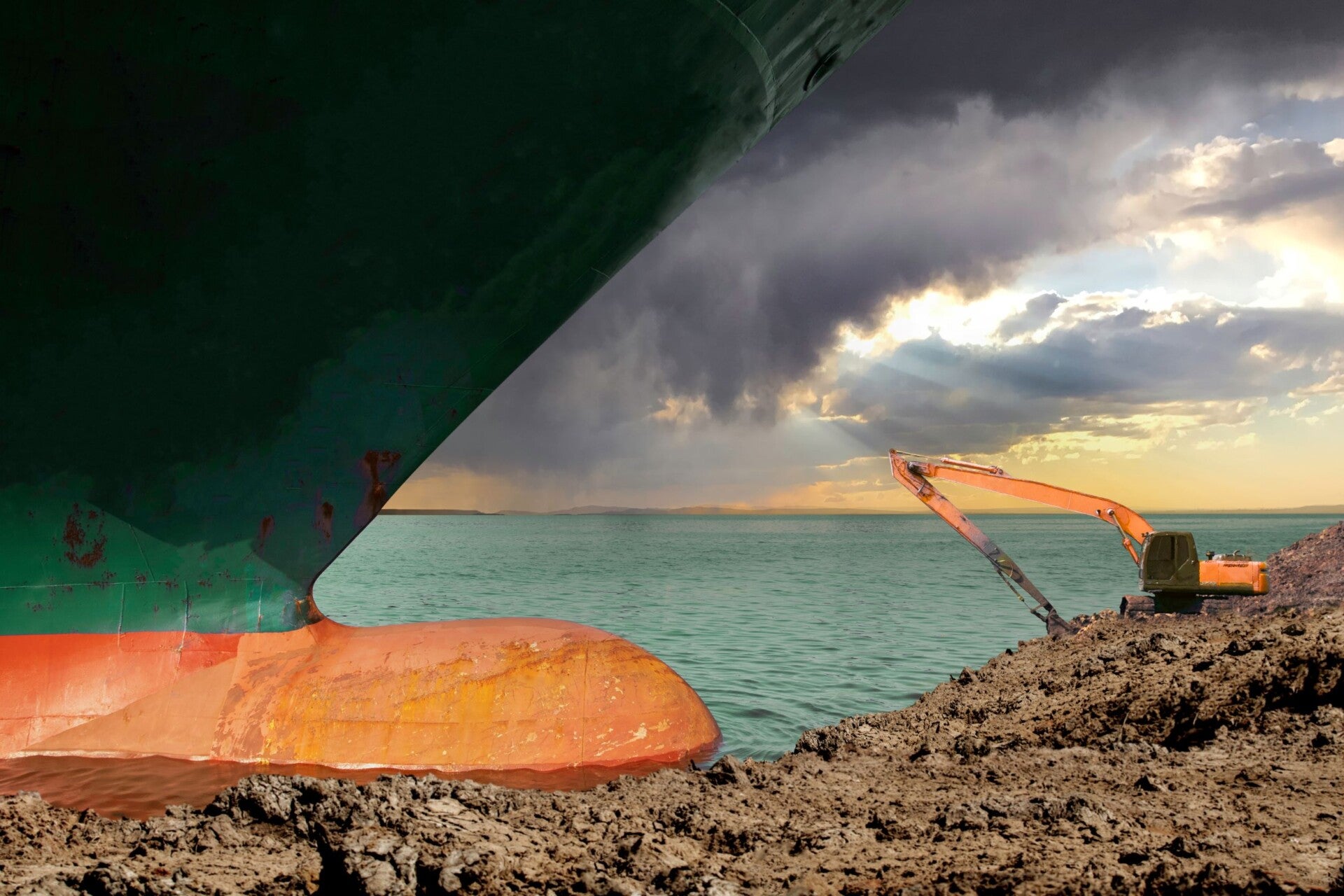
Inside the walls of his home-cum-office in south west London, Alex Stewart held his head in his hands and prepared for the worst. Less than a year after launching his eco-friendly travel goods brand, OneNine5, the entrepreneur watched on in despair as global travel shuddered to a halt following the outbreak of Covid-19 at the start of 2020.
