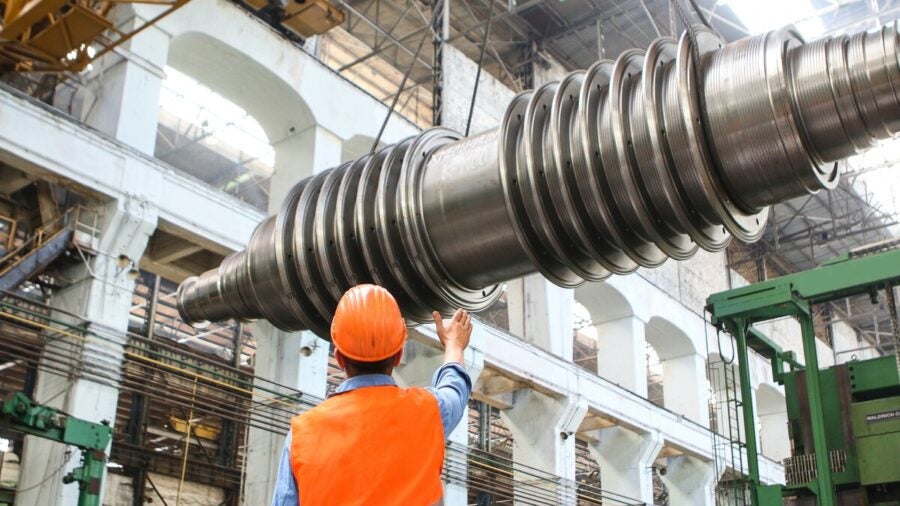
Digital transformation has broad connotations, spanning AI, robotics, big data, IoT and cloud-based technologies. At their core, these initiatives put technology to work to optimise workflows company-wide and grow the business.
But the emergence of new processes, business models, domains and digital cultures no doubt carries different implications across sectors. “Companies know that digital transformation is about innovation with intent,” says Andy Coussins, executive vice president, international sales at Epicor. “It’s not about adopting technology for technology’s sake.” So, how can organisations be sure they’re reaping the full potential of digitisation?
Manufacturing has long been a cornerstone of British industrialisation, and the sector is accelerating towards an increasingly digital future. Valtech research finds that leading manufacturers are growing more zealous about the potential for technology to power innovation, streamline product development and reinforce resilience, with 59% defining their organisation’s digital transformation goals as ambitious, compared to 47% last year.
Digital transformation is about innovation with intent. It’s not about adopting technology for technology’s sake
These lofty aspirations are more likely to be achieved through tailored transformation, says Coussins, advising against an industry-agnostic approach. “Companies need processes, data, and insights specific to their industry, allowing teams to leverage data-driven insights to make informed organisational decisions.” Data provides a solid foundation to pinpoint and tackle unique business challenges.
“Whether a business is looking for an ERP system for the global automotive industry or a system for highly regulated sectors like aerospace and defence, vertically-focused technology puts the right data in the right hands at the right time,” he continues. The challenge of leveraging new data sources that come from digital transformation strategies and translating this information into actionable insights remains.
Businesses can start by breaking down data silos between various applications within and beyond the organisation to create a seamless data supply chain. “When production networks are connected, and not operating as a single node, organisations unlock insights to personalise buying experiences, and deliver innovative new technologies,” says Coussins.
If the tech fits
US supply chain solutions provider Stephen Gould is no stranger to this approach. The company worked with Epicor to automate the entire intracompany process and establish a flexible data fabric that allows business users to act as citizen developers and integrators.
Scaling up digital transformations across supply chain and manufacturing operations and departments can be hard work. Coussins points out: “Working with an industry expert in technology will help you evaluate opportunities for automation to help you future-proof the business.”
Epicor Kinetic was designed with decades of industry expertise to maximise revenues through advanced project and production management – from tracking work in progress in real-time to improving technical data processes.
Hannah Willett, applications engineer at Stephen Gould, explains: “The biggest value of Kinetic lies in the customisability. You can mould the ERP to your business instead of trying to mould your business to the ERP.”
