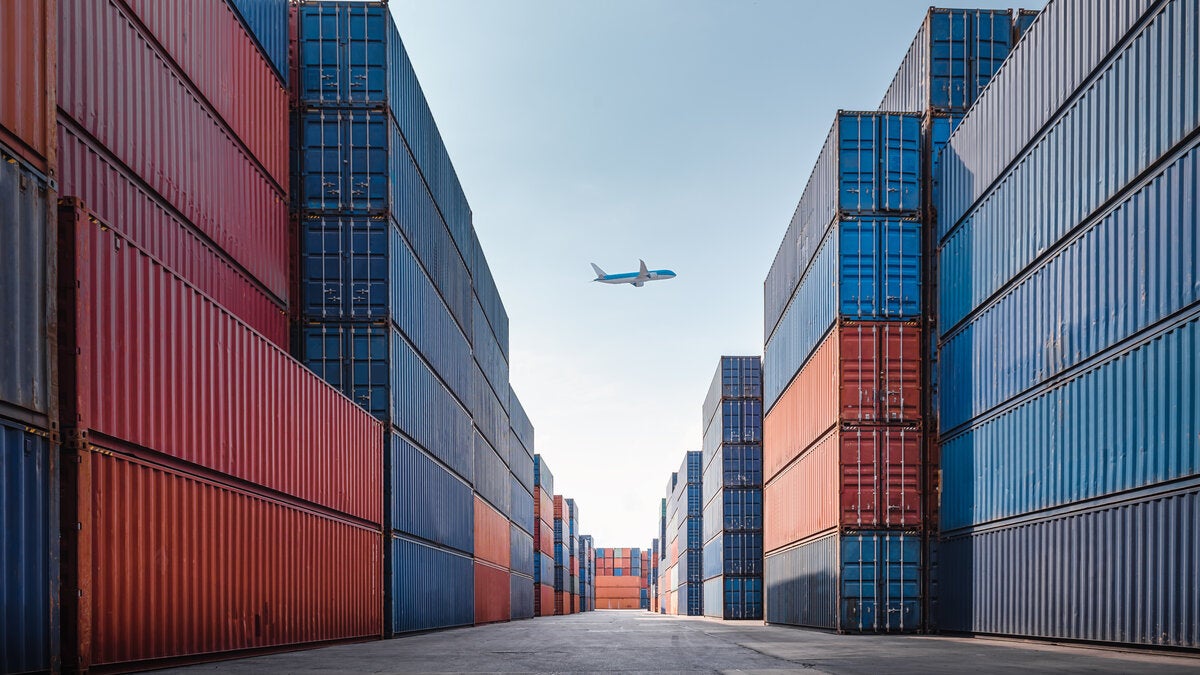
It has been a difficult few years for manufacturers, suppliers and businesses that sell products worldwide. Recent events highlighted the weaknesses in supply chains. Raw materials are in short supply, pushing prices higher and making decisions more difficult. Yet customer demand for new products in a timely manner has not adapted to the new circumstances. This means there is little room for error in every decision made in sourcing, supplying and manufacturing.
For years, the world ran on a just-in-time manufacturing methodology – which worked in a time of plentiful, reliable supply. “And there weren’t as many issues impacting the flow of goods,” says Julie Driscoll, executive advisor at aPriori. The company automatically generates product manufacturing intelligence that helps manufacturers collaborate across the product development process to make better design, sourcing and manufacturing decisions that yield higher-value products in less time.
Mistakes cost time and money, meaning companies must feel confident in all product development decisions. “There’s a lot of buyer demand for personalised products with a broader range of features. Companies are trying to innovate faster and move from design to market as quickly as possible,” says Driscoll.
aPriori recently surveyed 24 manufacturers about the pain points they have been experiencing in sourcing and buying products. The key finding? “Current sourcing processes have inefficiencies due to incomplete information and manual steps,” says Driscoll. Using data and technology to be more transparent about the product design, price, method of manufacturing and potential manufacturing issues can help businesses collaborate between teams, reducing the time spent searching for information and haggling on the phone or via email.
Fast isn’t enough. You need to be able to respond, because things might not go exactly as you wanted
This is vital at a time when trusted manufacturers may be unable to produce at the scale they once did due to staff or material shortages. Businesses are having to find, befriend and broker deals with organisations they have not previously worked with, introducing friction into an already strained process. “We’re talking about reducing friction across your entire product development process,” says Driscoll. “From early design of new parts or new products, we can help you speed up the process to get you to market quicker.” aPriori was recently used for a deep dive manufacturing and cost analysis for assembly by agriculture and construction equipment company CNH Industrial that evaluated 104 unique part numbers and fine-tuned the manufacturing process, saving the company $2.1m.
aPriori’s technology helps reduce friction both while products and components are manufactured and before they’re delivered. More than 70% of a product’s cost is determined at the design stage, but once set up and in production, reworking products mid-manufacture can cause costly waste. aPriori’s software helps identify any manufacturability issues early in the process, suggesting how an item can be made, how long it will take to make, how much material it’s going to use, and what the carbon footprint of the product will be. “Automating the product analysis and making the data easy to access and share are crucial to expediting the process,” says Driscoll. “Product life cycles are shrinking dramatically, and there’s so much more global competition.”
