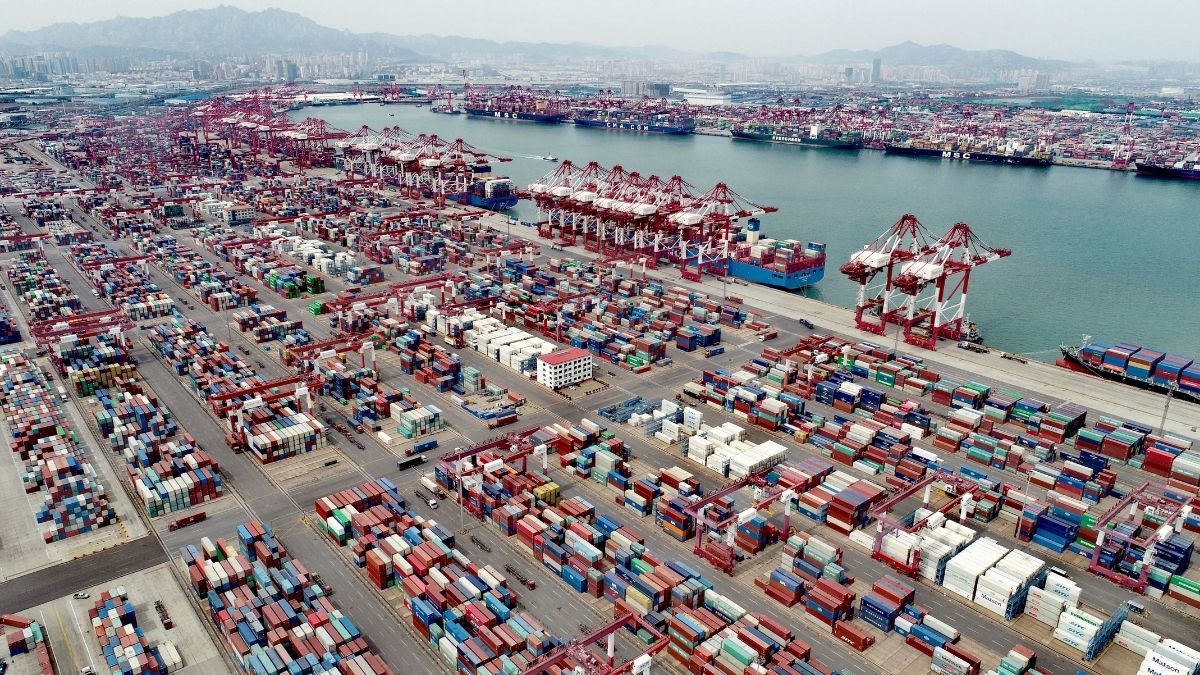
China’s zero-Covid policy has been creating serious knock-on effects for global supply chains and trade since the first lockdowns in 2020. The virus-containment restrictions in China have been among the harshest in the world and it did not take long for the effects to be felt beyond its borders. Chaotic, obstructed global trade caused by the pandemic exposed the heavy international reliance on Chinese-made products, materials and components, and the supply chains that originate from Chinese ports.
After two challenging years for logistics and trade, Chinese president Xi Jinping told state broadcaster CCTV in mid-March that the country would continue to stick with its “dynamic zero” policy in response to the latest outbreak of the omicron variant. The policy includes government-built quarantine facilities for people who test positive, widespread PCR testing in affected geographical areas and targeted lockdowns.
At the time, the north-eastern industrial province of Jilin was most heavily affected, along with cases reported in provinces and cities along China’s east coast and inland. Researchers at China’s Lanzhou University told the media they were confident this latest outbreak will be under control by early April.
Since then, however, further restrictions have been introduced by the government. Mass testing has been ramped up in Beijing, along with the closure of restaurants and entertainment venues. In Shanghai, residents have been forbidden from leaving their homes, food deliveries have been banned and infected patients have been quarantined.
