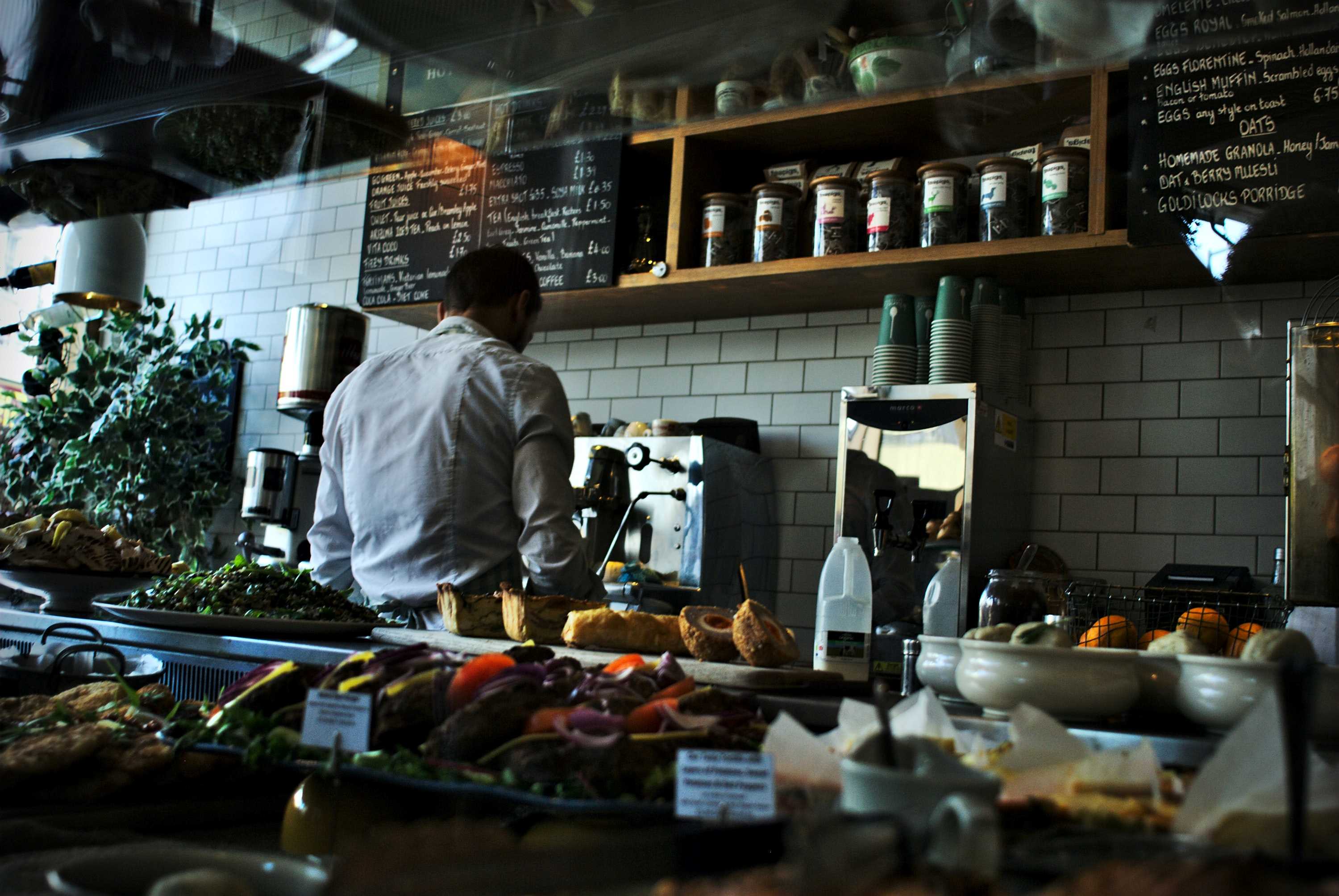
When the doors of Marylebone’s Crazy Pizza restaurant reopened in July, the aroma of warm pizza dough greeted customers upon arrival as they prepared to enjoy a slice of Italy in London at the end of England’s seven-month lockdown.
But while the sights and smells were the same, the accents were very different. The restaurant’s staff, from senior management to chefs and waiters, had previously consisted of Italian, French and Greek nationals, who had moved to London long before the pandemic.
But a combination of Covid-19 and post-Brexit immigration regulations saw thousands of EU workers return home, leaving Crazy Pizza operating with just 20% of its usual workforce. UK agency employees have since plugged some of the gaps, while thousands of other restaurants across the country have also been starved of labor.