Skills shortages are another fault line in the digital transformation conversation, but innovations needn’t add complexity. “You don’t need a lot of programming experience, meaning another employee who isn’t a developer could maintain our integrations,” says Willett, noting that the company is on track to have all six Stephen Gould subsidiaries and 41 plants on Epicor within three years.
Collaboration and employee buy-in
A large segment of manufacturing is made-to-order, with demands for personalisation on the rise. Cobots (industrial robotics or technology that works alongside employees) are capable of minimising human error and automating repetitive, high-volume tasks. Similarly, the industry is introducing process-aware generative AI agents that can be prompted to accelerate workflows, tying multiple tasks together in the interest of efficiency.
Advances may be exciting. But any digital transformation must bring employees along for the change, particularly in traditional industries and small-to-midsize businesses. Technology is about supporting people, not replacing people, Coussins asserts. On-the-job work instructions, visual cues, and real-time IoT-driven insights ensure workers feel productive and valued, particularly amid ongoing concerns over labour shortages across many economic sectors.
The best results often come when companies combine internal industry expertise with a partner that helps leaders apply technology to augment how teams make decisions. “Innovation is constant,” concludes Coussins. “Collaborate with industry leaders in industries parallel to yours, talk with your broader supply chain ecosystem about what they are using and why, and work with an industry expert in technology will help you evaluate what is right for your business.”
Find out more about transforming business with agile, intelligent, integrated ERP at epicor.com/en/resources/success-stories/manufacturing/stephen-gould/
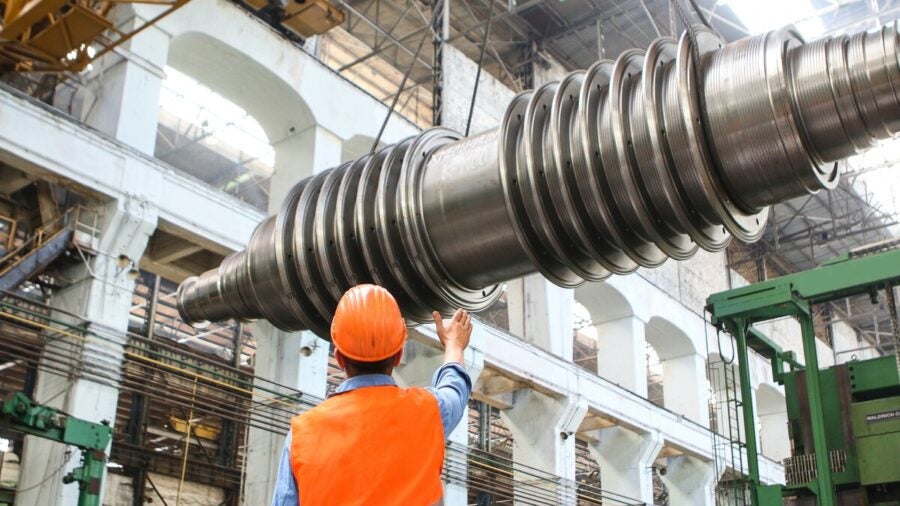
Digital transformation has broad connotations, spanning AI, robotics, big data, IoT and cloud-based technologies. At their core, these initiatives put technology to work to optimise workflows company-wide and grow the business.
But the emergence of new processes, business models, domains and digital cultures no doubt carries different implications across sectors. “Companies know that digital transformation is about innovation with intent,” says Andy Coussins, executive vice president, international sales at Epicor. “It’s not about adopting technology for technology’s sake.” So, how can organisations be sure they’re reaping the full potential of digitisation?
Manufacturing has long been a cornerstone of British industrialisation, and the sector is accelerating towards an increasingly digital future. Valtech research finds that leading manufacturers are growing more zealous about the potential for technology to power innovation, streamline product development and reinforce resilience, with 59% defining their organisation’s digital transformation goals as ambitious, compared to 47% last year.