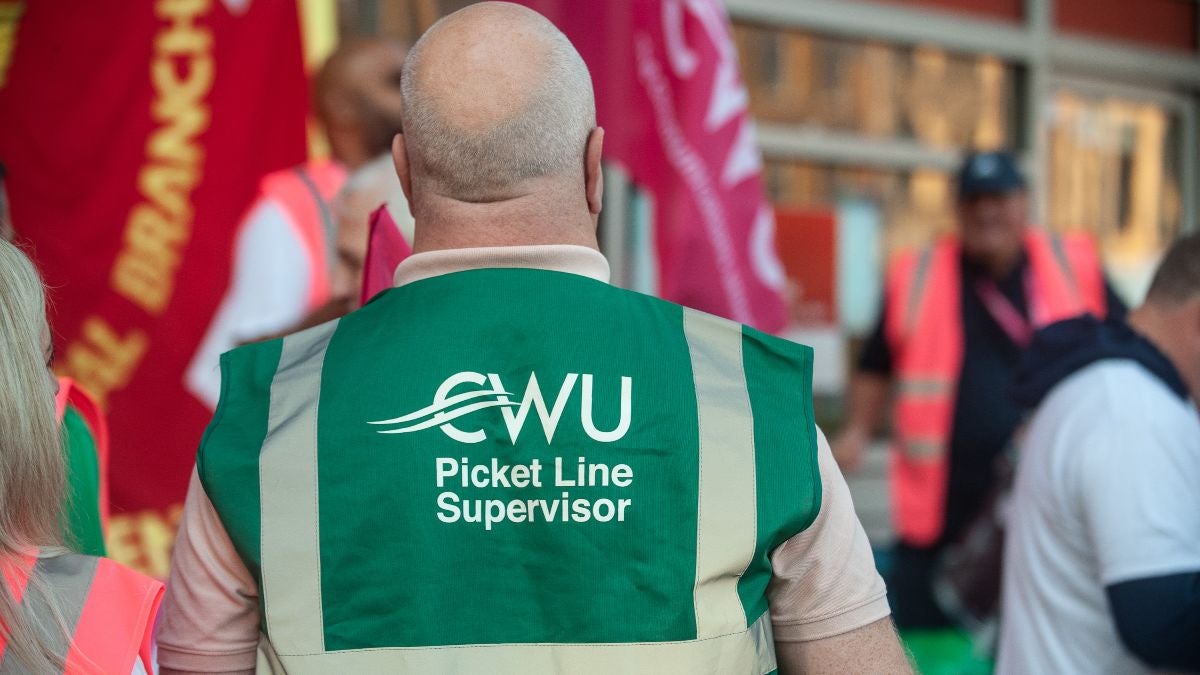
The UK supply chain was starting to make a recovery from Brexit and Covid this summer, only to be derailed by a series of strikes across industry.
The cost-of-living crisis has driven industrial action by workers in the railways, the Royal Mail and the UK’s largest port, Felixstowe, over increasingly stretched pay packets.
The logistics sector, highly praised for continuing to fulfil deliveries throughout the pandemic, has also been a hotbed of dissatisfaction, with DHL distribution centre workers in Scotland voting to walk out. Amazon workers in Tilbury have staged a protest over working conditions and pay, while HGV drivers at dairy firm Muller have gone on strike in protest against imposed rota changes.
These concerns in the logistics sector are not new. A City and Guilds report earlier this year said the sector is likely to have worker shortages of 400,000 by 2026 because of low pay and unattractive working conditions.
It found that only 23% of people said they would consider a job in logistics with 8% saying they were willing to drive an HGV. There have been reports of warehouse staff employed on insecure, zero-hour contracts, subject to firing and re-hiring on less favourable terms and even claims of timed toilet breaks.
As a result, according to the 2021 Stress & Mental Health study, up to 27% of employees in the transport and logistics sector had taken time off work for mental health reasons.
When it comes to pay, according to Statista, the median annual full-time wage for transport and storage workers in the UK in 2021 was £31,000. This is compared with the top sector – financial services at £43,000 and the lowest of £20,000 in food service.
We’ve recognised the cost-of-living issue and want to ensure our staff are not disgruntled
Wouter Satijn, sales director at materials handling group Joloda Hydraroll, says: “Lorry driving, and working in logistics in general, is a demanding profession. It’s very physical and drivers are under pressure to deliver goods to their destination within the allotted travel time. Who wants to work in a cold, damp and potentially dangerous unloading bay?”
So, what can be done to improve staff engagement and wellbeing in the sector, retain and attract talent and toughen up the supply chain?
Higher pay is an obvious solution. Logistics UK stated that HGV driver wages rose 12% in the year to January 2022, partly due to shortages. Aldi has agreed a wage increase of up to 9% for workers in its UK regional distribution centres. And the union Unite recently helped to secure a 12% pay rise for Sainsbury’s HGV drivers in Basingstoke.
North-east-based Moody Logistics and Storage has doubled the usual reward percentage from its profit-related pay scheme for employees. “We’ve recognised the cost-of-living issue and want to ensure our staff are not disgruntled,” says managing director Caroline Moody.
It is only part of a raft of staff benefits the company offers, such as a minimum of 28 days of paid annual leave, an auto-enrolment pension scheme, health care and company uniforms.
“We are trying to be a family business, not just by name but by nature too,” says Moody. “We also have annual company awards and little things such as buying each member of staff a family barbecue pack the Friday before last year’s May bank holiday. All of these measures combine to help with our productivity and retention figures. I can’t remember the last time we lost a member of staff.”
Despite this success, it’s clear that rewards, like pay, are still not enough to keep all logistics staff happy. When the Amazon walkout was taking place the organisation highlighted its offering of private medical insurance, life assurance, income protection, subsidised meals and a company pension plan.