Almost overnight, the brand’s daily sales dropped to single digits as airlines were grounded and millions of people across the globe were ordered to stay at home for lengthy lockdowns. For much of the next 12 months, Stewart was forced to sit tight and hope the storm would pass in time for his fledgling brand to survive.
As lockdowns lifted and travel resumed, so too did sales, but another storm has duly followed. In August, OneNine5’s factory in Shanghai was forced to close because of a rise in Covid-19 cases. Freight costs from China to Felixstowe then tripled from £1,200 to £3,500. Electricity shortages in China have also limited the factory’s output and caused manufacturing lead times to rise from 30 days to at least 50-60.
The brand now faces stock shortages over the Christmas period, just as orders have started to roll in. It isn’t alone. Shortages of construction materials, silicon chips and food products have caused massive disruption to crucial industries. It’s why an increasing number of companies are implementing business continuity plans to safeguard against unexpected future events so they can keep running and make money in times of crisis.
Patrick Roberts, the co-owner of Cambridge Risk Solutions, says a robust continuity plan has three parts. He said: “Firstly, we carry out a risk assessment to see how your business could be impacted in the event of a disaster and what you can do to lessen that risk. Secondly, you have instant response: the process you will follow as an event unfolds. Finally, you have a longer-term business recovery: how you’ll adapt as a company in the aftermath of a disaster, such as Covid.”
Mitigation is on the agenda of a host of companies. Ikea is set to move much of its production to Turkey to shorten its supply chains and avoid increases in shipping costs. The price of an Ikea container from east Asia to Europe jumped from $2,000 (£1,453) to $12,000 (£8,723) during the pandemic. Clothing brand Benetton has also moved production to Serbia, Croatia, Turkey, Tunisia and Egypt with the aim of halving production in east Asia.
We’re a small team with limited resources, the effort and time taken to build a trusted relationship with a responsible manufacturer is time intensive and wouldn’t be an easy process for us.”
But for smaller businesses, such as OneNine5, bringing their production closer to home simply isn’t an option. “We’d love to manufacture in the UK and explored UK factories before launching in 2019, but [they] could only manufacture using waxed cottons and leather,” says Stewart. “We’re a small team with limited resources, the effort and time taken to build a trusted relationship with a responsible manufacturer is time intensive and wouldn’t be an easy process for us.”
Supply chain mapping is an integral part of the mitigation and crisis response process. While most businesses have visibility of tier one and two suppliers, many are unaware of who their tier three suppliers are, further down the chain. These are suppliers that may provide raw materials, for example a farm that sells cotton to clothing manufacturers. In the event of a major disaster, damage to tier three suppliers can cause manufacturing delays and stock shortages higher up the chain.
Roberts advises his clients to create a detailed map of their suppliers but says it can be a complex process. “Often, tier one suppliers won’t discuss that with you because they see it as commercially confidential information,” he says. Cost is another potential issue. He adds: “Businesses can incur a lot of cost, they have to ask themselves, how much are they willing to pay for this level of certainty and visibility?”
Companies are increasingly willing to stump up cash to reduce their risk. Suppliview is a tool many are using to gain greater visibility of their entire supply chains so they can react at speed in a crisis. “It works well when you’ve got quite a large and complex supply chain,” says Benjamin Puncher, CEO of CORE, the software company that has developed the tool. “If your warehouse burns down, you need to quickly determine where your stock is in the supply chain and how you can get your hands on it so you can keep shelves full and meet the demands of customers.”
Creating a step-by-step process to follow during a crisis is another essential component of a business continuity plan. Office-based firms across the world were forced to implement IT solutions so that staff could work from home during the pandemic. Those that already had a continuity plan in place were quickly able to switch to home working; those that didn’t were faced with a race to get back online and ensure their workers could continue to do their jobs.
