Additive manufacturing is regarded as the cornerstone technology of the third industrial revolution. It allows you to create three-dimensional solid objects from a digital model, by adding successive layers of material or by hardening powders or fluids.
The ManSYS project focuses on developing complete decision-making and robust supply chain management systems for metal additive manufacturing, enabling production and delivery of quality-assured, highly customised products and services.
METAL ADDITIVE MANUFACTURING
Additive manufacturing (AM) or 3D printing covers a multitude of production technologies. Well known AM technologies are stereo lithography (SLA), selective laser melting (SLM) and fused deposition modelling (FDM).
All these technologies work with the same principle of adding or hardening material layer upon layer. Traditional manufacturing technologies, such as milling, subtract material to create a desired model. The excess material is turned into waste. With additive manufacturing technologies, only the material required is used, bringing the amount of waste down to practically zero.
But there are other benefits of AM, says Sozon Tsopanos, principal project leader at TWI and project manager of the ManSYS project. These are:
- Complex parts can be designed and produced without assembly;
- New geometries can be produced that traditional methods cannot produce;
- Prototypes can be produced quickly;
- Individualisation is possible at low cost;
- Small series of unique or redesigned parts become an economically viable option.
GOALS OF MANSYS PROJECT
The ManSYS project is an initiative of 12 partners, supported by the European Commission (EC), to develop an online platform for the design and procurement of 3D-printed parts and products.
Three key elements will be developed:
- Decision-support software aiding end-users to decide whether 3D printing is applicable in their specific situation;
- A supply chain management system that allows for easy adoption and management of 3D printing in the production process;
- A support network to design or redesign new or better products, realising user-oriented high-value-added solutions.
To demonstrate the benefits of ManSYS, essential parts from Smith & Nephew and Wisildent, GE Aviation will be produced via the platform.
In addition, to ensure that the quality of the products complies with market and customer requirements, much attention will be given to the development of the quality-assurance and quality-control processes. Also, the software to integrate various supply chain and business management systems will be developed.
The ManSYS project focuses on developing complete decision-making and robust supply chain management systems for metal additive manufacturing
“Quality control and quality assurance are essential for the acceptance of an additive manufacturing supply chain,” says Luis Portoles of AIMME. “We’ve already developed a decision-making tool and a workflow set-up geared towards the requirements of the aviation, medical and dental industries.”
ManSYS platform members will be trained to use the platform and trust created in the high-quality output it delivers, through a technical workshop.
MANSYS CONSORTIUM
The 12 companies developing and testing the platform bring ample experience in high-quality manufacturing of complex parts, software development, material and process quality control, and business modelling, concludes Wieke Ambrosius of Berenschot. Together they cover the entire supply chain
Follow the development of the platform or get involved in the ManSYS network as a service provider or future user at www.mansys.info
METAL ADDITIVE MANUFACTURING
GOALS OF MANSYS PROJECT
MANSYS CONSORTIUM
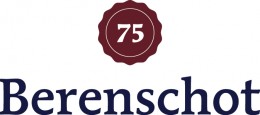