Three months on, restaurants, retailers, meat processing plants, haulage companies and many other sectors are all competing for the same pool of so-called ‘low skilled’ workers on entry-level wages. This has resulted in staff shortages at every step in the supply chain, empty shelves at supermarkets and revised menus for restaurants facing importation delays.
In the short term, companies must convince a dwindling labor pool of UK-based workers to take what have traditionally been seen as undesirable jobs. “In the UK, the perception is that a restaurant job isn’t a job for life, whereas in Europe it’s really respected,” says Lara Harris, corporate sales director of Crazy Pizza’s parent company, Billionaire Life.
The haulage sector is facing the same challenge. “In the first quarter of this year, 55,000 drivers aged 45 and over left the industry,” says Kieran Smith, CEO of HGV and LGV recruitment agency Driver Require. “They left because of appalling conditions, anti-social hours and low pay. In the UK, we have third world washing and parking facilities for drivers.”
Cash could provide a short-term solution. Waitrose has increased delivery driver salaries up to £53,780 per year – a rise of 7% – while a survey by recruiter Indeed showed that wages in the hospitality sector rose by 2.7% in July alone, up to £9.75 per hour. In the first three months of 2021, that rate stood at £9.25 per hour and just £9 at the start of 2020.
The haulage sector is hopeful that attractive salaries will tempt some of the UK’s 330,000 HGV license holders to return to the industry or encourage unemployed bus and coach drivers to obtain HGV licenses. It’s also considering an advertising campaign, similar to that employed by the army, to convince young people and women to pursue a career in logistics.
But retaining workers long term and avoiding losing staff to the highest bidder will require more than just cash. “Improving roadside facilities won’t happen overnight, but you need to give people hope,” says Smith. “The government can do this by committing to a plan of action and dedicating a budget to improving working conditions for drivers.”
At Crazy Pizza, the focus is on optimising workplace culture. “Those companies that are providing the desirable environment and conditions for staff are winning the best staff right now,” says Harris. “That’s made us raise our game and make sure that we’re providing the best possible conditions and pay. You have to look after your staff to retain them.”
Modern slavery is a just a piece of paper… unless it is embedded in organisational plans
Companies are also pursuing innovative solutions to make their supply chains more resilient. In August, Co-op chief executive, Steve Murrells, revealed the company is retraining supermarket staff as lorry drivers. Transport collaboration with competitors is another potential avenue. “Your best partner could well be your competitor, because you’re delivering to the same customer,” says Rob Wright, a logistics and supply chain consultant at Scala Consulting.
Nearshoring is also helping to shorten supply chains, reduce delivery times and minimise stock shortages. “We source ingredients from all over Europe but we’ve realised we can get a lot of our fruit, vegetables, meat and even wine from the UK,” says Harris. Retailers are also moving away from sole supplier agreements. “Dual-sourcing reduces risk and gives your supply chain more resilience,” adds Wright.
Having learned the harsh lessons of the last 18 months and with Christmas on the horizon, retailers and restaurants are now holding more stock and increasing lead times, with the days of just-in-time inventory strategies a thing of the past. “We used to order ingredients and they’d arrive in two days and alcohol would take just 24 hours,” says Harris. “Now we have to order two weeks in advance and ensure we order a lot more stock.”
But not all goods can be sourced from the UK. Companies still need to minimise delays further down the supply chain. Technology firm RedCloud uses AI software to help farmers, small distributors and merchants use data to predict selling patterns and spot consumer trends so that they can fulfill their orders. “We want farmers to become more profitable,” says RedCloud CEO Justin Floyd. “If they can improve their margins, they can grow more products and meet fluctuating demand, which keeps goods moving through supply chains.”
In response to Brexit and the pandemic, a host of UK retailers have also opted to digitise their supply chains to maximise visibility across their entire network of suppliers. This has enabled them to view data in real time and make swift decisions to drive sustainable improvements in lead times, delivery reliability, and inventory reductions.
Digital supply chain company Core works with Asda, Primark, M&S and a host of other high profile UK retailers. The company’s CEO, Ben Puncher, has witnessed the digital revolution first hand: “Those brands have been able to keep their supply chains moving efficiently because they decided very early on to digitise their supply chains and do away with manual, old-fashioned spreadsheets that slow down decision making.”
But scenario modelling software could be the secret to planning for crises long before they arise and make supply chain issues a thing of the past. Software can help companies predict the potential financial impact of future disasters, for example climate change, or the environmental consequences of changes to their supply chains.
As the uncertainty of winter approaches and companies continue to optimise their supply chains in response to the challenges of the pandemic and Brexit, it seems that cash, digitisation and predictive technology will be the defining factors that dictate who survives.