That puts pressure not just on the design process, but on the buying process too.
Previously, the push was that you had to go fast,” says Driscoll. “Now, fast isn’t enough. You need to be able to respond, because things might not go exactly as you wanted.” Whether it’s a shortage of a key component or shifting the manufacturing to an alternative at short notice, hurdles exist everywhere – and having visibility for options can help you to avoid them. “Digital transformation allows manufacturers to move quickly and to be responsive to disruption,” says Driscoll. “You don’t know when the next black-swan event is going to happen.”
Of course, the supply chain will not remain stalled forever – but the importance of remaining nimble will continue for years to come. “Even if the disruption settles down, efficiency and time to market are going to remain important,” says Driscoll. “If you have inefficiencies in your process, you are going to be a laggard.”
To see how real time data can streamline your product innovation lifecycle, visit aPriori.com/contact or call +44 (0)78517 91322
Promoted by aPriori
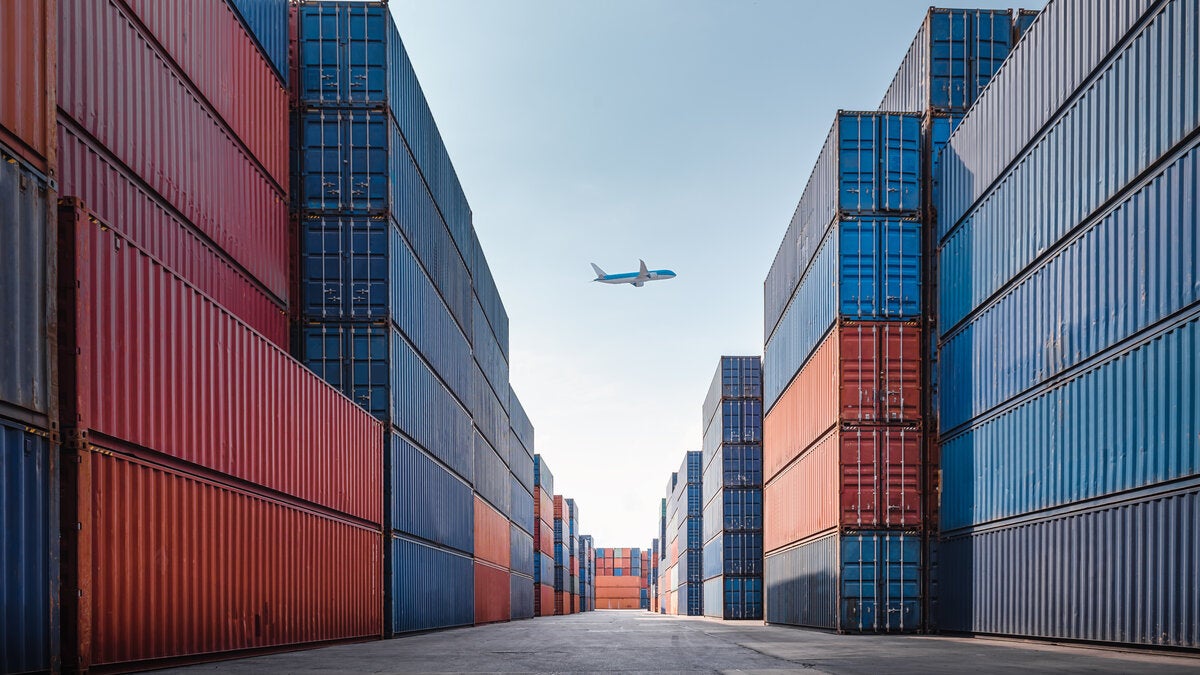
It has been a difficult few years for manufacturers, suppliers and businesses that sell products worldwide. Recent events highlighted the weaknesses in supply chains. Raw materials are in short supply, pushing prices higher and making decisions more difficult. Yet customer demand for new products in a timely manner has not adapted to the new circumstances. This means there is little room for error in every decision made in sourcing, supplying and manufacturing.
For years, the world ran on a just-in-time manufacturing methodology – which worked in a time of plentiful, reliable supply. “And there weren’t as many issues impacting the flow of goods,” says Julie Driscoll, executive advisor at aPriori. The company automatically generates product manufacturing intelligence that helps manufacturers collaborate across the product development process to make better design, sourcing and manufacturing decisions that yield higher-value products in less time.
Mistakes cost time and money, meaning companies must feel confident in all product development decisions. “There’s a lot of buyer demand for personalised products with a broader range of features. Companies are trying to innovate faster and move from design to market as quickly as possible,” says Driscoll.