But even the best plans can be undone if businesses fail to spot threats. “You have to have a preoccupation with failure,” says Roberts. “You need to constantly think ‘what is the worst-case scenario in this situation?’” Adopting that mindset requires companies to undergo behavioural and cultural change. “We have clients who have continuity plans but then haven’t used them during a crisis and sort of muddled through,” he adds. “High reliability organisations don’t do that; they create a plan and then stick to it when things go wrong.”
When the dust settles in the aftermath of a crisis, continuity plans ensure lessons are learnt and businesses evolve. For Stewart, change is already underway. Recently the brand switched from sea to rail freight to reduce the risk of delays. But it could take an injection of cash to ensure further problems are avoided. “We need to explore external investment so that we can buy more stock in advance and avoid cash flow problems,” he says.
Meanwhile, Roberts is keen to see other industries adopt continuity plans. “I think higher education could really benefit,” he adds. “As we’ve seen during Covid, they’re not prepared for major disasters and it’s students who miss out.” With the climate crisis escalating and the pandemic set to impact economies and businesses for the foreseeable future, companies that fail to plan for disaster may not survive the next one.
Crucial lessons to avoid supply chain disruption
- Reduce your risk
When Covid-19 spread across Europe at the start of 2020 many brick and mortar businesses were ordered to close their doors with minimal notice. Those companies that didn’t have sufficient cash reserves or a digital strategy soon became insolvent. But a thorough risk assessment could’ve helped many companies to survive those early months.