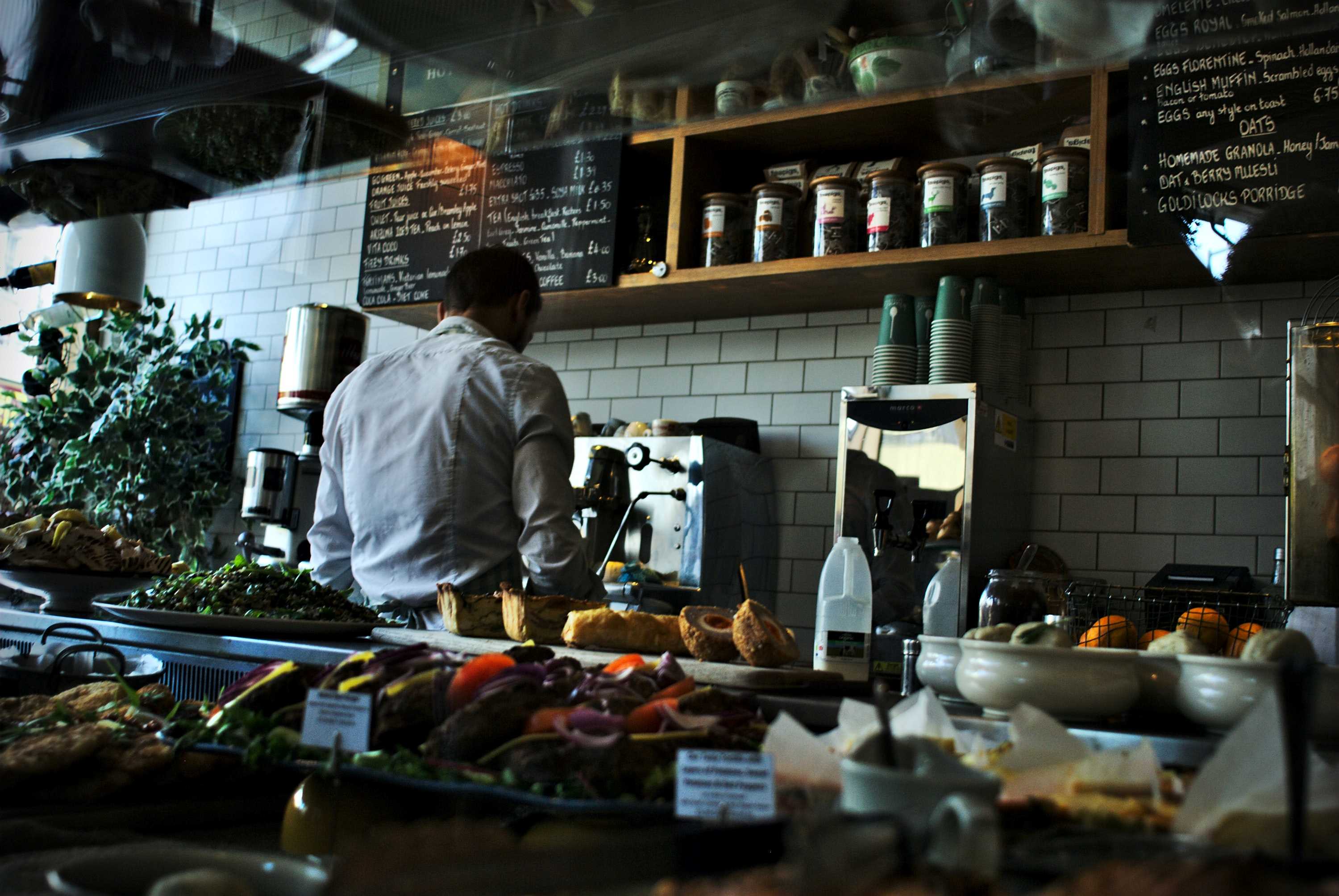
When the doors of Marylebone’s Crazy Pizza restaurant reopened in July, the aroma of warm pizza dough greeted customers upon arrival as they prepared to enjoy a slice of Italy in London at the end of England’s seven-month lockdown.
But while the sights and smells were the same, the accents were very different. The restaurant’s staff, from senior management to chefs and waiters, had previously consisted of Italian, French and Greek nationals, who had moved to London long before the pandemic.
But a combination of Covid-19 and post-Brexit immigration regulations saw thousands of EU workers return home, leaving Crazy Pizza operating with just 20% of its usual workforce. UK agency employees have since plugged some of the gaps, while thousands of other restaurants across the country have also been starved of labor.