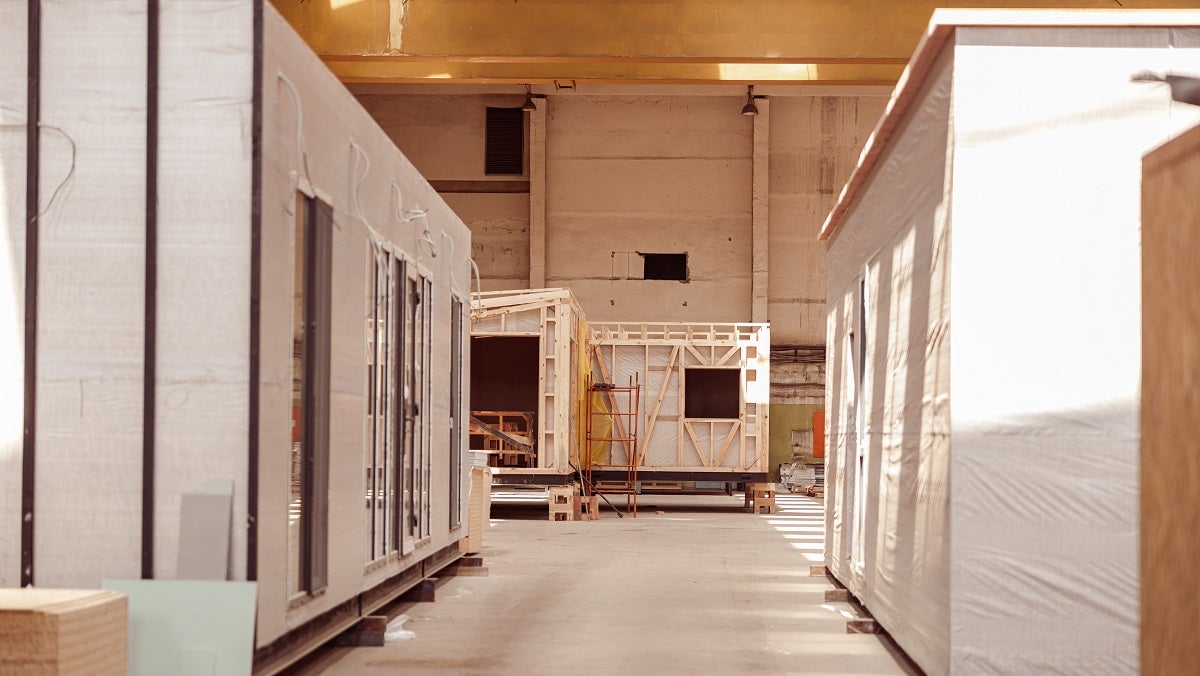
Construction is awash with sustainability targets, and the climate emergency means both regulatory pressures and market expectations are rising like sea levels.
The problems are not new, though. Back in 2013, the UK government published its industrial strategy Construction 2025, which set out clear targets for lower costs (down 33%) and emissions (50%), plus faster delivery (up 50%).
With a focus on productivity and labour issues, the Farmer Review followed in 2016, provocatively entitled Modernise or Die. Among 10 headline recommendations, the report challenged the industry to invest in R&D and innovation to support manufactured technologies, rather than traditional building methods, particularly in the housing sector.
These offsite systems and methods – including modular and volumetric solutions, structural insulated panels, plus design for manufacture and assembly (DfMA) – offer the prospect of building and engineering in factory conditions with greater efficiency and less waste, more quality control and less snagging.
This can make delivery faster, cheaper, safer and greener. So, what’s not to like?
Well, anything that threatens the hegemony of business-as-usual will encounter resistance from the industry old guard. When the palette of design options appeared limited in the early days of MMC, offsite solutions were tagged as ‘boxy’.
Pigeonholed as only fit for budget applications and projects with multiple unit repetitions, MMC became associated with no-frills hotels, student accommodation and prisons. While it might be perfect for schemes seeking economies of scale; it is also much more than that.
The success of Lego lies in its simplicity
Myth-busting is still required. For instance, there is a perception that a standardised approach to building could stunt the creativity of architects when the opposite is true, argues Russell Haworth, CEO of global technology platform NBS:
“Take the example of Lego; its success lies in its simplicity. Yet, within that structured framework, it opens the door for almost infinite creative options – building everything from Hedwig, Harry Potter’s owl, through to the Millennium Falcon, the iconic Star Wars craft.”
Advances in robotics, automation and mass-customisation nowadays mean components can offer almost infinite design choices, with shorter production runs. Versatility is booming, regardless of whether the primary building material is concrete, timber or steel.
The resulting award-winning designs come in all shapes, sizes and sectors.
In education, for instance, there are the timber-clad curves of the £4.4m expansion to Addington SEN School, Reading, designed by HLM Architects and built by Reds10. In housing, the sustainability skills of architects Bryden Wood won acclaim for realising the development potential of a problematic site at Churchwood Gardens, London.
From hotels and healthcare to bathroom pods and bridges, offsite applications are up.
