A national challenge with deep-seated causes
The skills shortage across the manufacturing and engineering sector has been building for years. But there are options for action
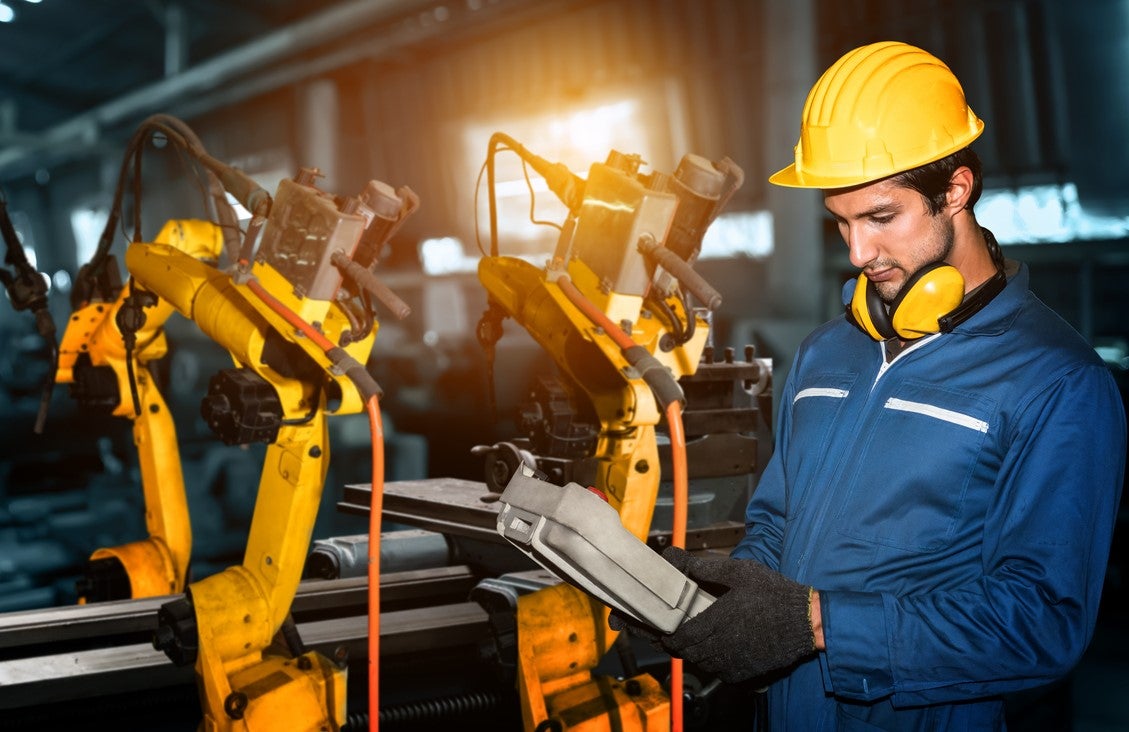
What has caused the skills shortage for industrial companies? It is a long and worrying list.
Demographics is one element. Companies need a steady stream of young people, either to train via the dual training (Duale Ausbildung) process or to engage out of university with advanced technical skills. But there are fewer of them. Germany today has around 800,000 20-year-olds. Ten years ago, it had one million.
And, as this report will show later, many of these young people would prefer to train for jobs in finance rather than industry, partly because they are seen as better-paid and partly because it has been less disrupted by the pandemic.
At the other end of the workforce, early retirement is taking mature, skilled staff away faster than expected. According to the German Pension Fund (Deutsche Rentenversicherung), almost two million Germans aged 63 drew retirement pensions in July 2022. That’s 400,000 more than projected when the early retirement policy was amended in 2014.
The result: a survey by the German Chamber of Commerce (DIHK) in late 2022 said 58% of industrial companies had vacant positions, a rise from the 53% reported a year earlier. It noted that a lack of skills risked vital projects such as the move to carbon neutrality and digitisation.
The Federal Employment Agency’s Institute for Employment Research (IAB) says the issue is not a major, general shortage of mechanical engineers, the problem is a shortage of specialists in key areas such as aerospace, construction, building and industrial supply and waste disposal.
But if current trends continue, the shortfall may move from specialists to generalists. Professor Bernd Fitzenberger, the director of the IAB, says: “While the unemployment rate in Germany’s engineering community is currently just 3%, there is a real risk of a growing shortage in the future.”