Arnold Ma, founder and CEO of Qumin, a digital agency that connects China and Europe, cautions that these outbreaks suggest that “the country’s battle against the virus is far from the end”.
But what do these latest pockets of Covid mean for world trade and supply chains, have there been improvements in the way business with China is being done, and have lessons been learned about the overreliance on China?
Laurence Dellicott, director of supplier management and supply chain services at logistics technology firm MySupply by Avnet Silica, says there are “definite signs that China is emerging from the pandemic, particularly because of a successful vaccination programme”.
“Economic growth is continuing [but] we’re still seeing city lockdowns with a zero-Covid policy being seen as too aggressive by some,” he says.
However, Dellicott says the trade and supply chain problems are not just Covid-related: “Trade disputes between the US and China were happening long before the current variants … Generally, costs have continued to rise across the board, with many manufacturers struggling to keep up with the scale of demand … in China and elsewhere.”
Kevin Gaskell, business growth expert and author of Inspired Leadership: How you can achieve extraordinary results in business, says that during the pandemic, China’s logistics “simply froze” because ships, trucks, planes and containers were locked down or not available in the right place at the right time.
“Modern inventory management works on the basis of efficient supply chains minimising required stock holding,” Gaskell explains. “When supply lines were disrupted, buffer stocks were quickly consumed and, due to logistical blocks and manufacturing lockdown in China, replenishment was difficult, if not impossible, for an extended period.”
Dellicott says that businesses are “seriously reviewing putting all of their eggs in one basket and spreading their manufacturing more than they usually would, in case of another international crisis.”
Operations in neighbouring countries can function as a backup in a situation like a pandemic
Many businesses are considering alternatives to using China as a one-stop manufacturing shop, with reports of a deltacron variant potentially speeding up this decision, Dellicott says.
For manufacturers, the pandemic has highlighted the importance of having manufacturing hubs outside China or maintaining a presence in China, while planning with neighbouring countries.
“Some companies have been playing on the so-called China Plus One strategy, which means they have expanded their operations to surrounding countries such as Vietnam and India as a way to reduce their reliance on China as a production base,” Ma says. “The strategy allows companies to have their presence in China so that they won’t miss out on opportunities offered by the lucrative market.”
The China Plus One strategy offers businesses flexibility without abandoning opportunities in China, as Ma explains: “Operations in neighbouring countries can function as a backup, in a situation like a pandemic, when restrictions in those regions might not be as tough as that in China.”
However, in some markets, governments have stepped in to make it easier for businesses to manufacture at or close to home. In the US, the government has invested $52bn (£38bn) in the semiconductor sector under the CHIPS for America Act. Meanwhile, in India, the government has approved a $19bn (£15bn) proposal to incentivise global companies to move factories to the country, including manufacturers in the automotive, electronics, pharmaceutical and textiles sectors.
In China itself, the economic impact of pandemic-related pressures on manufacturing and supply chains has improved the sophistication of logistics in the country, according to a report by McKinsey. This includes greater use of automation technology for digitised, highly visible supply chains, and expansion of air freight in response to shipping delays.
Gaskell says that the challenges with manufacturing and logistics are not specific to China because most interactions with international suppliers were affected by pandemic lockdowns. However, he adds that many in the UK and Europe are now reconsidering the price benefits of sourcing from China.
“In my companies, we are actively reviewing alternative local suppliers,” Gaskell says. “The transition will not be simple or quick, but alternative sources need to be considered as the pandemic has highlighted the existential problem of relying on long-distance supply chains.”
The perfect storm of China’s strict zero-Covid policy and increasing reliance on China for cheap manufacturing and smooth supply chains has created two years of serious disruption. But Kayla McEwan, a strategic analyst at TecEx, a customs compliance specialist, cautions against complacency. Other factors are at play – many of these have not only contributed to the problems during the pandemic but could become ongoing or re-emerging concerns.
