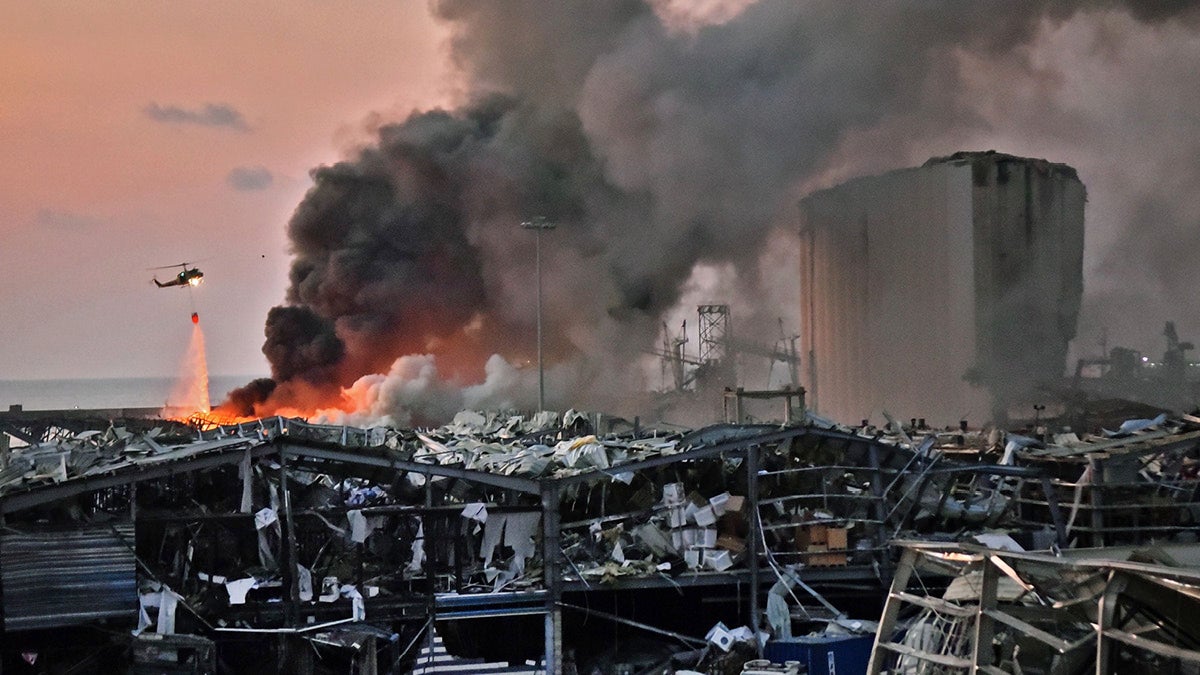
The huge explosion that destroyed so much of the Port of Beirut in August left Lebanon without its main trading gateway, exacerbating economic problems in a country already beset by spiralling inflation and growing levels of poverty and unemployment.
The blast killed 190 people and injured thousands when 2,750 tonnes of ammonium nitrate, which had been stored without the correct safety measures for the past six years, ignited.
The port is primarily an import hub for much of Lebanon’s goods, food and fuel, handling one million containers and nearly six million tonnes of cargo from 3,000 ships a year. Its loss will have significant consequences for Lebanon’s domestic supply chains and deprive shippers of a major Mediterranean and Middle-East trade hub.
Adaptability crucial in a crisis
“The Port of Beirut is significant for the region and its destruction will inevitably have an impact on the local economy in a myriad of ways,” says Antony Lovell, vice president of applications at planning consultants Vuealta.
One of the main concerns is that the disaster will disrupt the delivery of construction and other recovery-related materials. But given that businesses can’t plan in advance for such an unexpected humanitarian disaster, he says, the only way to avoid this is if supply chains are adaptable and quick to respond.
This agility could mean flexing processes so operations can resume at undamaged areas of the port or potentially diverting ships to Tripoli and then trucking the freight back to Beirut, he explains.
“Having achieved agility, the measure of resilience is defined by how all the links in the supply chain can adapt and respond to the new situation,” says Lovell, but this requires co-ordinated planning, across multiple companies in close to real time. “Any deficiencies in planning agility will reduce the network resilience and at a time of a natural disaster there will be humanitarian consequences,” he warns.
How AI can safeguard supply chains
While the explosion in Beirut was both unexpected and unprecedented, says Philip Ashton, chief executive of logistics specialists 7 Bridges, transport hubs are constantly shutting down across the world. This can be a consequence of any number of events, from health crises and cyberattacks, to weather patterns and civil unrest.
To deal with what he dubs black swan events, Ashton believes artificial intelligence (AI) is now a fundamental technology for supply chains, especially as factors such as outsourcing, sub-contracting and globalisation add to their complexity.
In the past, companies have tried to stay on top of situations with huge teams working on sprawling spreadsheets, but now, he says: “You have to be able to build a system that is adaptive without your intervention,” allowing you to seamlessly re-route, shift capacity and keep supply chains moving.
The measure of resilience is defined by how all the links in the supply chain can adapt and respond to the new situation
Data-driven systems allow you to approach problems in a more systematic way, so you can simulate what’s going to happen and run through all the different scenarios.
In essence, a hub should be able to go down without you even noticing and the system just adapts. “That’s how you can move systematically from fragile to robust supply chains,” says Ashton.