Dr Siegrun Brink, a researcher from IfM Bonn, who has researched the impact of skills shortages on small- and mid-sized companies, says the problem is not confined to these companies. She says the shortfall “applies regardless of company size”.
Big companies taking bold moves
Many of the largest companies are taking action. In 2016, to attract more labour from outside of Germany, Volkswagen switched the official company language from German to English, while in December 2022, Siemens announced that it was creating a skills academy to improve digital skill sets.
Gunther Friedl, a senior professor at the Technical University of Munich (TUM), says that the strategy employed by Siemens suggests that engineering companies need to get more skilled engineering graduates through the doors.
He says, “This is not a recent trend. Over the last twenty years, many academic institutions have seen the number of undergraduates decrease”.
Professor Friedl adds that those who prefer to pursue vocational training are also thin on the ground. He explains: “Last year, one-third of apprenticeships could not be filled. However, a decreasing number of apprentices and a fall in university students is mostly due to demographics.”
Friedl believes that technical universities can play a significant role in addressing the talent shortage. “German technical universities have consistently proved themselves to be engineering centres of excellence across the globe. The courses are run in English and German, and unlike many other leading academic institutions, they don’t charge tuition fees. This makes them very attractive for foreign students.”
To illustrate his point, Professor Friedl says that 40% of his university’s 50,000 students are foreign nationals. So could the large influx of non-German students help to solve the labour shortage in the engineering sector?
Says Friedl, “We know that a significant proportion of foreign students are staying in Germany after their studies. But even if they choose to go home, their knowledge of the German education system, coupled with the links they forge with other students, universities, businesses and Germany itself, is a huge plus point for the country in that it could lead to future economic opportunities. That shouldn’t be overlooked.”
The talent shortage has its roots deep in German society. Only a partnership of government, industry, and the education sector can solve it. And some of the solutions – such as changes to the tax system or greater immigration – may generate controversy.
Changes will also take time. Not only does the supply of talent each year need to meet demand, but the shortfall caused by the last ten years needs to be infilled. Without this, industry will be at a competitive disadvantage versus rivals elsewhere in Europe or Asian countries such as South Korea, particularly in fast-growing sectors such as renewable energy.
But companies must act quickly for solutions. So the question is: What actions can they take to acquire talent now?
Solving the problem, a step at a time
Every employer needs to find its own solution to the skills shortage, but becoming an employer-of-choice can help
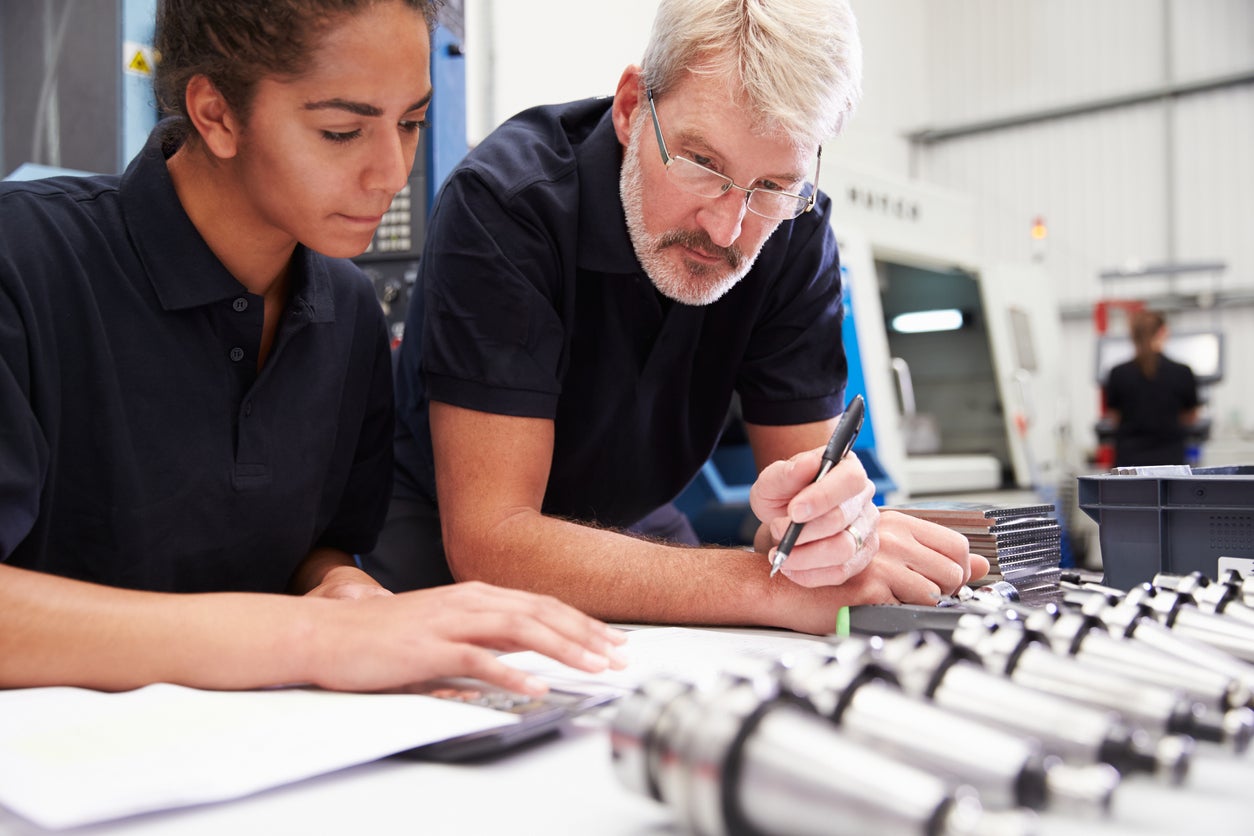
The problems listed in the article above are difficult to solve at a national level. But at the level of individual companies, there is a long list of actions that reduce the risk that skills shortages hold your company back.
Companies can make themselves into an employer-of-choice. Linked to this, they can act to ensure their more mature employees stay in the workforce. Or they can look beyond Germany’s borders for talent.
Heike Lipinski, client director for EMEA at global talent acquisition and talent advisory experts AMS, remarks: “Talent acquisition and retention are inextricably linked.”