For delivery at speed and scale, especially in housing, though, investment is critical, too.
Despite a challenging start, Legal & General has recently doubled-down, announcing further multi-million-pound investments into its modular housing arm. Housebuilder Weston Group has also sunk £35m into its British Offsite operation, creating more jobs at a new factory alongside its existing facility, in Essex.
Even Ikea is getting in on the act, partnering with Swedish construction giant Skanska on its Scandinavian BoKlok homes concept, which is fighting off the flat-pack association in places like Worthing and Littlehampton, in West Sussex.
This creativity and growth need not come at a cost to quality and efficiency.
Being less labour-intensive, standardisation not only helps drive up quality, but also shortens timeframes, especially when phases of work are undertaken concurrently in factory conditions, with no delays due to inclement weather or skills shortages.
Taking these multiple benefits together, projects utilising MMC can prove faster than traditional builds and require fewer deliveries to site, so minimising neighbourhood impact.
Energy is another area of potential efficiency gain with offsite – in terms of embodied energy, thermal performance, and decarbonisation. Wider factors are in play here, though, explains Simon Richards, Sustainability Director at Sir Robert McAlpine.
“Delivering building elements in a controlled environment allows us to ‘get it right first time’. This means we use fewer materials, emit less carbon and drive efficiencies. The level of quality and performance control will also help us to drive down operational energy emissions – so long as installation and interfaces with other trades are correct.”
Ultimately, many of the barriers to uptake are not architectural or technological, says Adam Sanford, operations lead South East and London, at Southern Construction Framework. The issues are systemic and call for revolution, not evolution, he adds.
“Offsite isn’t just cabins and doesn’t have to cost more. However, traditional construction supply chains aren’t geared up for manufacturing-based solutions – a sea change is required. The dire need to decarbonise the built estate poses challenges unique in scale and scope; it also presents unparalleled opportunities for market disruptors.”
Delivering building elements in a controlled environment allows us to ‘get it right, first time’
Employing lean manufacturing techniques to minimise material consumption and waste is one such opportunity afforded by offsite solutions. This is a major industry concern and a critical sustainability metric, given official statistics that show construction, demolition and excavation generate more than three-fifths (62%) of total UK waste.
Looking beyond mere factory efficiency, the onus is on the building sector to take a proactive stance on waste by designing for deconstruction, concludes James Ellis, Construction Industry Group chair at the Chartered Institute of Marketing. “The future for offsite needs to embrace the circular economy – making sure construction considers disassembly either as complete panels for reuse, or through the layering of systems to allow for disassembly down to their singular parts,” he says.
This is construction reimagined as intelligent closed-loop manufacturing, complete with a product take-back. This is the built environment of today, leveraging digital tools to deliver on sustainability goals, for a net-zero tomorrow. This is MMC.
Small is scalable for rooftop living
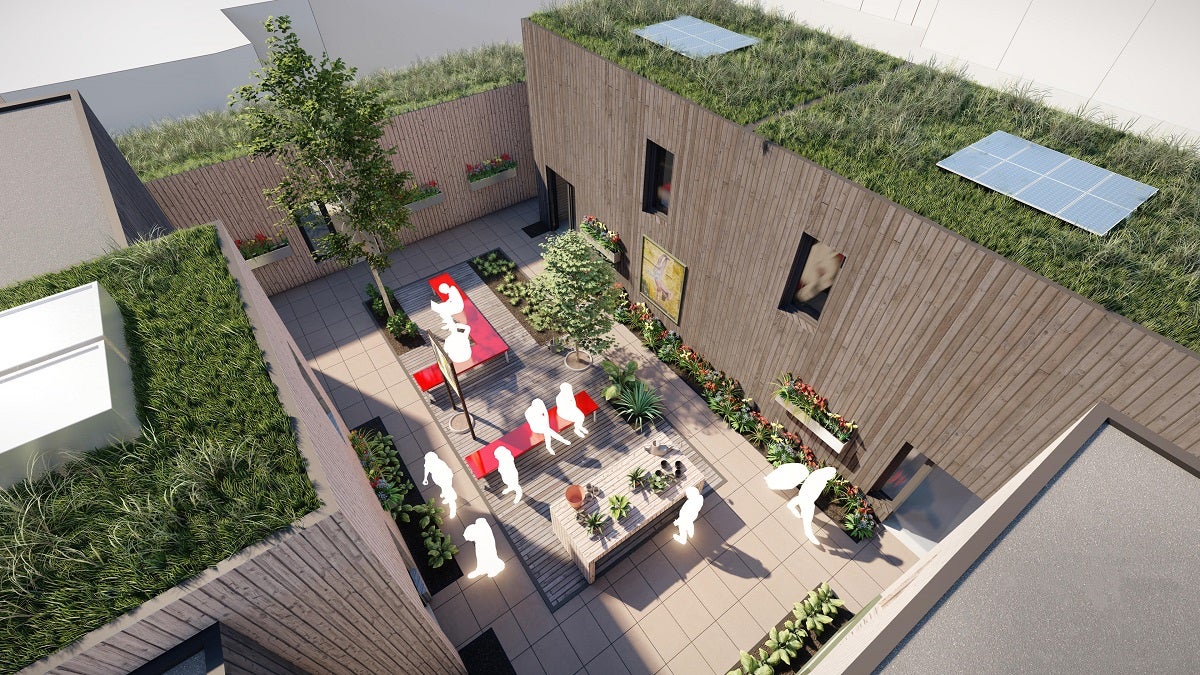
In Bristol, planning approval has just been awarded for an innovative proposal to create 15 new low-carbon, affordable eco homes, utilising modern methods of construction (MMC). But this is not your typical offsite build, as it will be constructed using straw-bale and timber panels up on the roof of the city-centre offices of the client, a charity that works with formerly homeless people.
