upgrading from an outmoded technology, it can be even more challenging.
That was the issue facing book retailer Waterstones in the summer, when the company’s 300 stores shifted to a new system to handle its stock from centralised warehouses. It found that the migration was less than smooth, contributing to stock shortages, while frustrated frontline employees were unable to locate books or order new ones for customers who wanted the latest bestsellers.
Waterstones did not respond to a request to comment for this story. However, the company is believed to have come a cropper when it upgraded to a new system that manages stock distribution run by Blue Yonder, an AI-driven supply chain platform. Waterstones believes that it can plough through its backlog of orders to get back on an even keel by September, when it can take advantage of what it calls a “much more sophisticated program”.