Roberts says many businesses fail to understand their level of risk. He says: “I did a risk assessment with a client many years ago and we found out that if they couldn’t ship goods and invoice for two days they would run out of cash. Companies need to have cash in the bank to be able to pay their suppliers and staff in the event of a disaster.”
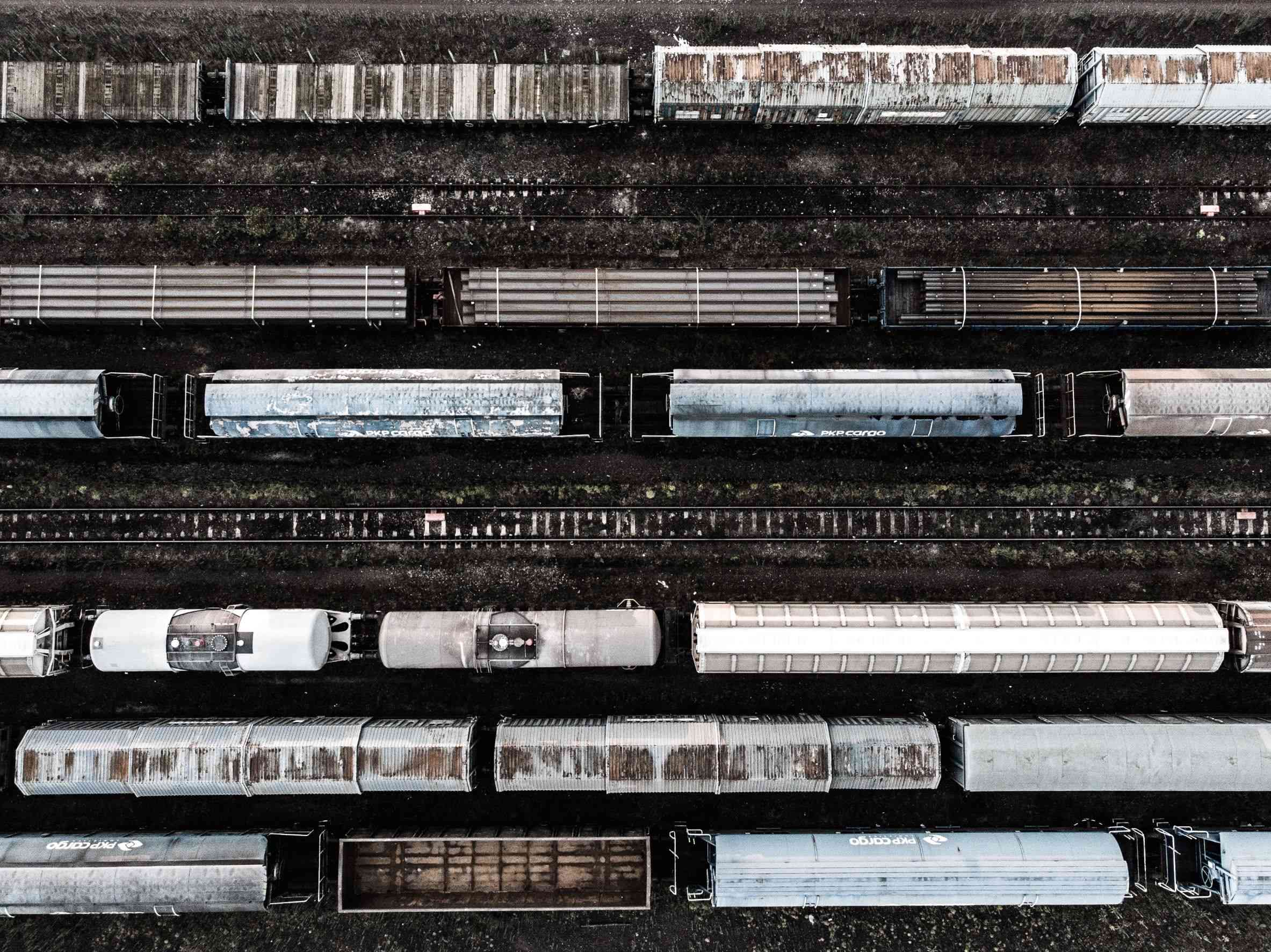
2. Map out your supply chain
Companies that don’t own their own factories or outsource the manufacturing of products to suppliers in other countries often end up with long and complex supply chains. Those chains can help to reduce manufacturing costs, but they also create chains that are vulnerable to disruption.
Supply chain mapping can help to spot risks and avoid potential pitfalls. By creating a detailed document of all companies, suppliers and individuals involved in a supply chain, businesses can put strategies in place when a supplier faces a shortage or there is a surge in product demand.
3. Keep your plan up to date
High growth companies who quickly restructure or hire staff will need to update their continuity plan on a regular basis. “If the executive team changes on an annual basis or even faster than that, then you need to revisit your plan every few months,” says Roberts. “Continuity plans are no use if they’re out of date.”
For bigger businesses with low staff turnover and fixed processes, annual training exercises can prepare staff for what they need to do in times of crisis. “You need to know who is responsible for carrying out specific tasks when problems arise,” adds Roberts.
4. Learn the right lessons
Businesses that have survived the perfect storm of Covid-19, Brexit and the Suez Canal blockage without a continuity plan may believe they are well equipped to deal with the next disaster that affects the western world.
But Roberts says complacency can be fatal. “There is a danger that companies can be optimistic and think they can just muddle through problems,” he adds. “Businesses need to be constantly on the lookout for problems; it’s better to overreact than respond too late.”