Lipinski, who is based in Frankfurt, adds: “Graduates – particularly younger cohorts – greatly value a good work/life balance. Those who are parents need an employer who understands that they need to pick their kids up from the local kindergarten or school on time.
She adds: “This doesn’t always happen in Germany, but when companies put these types of policies in place, it can sometimes give employees a powerful reason to stay.”
AMS prides itself in understanding not just the challenges that German companies face but, more importantly, the individual hurdles that prevent companies from acquiring talented staff. It then works in tandem with each organisation to overcome those obstacles.
“Young people are more and more choosing higher education levels such as university over apprenticeships,” says Lipinski. “Fewer want to take the traditional German route of dual education and working for one company for their whole career.
“In some cases, this has made it much harder for sectors like manufacturing, where specialist skill sets are honed over many years, to fill vacancies.”
General problem, customised solutions
For companies successfully overcoming talent acquisition challenges, language and location are not seen as insurmountable barriers.
Lipinski says enterprises that successfully overcome these challenges “often operate in multiple languages” across different business lines.
She explains: “When we work with these companies, we observe a perfect interplay of the employer value proposition, attractive salaries and benefits, flexible work environment and a complex local, regional and global talent acquisition strategy.”
Brett O’Connor, a client service director for AMS in Germany, notes it is essential to create solutions that reflect each company’s situation.
He says: “Leveraging how we work with clients across the globe and in Germany, we have learnt what it takes to build a high-performing workforce for leading organisations. It starts with talent, sourcing, selecting and retaining the right people.
“This helps AMS and its client to source the best possible fit for the organisation. Sometimes the company may want a German speaker, as the language on the engineering floor or site location may be German.”
Lipinski also notes the role played by AMS’s advisory team. It supports medium-sized and large enterprises by not only analysing the unique situation but also consulting on how to best overcome identified challenges.
When the critical sourcing challenges have been identified, Lipinski says that AMS’s insight teams “can add real value” by analysing the global recruitment market to identify where and how to find world-class talent.
Working in dual languages?
However, when companies look abroad for skills, Lipinski says they will likely need to make other changes.
She says: “Many Mittelstand companies are family-owned businesses that have been operating in highly dispersed areas – all over Germany – for generations. Often they are world leaders in the arcane areas that they work in. Still, when it comes to acquiring talent, they need to widen their horizons and look regionally as well as internationally. That often means changing the culture within their businesses.”
Lipinski says that adjustments will be needed. “Sometimes, they need to change standard work practices on the engineering floor and in office environments. Is it possible, for example, to work in multiple languages?
“Many large companies (but still not all) already do this to integrate non-German speaking employees. However for smaller enterprises, where the German language is deeply embedded in the engineering and production processes, it can be highly challenging. This is a journey that AMS is helping some of them to navigate.”