Complete with food-growing and shared amenity space, the scheme for Emmaus Bristol is being driven by the urgent need to respond to both the housing crisis and climate emergency. The design approach taken to tackle these sustainability concerns is different, though, suggests Craig White, CEO of project delivery partner, Agile Homes:
“Agile goes about it by thinking small and scaling fast, to deliver housing as if people mattered. We work with MMC in a way that respects people, planet, profit and purpose.”
Unlike scenarios involving capital-intensive investment in big factories, Agile’s model of distributed manufacture optimises the making of build-systems for job creation, locally.
Properties must also be constructed using renewable, carbon-capturing materials – in this case, prefabricated panels made of chopped and compacted straw for insulation.
In addition, by unlocking land on a rooftop site, the accommodation can be made affordable for those in housing need, via simple finance options.
The aim is to deliver people-centred solutions that are adaptive to need, performance and market demand. Small, but scalable, the versatility of MMC is what makes this possible.
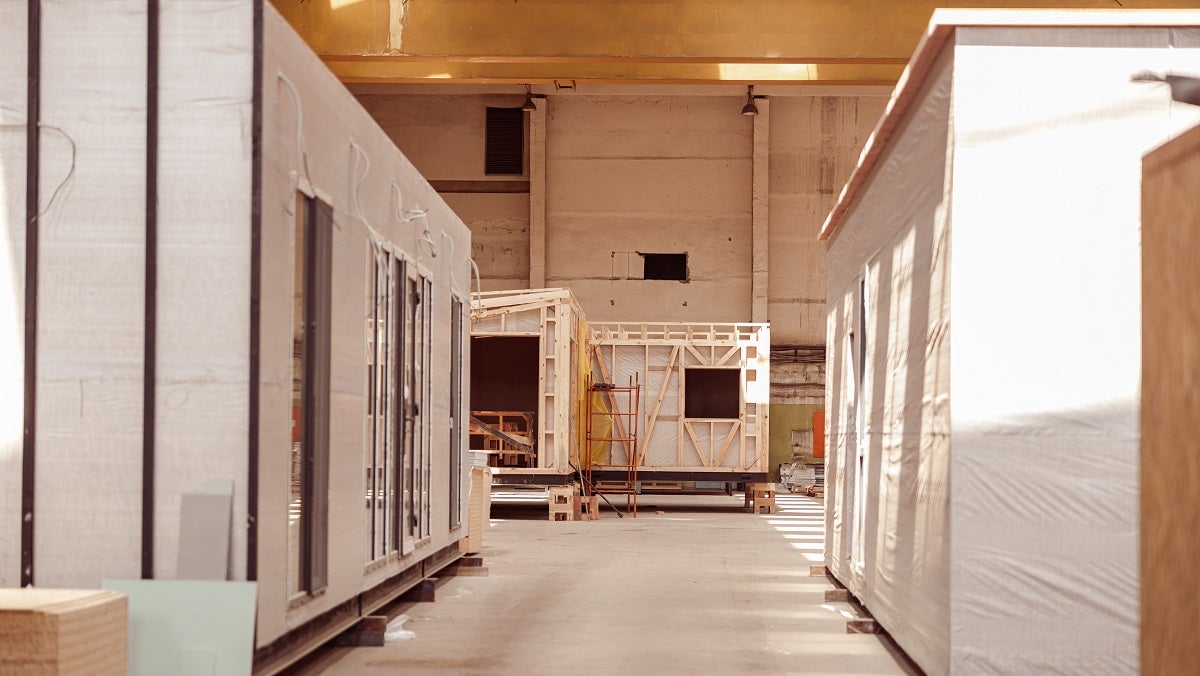
Construction is awash with sustainability targets, and the climate emergency means both regulatory pressures and market expectations are rising like sea levels.
The problems are not new, though. Back in 2013, the UK government published its industrial strategy Construction 2025, which set out clear targets for lower costs (down 33%) and emissions (50%), plus faster delivery (up 50%).
With a focus on productivity and labour issues, the Farmer Review followed in 2016, provocatively entitled Modernise or Die. Among 10 headline recommendations, the report challenged the industry to invest in R&D and innovation to support manufactured technologies, rather than traditional building methods, particularly in the housing sector.