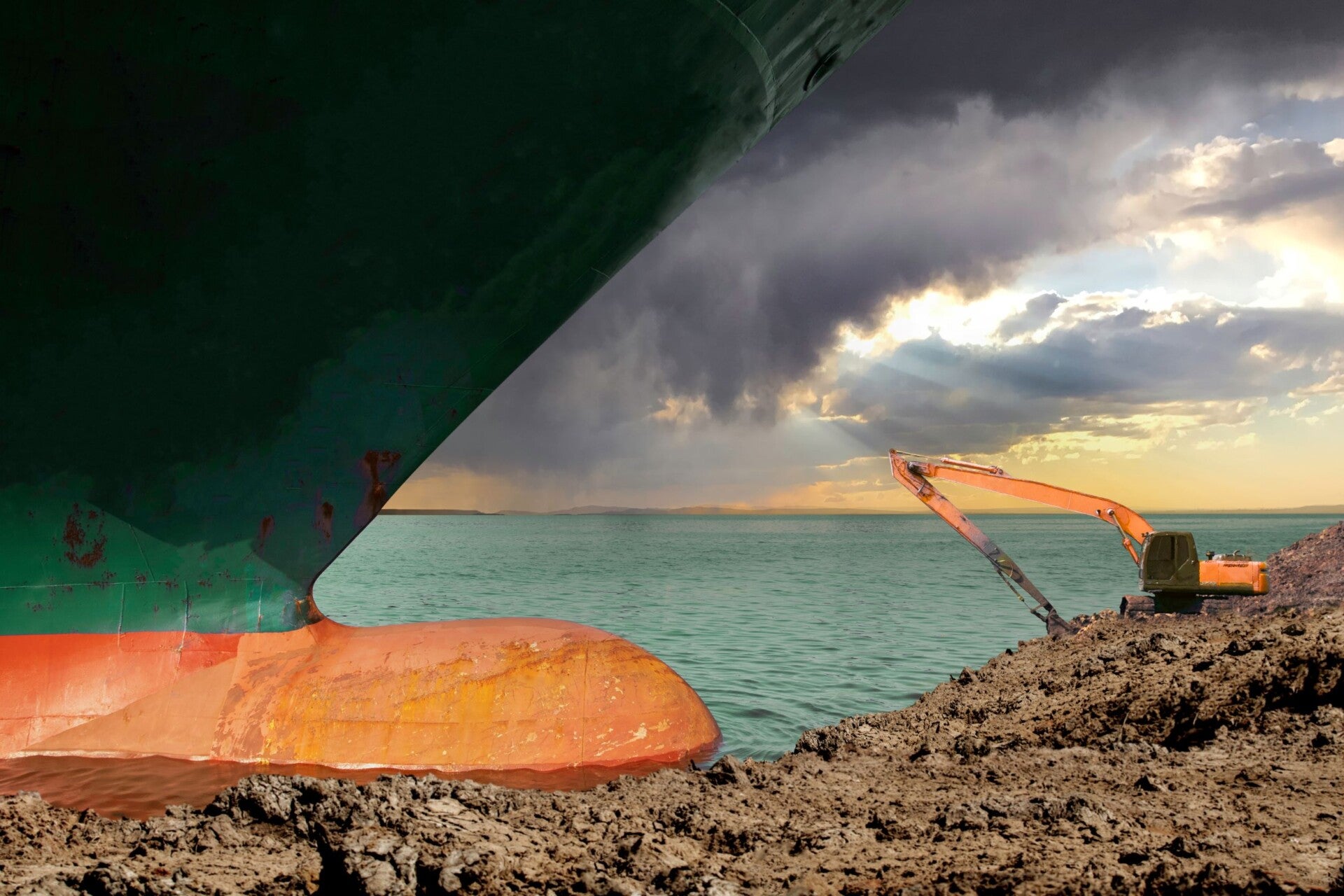
Inside the walls of his home-cum-office in south west London, Alex Stewart held his head in his hands and prepared for the worst. Less than a year after launching his eco-friendly travel goods brand, OneNine5, the entrepreneur watched on in despair as global travel shuddered to a halt following the outbreak of Covid-19 at the start of 2020.
Almost overnight, the brand’s daily sales dropped to single digits as airlines were grounded and millions of people across the globe were ordered to stay at home for lengthy lockdowns. For much of the next 12 months, Stewart was forced to sit tight and hope the storm would pass in time for his fledgling brand to survive.
As lockdowns lifted and travel resumed, so too did sales, but another storm has duly followed. In August, OneNine5’s factory in Shanghai was forced to close because of a rise in Covid-19 cases. Freight costs from China to Felixstowe then tripled from £1,200 to £3,500. Electricity shortages in China have also limited the factory’s output and caused manufacturing lead times to rise from 30 days to at least 50-60.