O’Connor, himself a skilled migrant who has lived in Germany for five years, says that the long-term, national solution to skills shortages lies in “accelerating skilled immigration and international student numbers” and better “integration and up-skilling options into the workforce and the community” as well as “offering a flexible work environment that allows reconciliation of work and family”. It’s also vital to find structural ways to encourage more mature people to stay in the workforce with refreshed skills if necessary.
O’Connor is optimistic: “Germany is a leading global economy at the heart of Europe and a very desirable place to live and work. It has world-class academic institutions and a strong stakeholder governance approach that balances the needs of employees, employers and communities.
He continues, “Germany is also more a country of immigrants than people often realise,” he adds. “If it decides that attracting talented economic migrants is the key to its future prosperity, with statistics showing that people with a migrant background make up over a quarter of the population, it is exceptionally well placed to succeed in further attracting global talent.”
Changing attitudes are a threat to the system
With young people in short supply, competition from other sectors is heating up. So how can engineering and manufacturing fight back?
In decades past, Germany’s manufacturing and engineering sectors were seen as aspirational goals for those looking to enter the world of work. That is changing.
It’s vital to note that this is more than just a prolem with the dual training system: other routes into a career in industry are also attracting fewer young people. For example, at Karlsruhe University of Applied Sciences, there were seven applicants for every position studying mechanical engineering and mechatronics five years ago. Today, there are three. Robert Weiss, dean of faculty, told Deutsche Welle the situation is “frightening”.
He said: “It’s a problem for the university. We want to make our programs as full as possible and [train] all these engineers. But this also has an impact on the industry and for Germany and for the economy if you don’t have enough engineers working.”
Daniel Dombach, director of industry solutions for Europe, the Middle East and Africa at Zebra Technologies, a sensors and systems company that works with a wide range of industries, comments: “I talk with business leaders in manufacturing and engineering regularly, and I’m hearing that these industries are struggling to hire enough talent, train them fast enough, and retain them long-term.”
A closer look at the problem
Dombach has a long list of challenges constricting the flow of young people into manufacturing and engineering, including “demographic decline, changes in immigration, and the impact of pandemic lockdowns on job security and industry operations.”
This report has already looked at demographics, but the issue of cultural change is arguably as important. The training contracts most popular with young people are those seen as future-proof (such as e-commerce and logistics) or that lead to highly-remunerated jobs such as banking. True, industrial firms offer relatively high training allowances, often 10% or more than those provided by the hospitality industry. But they are still around 10% lower than those provided by banks. In addition, industrial and engineering training was hit hardest by the pandemic because it was much harder to switch to remote learning. It also disrupted industry/school links.
One option to solve the skills shortage when it comes to the pipeline of new workers is to automate elements of the engineering and manufacturing sectors that can be handed over to technology.
Dombach comments: “Autonomous mobile robots, industrial machine vision, radio frequency identification, enterprise mobile computing and communication software are being used to better augment and connect workers, and speed up and automate workflow processes in warehouses and factories.” But efficiency can only go so far.
Making manufacturing attractive
A DIHK study of Generation Z training and employment gave a list of techniques employers are using to improve their attractiveness to young people. The most frequent, used by 58%, was to flatten hierarchies so that young people feel like a team member rather than an apprentice from day one. Giving trainees better IT equipment and creating a more streamlined, modern hiring process are also priorities. They may also boost training allowances with incentives for good learning outcomes, housing subsidies, or other “goodies”.
However, by the time they are ready to join the workforce, many young people may have already decided to pursue non-industrial careers. A more foundational approach is to use school liaison schemes to make studying those subjects attractive and acclimatise students to entering the field.
The government holds some responsibility for offering those schemes, but businesses can ably support them. For example, Igus, a Cologne-based motion plastics company employing more than 4,500 people worldwide, runs a Young Engineers’ Support (YES) programme which goes into schools and supports students wishing to pursue a career in the industry. “Through this project, highly innovative projects have been realised, and these can be used to show how innovative engineering careers can be,” says Frank Blase, the company’s chief executive.
Igus makes a particular effort to reach female students. (The IAB notes that female engineering students account only for around 26% of the total engineering student population.) “Igus offers girls’ days where female students are invited to explore technical jobs at Igus,” Blase says. “And we also offer school visits.” Those visits don’t just play up the hard engineering skills involved in the world of work, but also some of the so-called “softer” streams, including how engineering can help the environment and tackle climate change.