McEwan says that for the UK and Europe, Brexit is the first issue that comes to mind because of the “trade barriers and other complexities” created since the 2016 vote to leave the EU. More broadly, she cites “other adverse factors”, such as labour shortages, global supply issues and panic-buying, as causes of worldwide logistics and manufacturing headaches. The overriding lesson goes beyond over-reliance on China – agile businesses will be better equipped to overcome future disruptions if they implement strategies that spread the risk and the responsibilities.
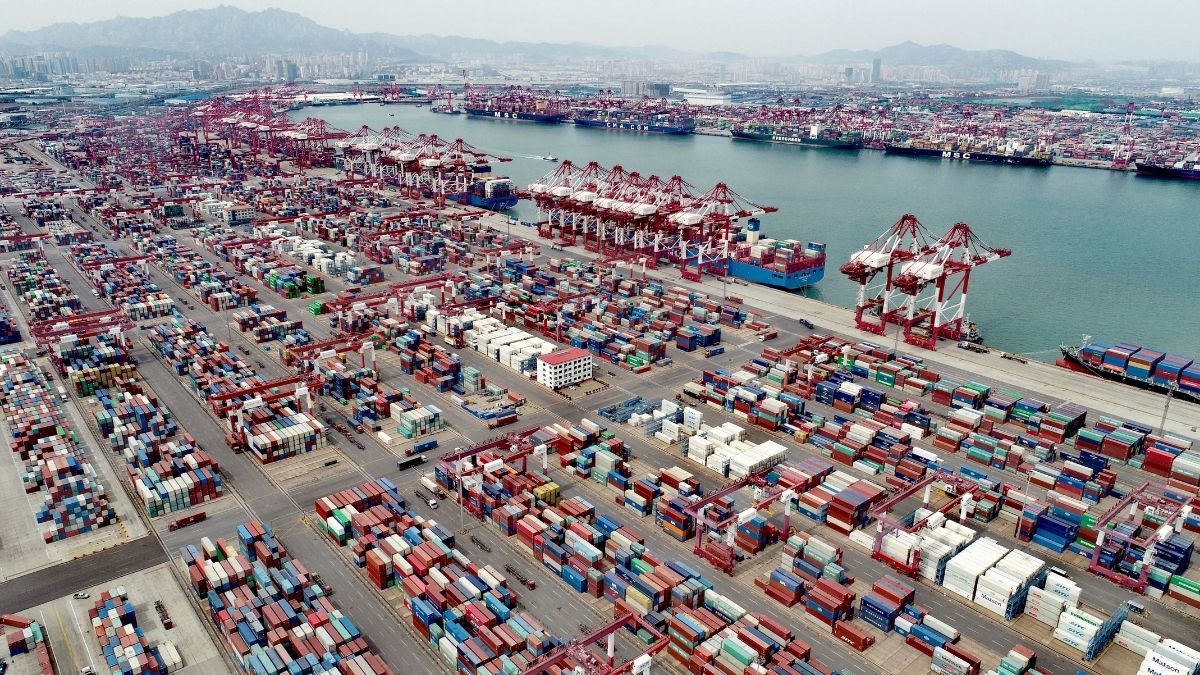
China’s zero-Covid policy has been creating serious knock-on effects for global supply chains and trade since the first lockdowns in 2020. The virus-containment restrictions in China have been among the harshest in the world and it did not take long for the effects to be felt beyond its borders. Chaotic, obstructed global trade caused by the pandemic exposed the heavy international reliance on Chinese-made products, materials and components, and the supply chains that originate from Chinese ports.
After two challenging years for logistics and trade, Chinese president Xi Jinping told state broadcaster CCTV in mid-March that the country would continue to stick with its “dynamic zero” policy in response to the latest outbreak of the omicron variant. The policy includes government-built quarantine facilities for people who test positive, widespread PCR testing in affected geographical areas and targeted lockdowns.
At the time, the north-eastern industrial province of Jilin was most heavily affected, along with cases reported in provinces and cities along China’s east coast and inland. Researchers at China’s Lanzhou University told the media they were confident this latest outbreak will be under control by early April.