The transformative impact of additive manufacturing is well-known by global manufacturing executives. Faster prototyping, less waste and more product flexibility are hard to resist for any business, but 53 per cent of respondents to the GE Global Innovation Barometer do not believe additive manufacturing has yet reached its full potential.
‘Fear of the unknown’ is certainly an issue when it comes to the widespread adoption of additive manufacturing across virtually all sectors, especially as finding staff with the appropriate design and production skills to make the implementation of additive manufacturing successful is a major barrier facing companies looking to take advantage of the next revolution in manufacturing. Understanding the massive variety of materials available, their distinct properties and what printing machines are most appropriate can at first seem like a difficult process to initiate.
Behrang Poorganji, materials development manager at GE Additive, works with a team of engineers to ensure customers have the most suitable materials for their products, even going as far as creating new materials based exactly on user requirements. These custom-made material recipes offer at least the same or better performance than conventional substances and improve profitability due to their bespoke nature.
“The materials we have today are all built on the conventional manufacturing paradigms that actually impose unnecessary constraints on designing a material. But now we have a technology that can open the boundaries of design and manufacturing like never before,” says Mr Poorganji. “By asking our customers what their performance needs are we can create whatever works best for their applications, whether it be a material with a lightweight structure or one that is able to withstand high temperatures or pressure.”
While choosing the correct material is a vital part of the process, machine selection can be equally important. Depending on the industry, there are a range of machines in terms of size and material compatibility to consider. For example, the GE’s Concept Laser Mlab machines are more suitable to smaller applications and for using with precious metals, whereas larger parts can be fabricated in a Concept Laser Xline.
Additive manufacturing excels at building complex parts out of expensive materials, as the process only uses the exact amount of material needed, and in the process cuts waste and saves on material costs over traditional manufacturing methods. Industries that tend to use higher grade and more expensive materials, like aerospace manufacturers and the medical device industry, can see considerable raw material savings when making the transition to additive.
Potential additive manufacturing customers usually want to hear about successful projects and case studies as part of their decision making plans, but the best way to clearly see if additive manufacturing is right for a company is to engage directly with those additive experts who can advise based on extensive market knowledge.
The vast majority of companies would benefit from partnering with an external additive manufacturing expert to ensure both a cost effective implementation process and a quicker product cycle. “If you decide to go it alone with additive manufacturing, you’re talking about significant investment in a lot of cases. That is just something that not a lot of companies can quite frankly afford,” says Josh Mook, Engineering Manager at GE Additive.
“We focus on supporting the customer through their journey to product and try to understand exactly how they differentiate themselves from competitors. Through an extensive discovery workshop we find ways additive can impact our customers and then begin to generate the business cases to support its introduction,” adds Mr Mook.
When a clear connection is established between additive manufacturing and bottomline business benefits, especially around the impact it can have on improving competitiveness in the market place; customers quickly start to come around to the idea of utilising additive as a key instrument in their manufacturing toolbox.
The success rate of implementation is going to be much higher using a process where you have an expert with you every step of the way
Collaborating with an additive manufacturing specialist shouldn’t be a one-off project, but rather a long-term business relationship. Additive manufacturers should play a central role in everything from identifying use cases to achieving product certifications and beginning low-rate production, all the way up to implementing additive manufactured components into a product.
“We believe the success rate of implementation is going to be much higher using a process like this where you have an expert with you every step of the way, opposed to just giving you a pat on the back saying good luck and goodbye,” says Mr Mook. Working with a design team that has a proven track record of success with dozens of other projects around additive manufacturing helps ensure that whatever issues are encountered during the implementation process, will have all been seen before and the team will know how to overcome them.
GE is unique in the additive manufacturing environment as it’s the only original equipment manufacturer who is designing for additive and introducing their own products into the field using the technology, allowing the company to showcase the full possibilities of additive. The Advanced Turboprop Engine from GE Aviation saw around 12 to 18 months eliminated from its product design cycle, thanks to the use of additive manufacturing.
The changes additive manufacturing will bring to the supply chain are expected to be significant, as a single printing machine will, in some circumstances, be able to replace an entire factory building and the complex infrastructure support will no longer be required. The aerospace and biomedical industries have led the way in the adoption of additive manufacturing, but the next few years will undoubtedly see an increasing number of sectors such as, power generation, renewable energy, automotive and industrial equipment fully embracing additive manufacturing, with those companies who hesitate set to fall behind.
“We have a saying at GE Additive: additive manufacturing is here. You’re either going to be the leader in additive or a victim of it. The companies that don’t see the value and choose to sit on the sidelines are either going to be overtaken by competitors or potentially even lose to new market entrants, as additive effectively lowers the barrier to entry in a lot of industries,” said Mr Mook.
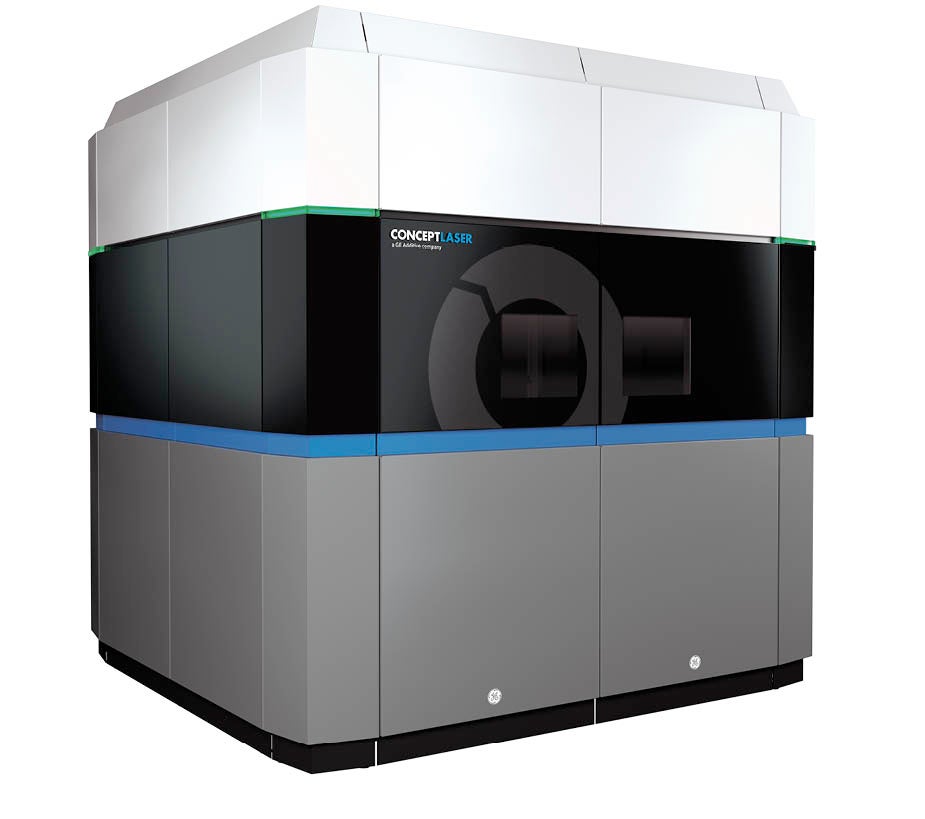