Blase realises that it’s important to meet would-be workers where they want to engage, which is why the company works hard to present opportunities in non-traditional means. The company has developed a series of tools and services it bundles under the banner of Enjoyneering designed specifically to intrigue younger generations of potential staff members. “To engage with young people, you have to engage more with digital technology,” he says. “This makes engineering more relevant, and interesting.”
The problems with Duale Ausbildung
Duale Ausbildung (dual training) has been such a success that many countries have tried to copy it. Germany has bilateral cooperation deals with 11 countries to promote similar systems, and many German companies offer similar schemes in their overseas operations. But there are clear signs of problems at home:
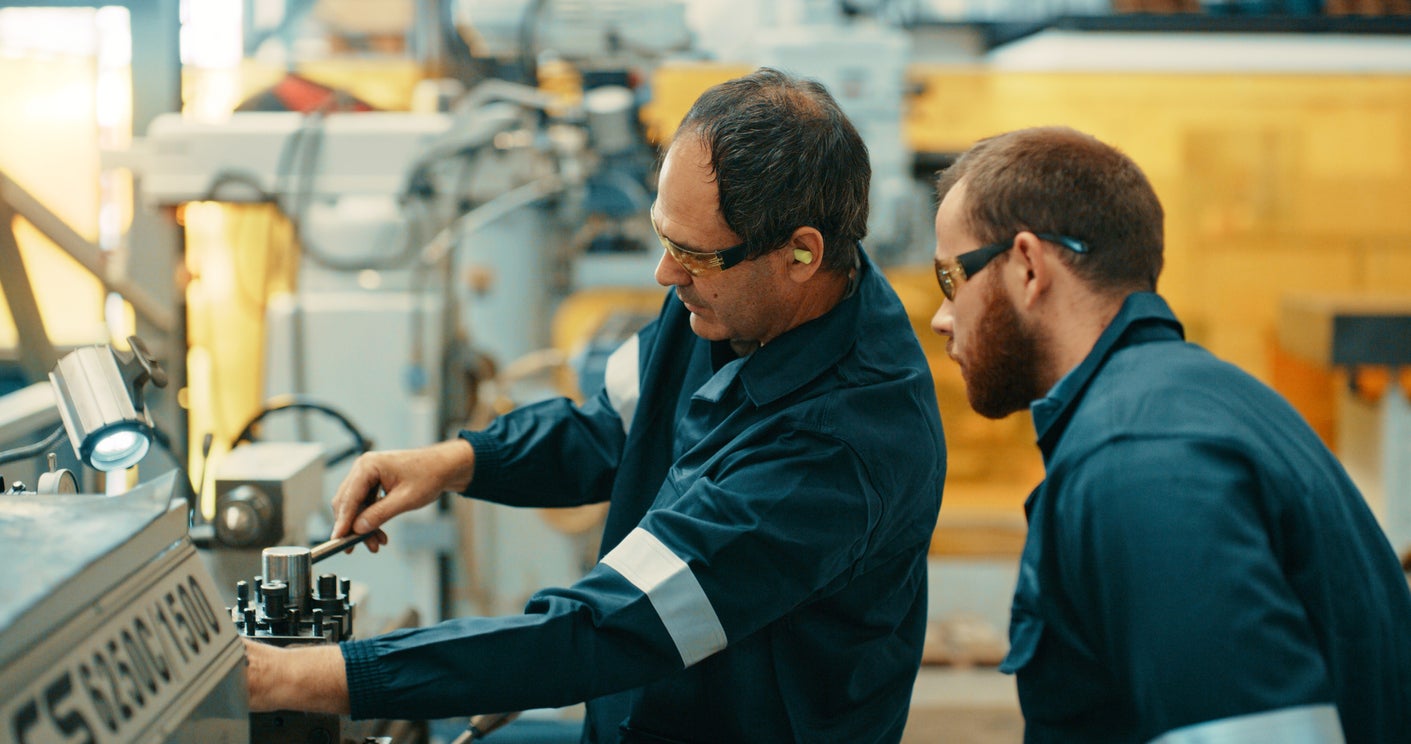
Looking in new places for skills
The Federal government is making it simpler to get talent from outside of Germany. But companies doing this may need to embrace cultural change
The arithmetic does not lie: unless there is a sharp increase in the local birth rate, the only way that Germany can avoid a continuing decline in working-age people is to import them from elsewhere.