“Ultimately we believe AI is the only practical way to approach this problem because the computational power required to assess all the different ways you can get your products to a customer, and how to do that efficiently, is extremely complex and simply can’t be processed by a person.”
In Beirut, for instance, the extra data processing power would have enabled shippers and freight companies to handle a lot more information, scale up operations at Tripoli and re-route freight once it was landed. “What you want is inter-operability between multiple different ports, air freight hubs and road routes,” says Ashton. “Rather than simply queuing up, AI can show shippers a faster route.”
Companies left unprepared for disasters
A recent survey of 200 supply chain and finance professionals by procurement specialists Ivalua looked at how organisations plan for supply chain risk. But despite the fact that three quarters (74 per cent) of UK businesses have encountered some form of risk, including supplier failure and supply shortages, it found more than half don’t have any contingency plans in place.
It’s something that worries Jay Muelhoefer, chief growth officer at supply chain management company Kinaxis. “The most dangerous thing a company can do in managing supply chain risks, is to do nothing at all,” he says. “Even in these uncertain times, manufacturers can’t be paralysed by fear of change and must start moving on their digital transformation journey.
“Well-worn sequential supply chain planning approaches have proven unfit for this purpose. They’re too slow and inaccurate. That’s unsurprising when you consider they’re based on teams working independently in silos, gathering data in disconnected spreadsheets before passing results down the chain.”
In contrast, concurrent planning, which can be powered by AI, creates and manages synchronised plans across the supply chain. Each node in the chain is connected to the next, and each team shares data with the others and has the ability to run multiple “what if?” scenarios.
“If someone makes a change, it’s instantly reflected up and down the rest of the network. Everyone stays strategically aligned, informed and confident,” says Muelhoefer.
Concurrent planning is already being deployed by major players such as P&G and Merck, and has become essential to many operations because it’s fast, connected and reliable. “It drives agility, enabling decision-makers to analyse and determine the best course of action hourly or even by the minute, for the entire supply chain,” he says.
“This makes concurrent planning particularly well suited to helping supply chains cope with, plan for and respond to disasters, which by their nature require a rapid response.”
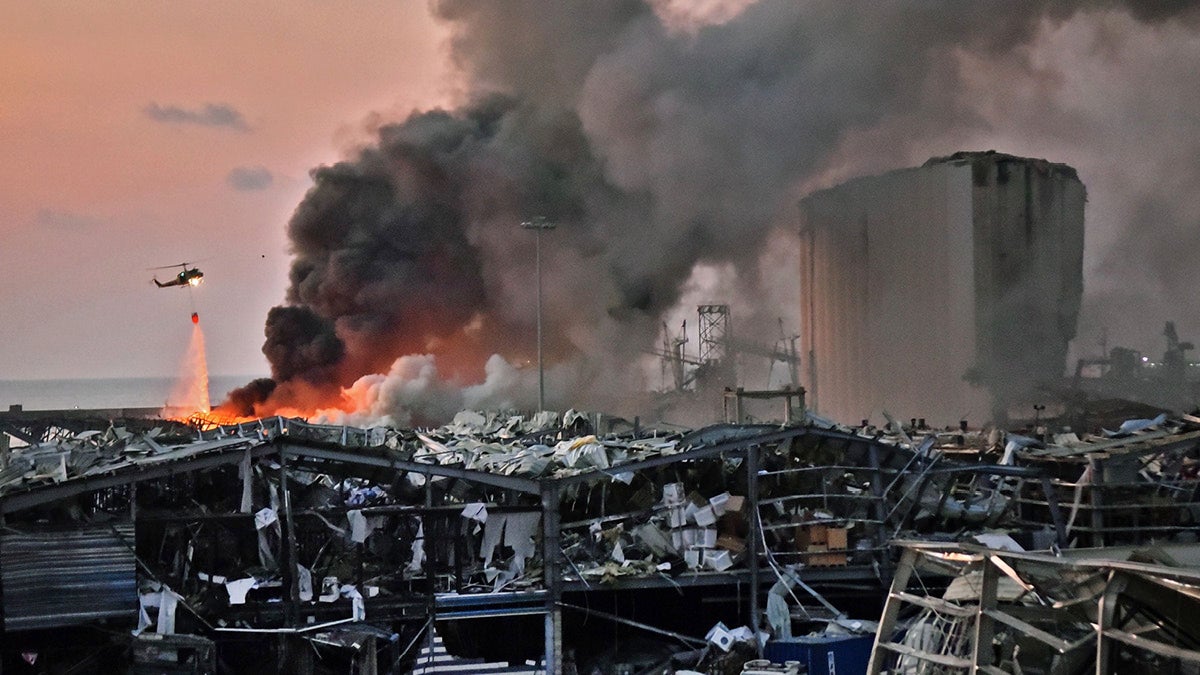
The huge explosion that destroyed so much of the Port of Beirut in August left Lebanon without its main trading gateway, exacerbating economic problems in a country already beset by spiralling inflation and growing levels of poverty and unemployment.
The blast killed 190 people and injured thousands when 2,750 tonnes of ammonium nitrate, which had been stored without the correct safety measures for the past six years, ignited.
The port is primarily an import hub for much of Lebanon’s goods, food and fuel, handling one million containers and nearly six million tonnes of cargo from 3,000 ships a year. Its loss will have significant consequences for Lebanon's domestic supply chains and deprive shippers of a major Mediterranean and Middle-East trade hub.