Suzanne Marshall, head of clinical strategy at wellbeing experts GoodShape, isn’t surprised that some staff remain unhappy. She says companies need to be careful that they don’t offer benefits which aren’t addressing the right problems.
“Times are tough. Crippling staff shortages in the sector and spiralling living costs are adding pressure to everyone and while a drinks fridge in a breakout room might be a nice perk, it isn’t going to improve wellbeing or staff retention,” she says.
Instead, Marshall urges a clearer focus on addressing operational issues such as the sector’s working patterns.
“Logistics typically has high levels of staff working remotely on shift patterns. This adds challenges when it comes to communicating and understanding the issues and barriers to wellbeing,” she says. “One logistics company we worked with was seeing higher levels of absence in one shift. By unpicking their data and insights they established that not enough time was being given for drivers to hand over to the next member of staff. This resulted in insufficient time for drivers to adjust their chair position and subsequently a higher level of musculoskeletal-related absences. Logistics firms need a better understanding of the cause of staff absences so they can provide better support.”
Akshatha Veerendra is principal consultant, energy, sustainability and wellness at RPS Group. She says that logistics firms, inspired by the pandemic, are trying to improve employee experiences by reimagining warehouse design.
As employers we always complain we can’t find the right people, but you have to look after them in the right way.
This includes sites with more natural light, green pathways and even running tracks on roofs. It means more space aiding health and safety among the forklifts and pallets, as well as meditation and training zones.
“We’re seeing competition between companies looking to develop the best sites to increase employee engagement, reduce absences and missed deliveries but also meet ESG requirements,” explains Veerendra.
Satijn calls on logistics firms to also invest in warehouse and logistics automation to help up-skill staff to more added-value roles. “Automating the warehouse is an essential next step to gaining efficiencies that will also positively impact driver satisfaction and productivity,” he states. “As employers, we always complain we can’t find the right people, but you have to look after them in the right way. If we don’t move at a higher and faster pace, it will mean more empty shelves in our stores and a big impact on everyday life.”
But Moody says it can be hard for logistics firms to find the time and financial headroom to make the necessary changes. “When you’re in a good position and making money, you can afford to do these things. It then becomes self-fulfilling with better engagement and productivity,” she says. “With a lot of hauliers, it is about making that initial step.”
Veerendra agrees that change will take time. “We’re seeing improvements but it is slow. There needs to be a cultural shift in the sector throughout the supply chain around engagement and wellbeing.”
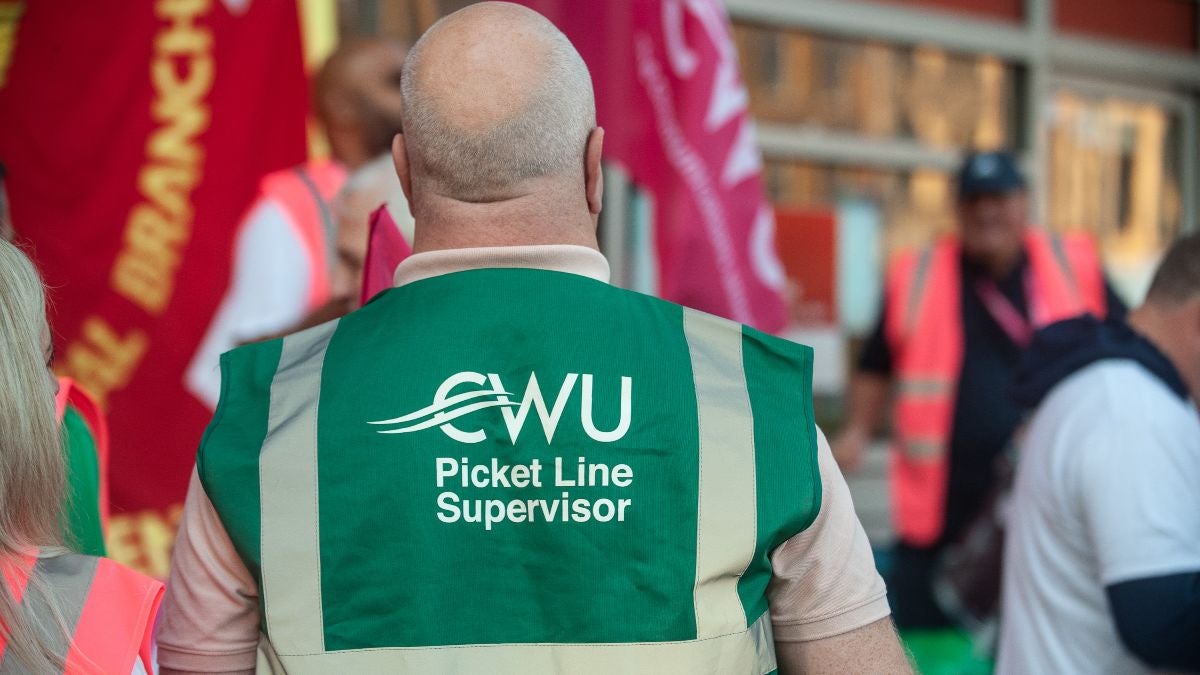
The UK supply chain was starting to make a recovery from Brexit and Covid this summer, only to be derailed by a series of strikes across industry.
The cost-of-living crisis has driven industrial action by workers in the railways, the Royal Mail and the UK’s largest port, Felixstowe, over increasingly stretched pay packets.
The logistics sector, highly praised for continuing to fulfil deliveries throughout the pandemic, has also been a hotbed of dissatisfaction, with DHL distribution centre workers in Scotland voting to walk out. Amazon workers in Tilbury have staged a protest over working conditions and pay, while HGV drivers at dairy firm Muller have gone on strike in protest against imposed rota changes.