“Certainly Germany is facing, like other European countries, a major democratic turning in the sense that new cohorts entering the labour workforce are much smaller than older cohorts who are retiring,” says Panu Poutvaara, a member of Germany’s Expert Council on Integration and Migration, and professor of economics at the University of Munich.
Immigration has long propped up what would have been a declining German population for years, says Professor Poutvaara – and so it’s important to acknowledge the benefits it brings to the country rather than any risks or issues it raises.
The most recent Destatis projections are stark: in a low net migration scenario, the working-age population goes from 51.4 million in 2021 to 45.9 million in 2040. Thankfully this low-migration scenario looks increasingly less likely. The Skilled Immigration Act of 2020, the influx of people from Ukraine, and other sources of human capital are making this painful reduction of the national working-age population less likely.
However, Professor Friedl of the Technical University of Munich says those given sanctuary by the German state were not economic migrants. Therefore in most cases, their skill sets “did not match the needs of the German engineering labour market”.
He says the debate being played out in the Federal parliament and the national media “is how Germany can redesign its immigration laws so that they directly address the skills shortage”.
A card of opportunity
One initiative that aims to ensure skills are available is the Chancenkarte, or opportunity card, which enables workers from abroad with requisite in-demand skills to enter the country more easily. It’s hoped to come into force by the end of 2023. “We want to make it easier and faster for foreign skilled workers to find their way to Germany,” interior minister Nancy Faeser and labour minister Hubertus Heil said recently in a joint statement. The card will be issued on a points-based system, although exact details have yet to be decided.
But employers are already ahead of the game. In a 2022 survey, 39% of manufacturers told the German Chamber of Commerce and Industry (DIHK) they are already acquiring talent outside Germany’s borders.
Two key issues follow from this: first, how can Germany increase its attractiveness to foreigners, especially those with in-demand skills? And second, how can these workers be integrated once they arrive to maximise their value to their employer?
On the first issue, the outlook is mixed. Germany’s attractiveness for highly-qualified skilled workers fell from the 12th to 15th in 2022 in a survey carried out for the Organisation for Economic Co-operation and Development with the help of the non-profit foundation Bertelsmann Siftung. Bertelsmann Siftung CEO Ralph Heck in a statement that “The international comparison clearly shows what Germany needs to do to make the migration of skilled workers, which is so important for our country, even better.”
Looking at the list of most-favoured countries, it is striking that New Zealand, Australia, the UK, the USA, Canada and Ireland all sit above Germany in the rankings: a clear message that English-speaking countries have a competitive advantage when it comes to attracting talent. And they are not standing still: at the same time that Germany was passing the law creating the Chancenkarte, Canada announced a new visa system that also aims to attract skilled workers.
There is better news elsewhere in the survey, though: Germany is the second-most-favoured destination for international students (beaten only by the US). This suggests that bringing more international students and persuading them to stay in Germany after qualification could be a route to reducing skill shortages. Of course, this would be slower than attracting workers with ready-to-use skills. But they may also put down roots and contribute to the economy until retirement, in contrast to many non-German workers who may stay only for a few years and then return to their home country.
Effective deployment
Administrative measures such as the Chancenkarte and the Jobseeker Visa are parts of a solution. But employers still need to find ways to deploy them effectively. (Although some entry routes to Germany require German proficiency to B1 level, this is intermediate rather than fluent.)
Tesla is one company trying to remain competitive in a labour market where the workers, rather than their employers, hold the power to pick and choose. At its Berlin Gigafactory, it offers English-language shifts for workers who still need to gain proficiency. This means it can pick staff based on their work skills rather than their command of the German language.
“It’s certainly a good idea, and I would like to see companies doing that at a larger scale,” says Professor Poutvaara, who suggests that companies operating on the Polish border could consider a similar scheme to attract workers from that country.
“If a company has enough workers who speak Polish to have a Polish-language team, I think there’s nothing problematic in doing so,” he says. “Companies need to be creative, and to explore that possibility.” Targeted marketing spending on countries which could supply workers could reap massive benefits in the long run.
It’s not just employers who need to change: the Federal government needs to also. For example, Poutvaara suggests that the government could improve online access to book appointments that enable workers from non-EU countries to arrange visas in English. “One problem is currently getting an appointment can take a very long time,” he says. “This process needs to be sped up.” But it’s also essential to improve the ability for workers in the EU to feel encouraged to work in Germany – particularly those from eastern Europe as they can provide a quick fix. “The geographic distance is much shorter,” says Pouvaara. “If they want to go to visit their family or relatives, it’s much easier for them.